Why Regular Maintenance is Key to Maximizing Machinery Lifespan
.png)
Keeping machinery in good shape is super important for any business that relies on it. Regular maintenance isn’t just a nice-to-have; it’s a must if you want to keep everything running smoothly and avoid costly breakdowns. In this article, we’ll explore why regular maintenance is key to maximizing machinery lifespan and how it can save you time and money in the long run.
Key Takeaways
- Regular maintenance boosts equipment reliability and prevents unexpected failures.
- It can significantly extend the lifespan of your machinery and reduce downtime.
- Identifying early signs of wear can save you from costly repairs later on.
- Having a solid maintenance program can improve safety standards in your workplace.
- Training your team on maintenance best practices enhances efficiency and performance.
Understanding The Importance Of Regular Maintenance
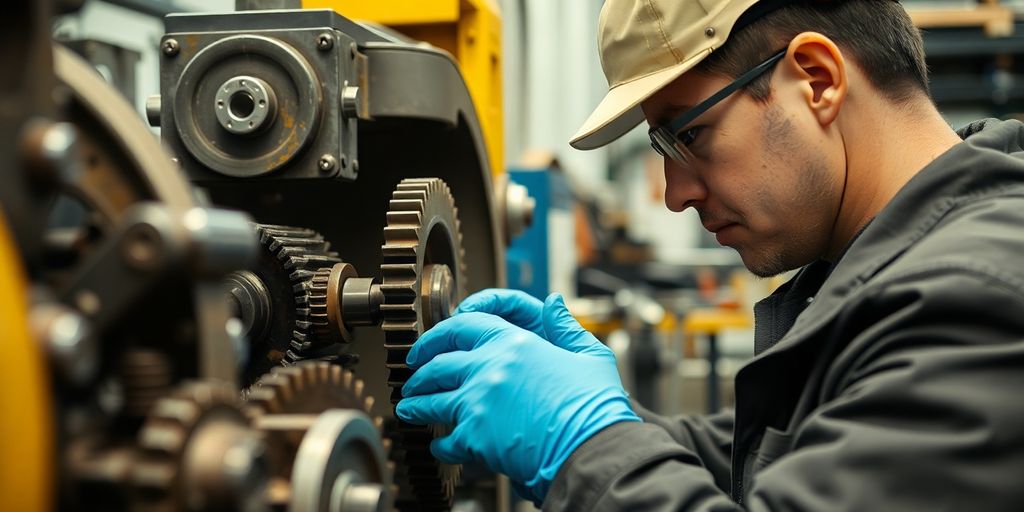
Enhancing Equipment Reliability
Think of your machinery like your car. You wouldn't skip oil changes, right? Same goes for industrial equipment. Regular maintenance keeps everything running smoothly and reduces the chance of unexpected failures. Reliability is the name of the game. It's about making sure your machines do what they're supposed to when they're supposed to, without any drama.
Preventing Costly Breakdowns
Okay, let's be real, nobody likes surprise repair bills. Preventative maintenance is like insurance against those nasty surprises. By catching small problems early, you avoid them turning into huge, expensive disasters. It's way cheaper to replace a worn belt than to rebuild an entire machine after it seizes up. Trust me, your wallet will thank you.
Boosting Operational Efficiency
Ever tried running a marathon with a pebble in your shoe? Not fun, right? Machines are the same way. When they're not properly maintained, they don't run at their best. Regular maintenance ensures everything is optimized, so you get the most out of your equipment. More output, less energy consumption, and happier employees – it's a win-win-win.
Skipping maintenance is like ignoring a leaky faucet. It might seem like a small issue at first, but it will eventually lead to bigger problems, like water damage and a higher water bill. Regular maintenance is about being proactive and addressing potential issues before they escalate into major headaches.
Key Benefits Of Preventative Maintenance
Preventative maintenance is more than just a good idea; it's a necessity for keeping your machinery running smoothly and your business efficient. It's about taking a proactive approach to equipment care, and the payoffs can be huge. Let's look at some of the key advantages.
Extended Machinery Lifespan
Regular maintenance is like giving your equipment a long and healthy life. By keeping components in good shape, you're essentially preventing premature wear and tear. This means your machines will last longer, reducing the need for frequent replacements. It's a simple concept, but the impact on your bottom line can be significant. Think of it as investing in the longevity of your assets.
Reduced Downtime
Nobody likes downtime. It's disruptive, costly, and frustrating. Preventative maintenance helps minimize unplanned downtime by identifying and fixing potential problems before they cause a breakdown. Imagine catching a small leak in a hydraulic system before it leads to a complete system failure. That's the power of preventative maintenance. It keeps your operations running smoothly and predictably.
Improved Safety Standards
Safety should always be a top priority. Well-maintained machinery is safer to operate. Regular checks and maintenance help ensure that equipment is functioning correctly, reducing the risk of accidents and injuries. This not only protects your employees but also helps you avoid potential legal and financial repercussions. It's a win-win situation.
Implementing a solid preventative maintenance program is not just about fixing things when they break. It's about creating a culture of care and responsibility that benefits everyone involved. It's about investing in the future of your operations and ensuring that your equipment is always ready to perform at its best.
Identifying Maintenance Needs Early
It's easy to overlook the subtle signs that your machinery needs attention. But catching these early can save you a ton of money and headaches down the road. Think of it like going to the doctor for a check-up – you're looking for potential problems before they become serious.
Recognizing Warning Signs
Sometimes, your equipment will practically scream for help. Other times, it's more of a whisper. Being able to distinguish between normal operation and a cry for maintenance is key. Here are a few things to watch out for:
- Unusual noises: Grinding, squealing, or banging sounds are never a good sign. They often indicate worn bearings, loose parts, or lubrication issues.
- Decreased performance: Is your machine not producing as much as it used to? Is it running slower? This could point to a variety of problems, from clogged filters to failing components.
- Visible wear and tear: Obvious signs like rust, cracks, leaks, or frayed wires should be addressed immediately. Don't ignore the obvious!
Monitoring Performance Metrics
Numbers don't lie. Keeping track of key performance indicators (KPIs) can give you valuable insights into the health of your machinery. Here are some metrics to consider:
- Output rate: Track how much your machine produces over time. A sudden drop could indicate a problem.
- Energy consumption: A spike in energy usage could mean your machine is working harder than it should be.
- Error rates: Are you seeing more errors or rejects than usual? This could be a sign of a malfunctioning component.
By closely monitoring these metrics, you can identify potential problems before they lead to breakdowns. It's like having a built-in early warning system for your equipment.
Conducting Regular Inspections
There's no substitute for a good old-fashioned visual inspection. Routine inspections and checks are essential. Set up a schedule for regular walk-arounds, and train your team to look for anything out of the ordinary. Here's a simple checklist to get you started:
- Check fluid levels (oil, coolant, etc.).
- Inspect belts and hoses for cracks or wear.
- Listen for unusual noises.
- Look for leaks or spills.
By being proactive and paying attention to the warning signs, you can keep your machinery running smoothly and avoid costly downtime.
Best Practices For Effective Maintenance Programs
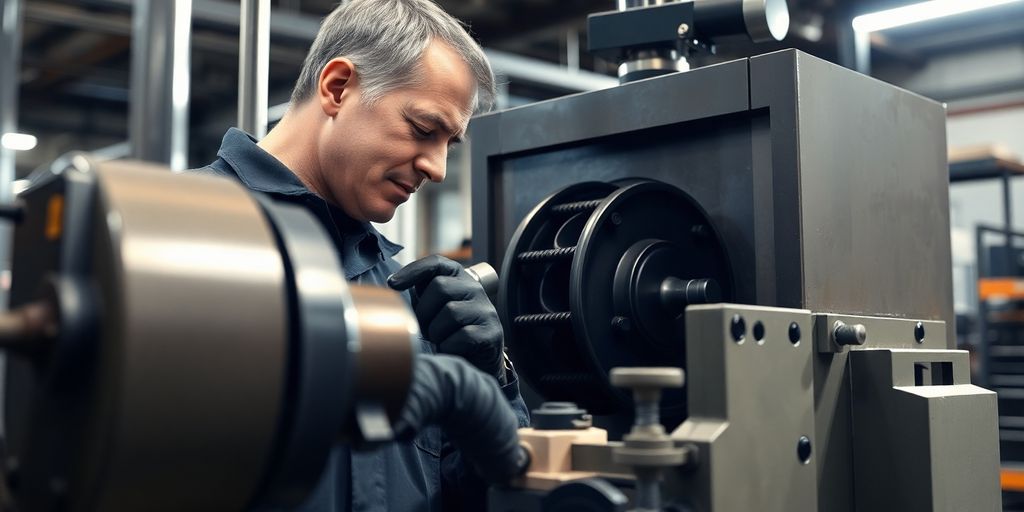
Scheduled Inspections and Cleaning
Okay, so you want your machines to last? Think of it like this: regular check-ups and a good scrub are essential. It's not rocket science. Set up a schedule, stick to it, and make sure everything is clean. This helps catch small problems before they turn into big, expensive headaches. It's like going to the dentist – you might not want to, but you'll be glad you did. A preventive maintenance plan can save you a lot of trouble down the road.
Component Replacement Strategies
Don't wait for things to break down completely. That's just asking for trouble. Have a plan for replacing parts before they fail. This might mean keeping an eye on how long parts usually last and swapping them out at regular intervals. Or, it could involve using sensors to monitor the condition of components and replacing them when they show signs of wear. Either way, proactive replacement is the name of the game. Here's a simple breakdown:
- Track component lifecycles.
- Implement predictive maintenance using sensors.
- Keep a stock of critical replacement parts.
Documentation and Record Keeping
If you didn't write it down, it didn't happen. Seriously, keep detailed records of all maintenance activities. This includes inspections, repairs, replacements, and anything else related to keeping your machinery in tip-top shape. Good documentation helps you track trends, identify recurring problems, and make informed decisions about maintenance strategies. Plus, it's super helpful when you need to troubleshoot issues or plan for future maintenance.
Think of your maintenance records as a machine's medical history. The more information you have, the better you can diagnose and treat any problems that arise. It's all about being prepared and informed.
Choosing The Right Maintenance Approach
Okay, so you're on board with regular maintenance. Great! But now comes the tricky part: figuring out how to actually do it. There's no one-size-fits-all answer here. What works for a small shop might be a disaster for a large factory, and vice versa. It really boils down to your specific needs, resources, and the complexity of the maintenance tasks you're dealing with.
In-House Maintenance Advantages
Having your own maintenance team can be super convenient. You've got people on-site who know your equipment inside and out. Plus, you can respond to problems quickly without waiting for an outside contractor. However, it also means investing in training, tools, and a parts inventory. It's a commitment, but it can pay off big time if you have the volume to justify it.
- Faster response times to equipment issues.
- Greater control over maintenance schedules.
- Potentially lower costs for routine maintenance.
Factory Rebuilds Benefits
Sometimes, you need the big guns. Sending equipment back to the factory for a rebuild can seem extreme, but it's often the best way to ensure a thorough overhaul. They'll tear it down, inspect every component, replace worn parts, and basically bring it back to like-new condition. Plus, factory rebuilds often come with warranties, which is a nice peace of mind.
Factory rebuilds are a good option when dealing with highly specialized or complex machinery. The manufacturer has the expertise and specialized tools to perform the job correctly, ensuring optimal performance and longevity.
Evaluating Your Options
So, how do you decide? Start by assessing your internal capabilities. Do you have the skilled personnel and equipment to handle most maintenance tasks? If so, in-house maintenance might be the way to go. If you're dealing with highly specialized equipment or need a complete overhaul, factory rebuilds could be a better choice. Consider these factors:
- The complexity of your machinery.
- Your budget for maintenance.
- The availability of skilled technicians.
Ultimately, the best approach is the one that keeps your equipment running smoothly and minimizes downtime. Don't be afraid to mix and match strategies to find what works best for you.
Training Your Maintenance Team
Your maintenance team is the backbone of your preventative maintenance programs. Without a skilled and knowledgeable team, even the best-laid plans can fall apart. It's not just about hiring people; it's about investing in their growth and making sure they have what they need to keep things running smoothly.
Essential Skills and Knowledge
First off, you need to make sure your team has the core skills. This means a solid understanding of mechanics, electrical systems, and whatever specific equipment you're using. But it's more than just knowing how things work. They need to be able to troubleshoot problems, read schematics, and use diagnostic tools effectively. A good foundation in safety procedures is also non-negotiable. It's about keeping everyone safe and preventing accidents.
Ongoing Training Programs
Technology changes fast, and so does equipment. That's why ongoing training is so important. Regular training sessions keep your team up-to-date on new technologies, maintenance techniques, and safety protocols. Consider these options:
- Vendor training: Get training directly from the equipment manufacturers.
- Online courses: There are tons of online resources for specialized skills.
- Cross-training: Teach team members different skills to increase flexibility.
Utilizing Technology for Efficiency
These days, there's a ton of tech that can make maintenance way more efficient. Think about using CMMS (Computerized Maintenance Management System) software to track work orders, manage inventory, and schedule maintenance. Mobile devices can also be a game-changer, allowing technicians to access information and update records on the spot. It's all about using technology to streamline processes and reduce downtime.
Investing in your maintenance team is an investment in the longevity and reliability of your equipment. A well-trained and equipped team can identify problems early, perform maintenance effectively, and keep your operations running smoothly. It's a win-win for everyone.
Monitoring And Adjusting Maintenance Strategies
It's easy to think once a maintenance plan is in place, you can just set it and forget it. But that's not really how it works. Things change, equipment ages, and new technologies emerge. So, keeping an eye on how well your maintenance strategy is actually working and making adjustments is super important.
Analyzing Performance Data
The first step is to gather data. You need to know what's going on with your equipment. This means tracking things like:
- Downtime frequency and duration
- Repair costs
- Equipment lifespan
- Overall equipment effectiveness (OEE)
By looking at this data, you can spot trends and see where your maintenance plan might be falling short. For example, if you notice a particular machine is breaking down more often than it used to, it might be time to adjust the maintenance schedule or replace some parts.
Feedback Loops for Improvement
Data is great, but it doesn't tell the whole story. You also need to get feedback from the people who are actually doing the maintenance work. They're the ones who see what's really going on with the equipment, and they might have some good ideas for how to improve the maintenance process.
Talk to your maintenance team regularly. Ask them what's working, what's not, and what they think could be done better. This feedback can be invaluable in fine-tuning your maintenance strategy.
Adapting to New Technologies
Maintenance isn't a static field. New technologies are constantly emerging that can help you improve your maintenance practices. For example, condition monitoring systems can use sensors to track the health of your equipment in real-time, allowing you to identify potential problems before they lead to breakdowns. Similarly, predictive maintenance software can use machine learning to forecast when equipment is likely to fail, allowing you to schedule maintenance proactively.
Staying up-to-date on these technologies and adapting your maintenance strategy accordingly can help you keep your equipment running smoothly and efficiently for years to come.
Wrapping It Up: The Importance of Regular Maintenance
In the end, keeping up with regular maintenance is just smart business. It’s not just about fixing things when they break; it’s about preventing those breakdowns in the first place. By staying on top of maintenance, you can save money, avoid downtime, and keep your machinery running longer. Plus, it helps ensure a safer work environment for everyone. So, whether you’re checking off a maintenance checklist or scheduling those routine inspections, remember that a little effort now can lead to big benefits down the road. Don’t wait for problems to arise—make maintenance a priority and watch your equipment thrive.
Frequently Asked Questions
Why is regular maintenance important for machinery?
Regular maintenance helps keep machines working well, prevents big problems, and extends their life.
What are the benefits of preventative maintenance?
Preventative maintenance can make your machines last longer, reduce downtime, and improve safety.
How can I tell if my equipment needs maintenance?
Look for signs like strange noises, poor performance, or visible damage to know when maintenance is needed.
What are some best practices for maintaining machinery?
Best practices include regular inspections, cleaning, replacing worn parts, and keeping detailed records.
Should I handle maintenance in-house or send it to the factory?
In-house maintenance allows for quick fixes, while factory rebuilds offer thorough inspections and warranties.
How can I train my maintenance team effectively?
Provide essential training, ongoing education, and use technology to help your team work more efficiently.