Why Preventative Maintenance is Key for Heavy Equipment
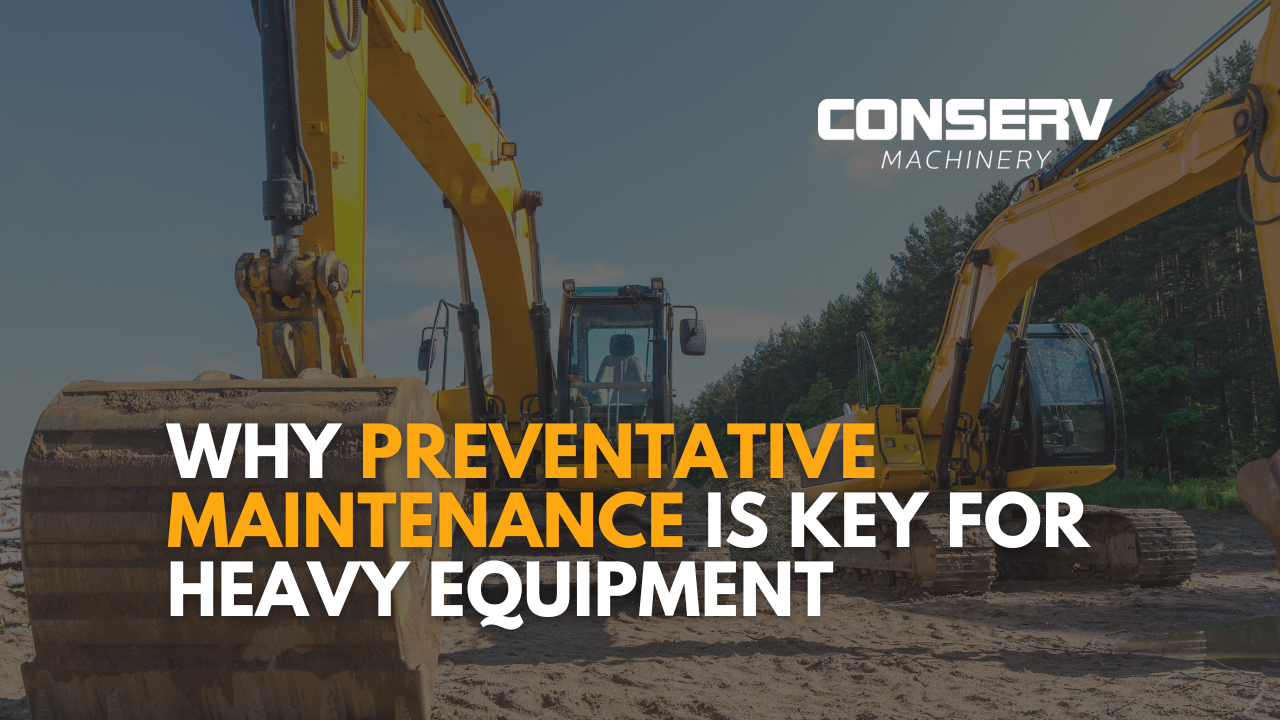
Why Preventative Maintenance is Key for Heavy Equipment
Preventative maintenance is crucial for heavy equipment, ensuring that machinery operates smoothly and efficiently over time. By taking a proactive approach to maintenance, companies can avoid costly repairs and downtime, while also enhancing safety and performance. This article explores why preventative maintenance is key for heavy equipment and the many benefits it brings to construction operations.
Key Takeaways
- Preventative maintenance helps avoid costly repairs and unplanned downtime.
- Regular maintenance checks improve equipment safety and operator confidence.
- Routine inspections allow for quick fixes of minor issues before they escalate.
- Following maintenance schedules can significantly extend the lifespan of heavy equipment.
- A proactive maintenance approach enhances overall equipment performance and efficiency.
Understanding Preventative Maintenance for Heavy Equipment
Preventative maintenance is essential for keeping heavy equipment in top shape. It helps avoid costly breakdowns and ensures that machinery operates efficiently. This type of maintenance goes beyond just routine checks; it involves a comprehensive approach to care for equipment.
The Role of Manufacturers' Recommendations
Manufacturers provide guidelines that are crucial for maintaining equipment. Following these recommendations can help:
- Ensure safety and compliance
- Extend the lifespan of the machinery
- Optimize performance
Input from Operators and Mechanics
The people who operate and repair the equipment have valuable insights. Their input can lead to better maintenance practices by:
- Identifying common issues
- Suggesting improvements based on experience
- Enhancing communication between teams
Team Approach to Maintenance
A successful maintenance strategy involves collaboration among various team members. This includes:
- Operators who use the equipment daily
- Mechanics who understand the technical aspects
- Management to oversee the maintenance schedule
A well-rounded team approach to maintenance can significantly reduce unexpected failures and improve overall efficiency.
By understanding and implementing these aspects of preventative maintenance, companies can minimize breakdowns, extend equipment life, and keep their construction projects on time. This is your comprehensive guide to equipment maintenance.
Benefits of Routine and Preventative Maintenance
Routine and preventative maintenance is essential for keeping heavy equipment in top shape. A strong maintenance program will keep the assets in peak condition and help avoid costly repairs. Here are some key benefits:
Cost Savings Over Time
- Regular maintenance can save money in the long run by preventing major repairs.
- It reduces the chances of unexpected breakdowns that can lead to expensive downtime.
- Investing in routine checks is cheaper than dealing with emergency repairs.
Reducing Equipment Downtime
- Scheduled maintenance helps ensure that equipment is available when needed.
- By addressing minor issues early, you can prevent them from becoming major problems.
- This proactive approach minimizes the time equipment is out of service.
Enhancing Equipment Safety
- Well-maintained equipment is safer for operators and reduces the risk of accidents.
- Regular checks can identify potential hazards before they cause harm.
- A safer work environment boosts employee confidence and productivity.
Preventative maintenance not only extends the life of your equipment but also enhances its performance and safety. By making it a priority, companies can ensure their machinery operates efficiently and reliably.
Maximizing Equipment Lifespan Through Preventative Maintenance
Regular Inspections and Tune-ups
Regular inspections and tune-ups are essential for keeping heavy equipment in top shape. By checking the machinery frequently, you can catch small problems before they become big issues. Here are some key points to remember:
- Inspect equipment regularly to identify wear and tear.
- Schedule tune-ups based on the manufacturer's recommendations.
- Keep a checklist to ensure no part is overlooked.
Scheduling Maintenance in Advance
Planning maintenance ahead of time can save you from unexpected breakdowns. Here’s how to effectively schedule maintenance:
- Create a maintenance calendar for all equipment.
- Set reminders for upcoming inspections and tune-ups.
- Ensure that maintenance is done during off-peak hours to minimize downtime.
Avoiding Major Failures
Preventative maintenance helps in avoiding major failures that can lead to costly repairs. Here are some strategies to prevent these failures:
- Address minor issues quickly before they escalate.
- Keep a log of all maintenance activities to track performance.
- Train operators to recognize warning signs of potential problems.
Regular maintenance is key to extending your heavy equipment's lifespan. Preventive care, prompt repairs, and quality parts keep machinery running efficiently.
Improving Equipment Performance and Efficiency
Resolving Minor Issues Quickly
Regular maintenance helps in catching small problems before they turn into big ones. By addressing these issues early, you can:
- Prevent major breakdowns
- Save on repair costs
- Keep equipment running smoothly
Ensuring Maximum Capacity Operation
When equipment is well-maintained, it can operate at its best. This means:
- Higher productivity
- Better quality of work
- Less fuel consumption
Speeding Up Workflow
With efficient equipment, tasks can be completed faster. This leads to:
- Quicker project completion
- Improved team morale
- Enhanced customer satisfaction
Keeping your equipment in top shape not only boosts performance but also extends its lifespan. Regular checks and maintenance are essential for optimal operation.
Safety and Compliance in Heavy Equipment Maintenance
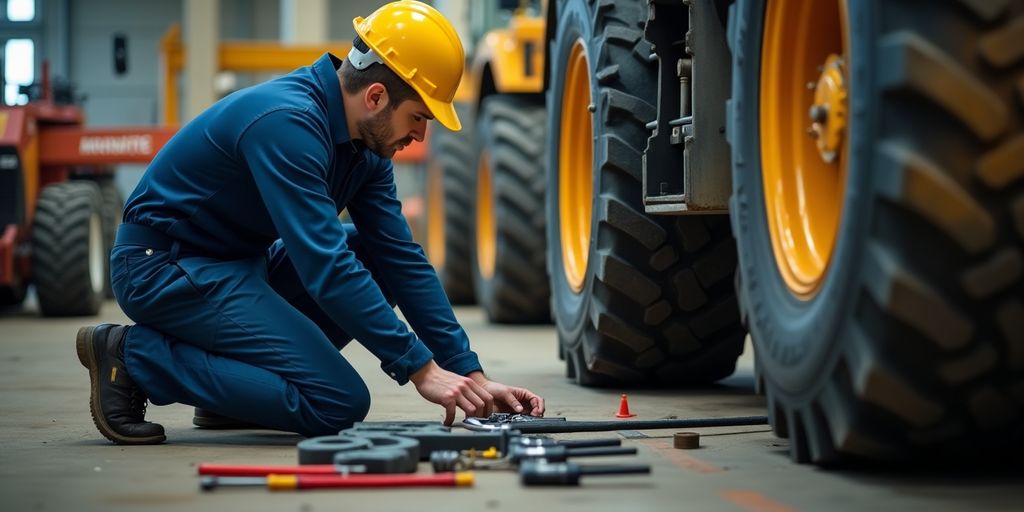
Adhering to OSHA Guidelines
Maintaining heavy equipment is not just about keeping machines running; it’s also about protecting your workers and ensuring compliance with safety regulations. Following OSHA guidelines helps prevent accidents and injuries on the job site. Regular maintenance checks can identify potential hazards before they become serious issues.
Identifying Potential Safety Hazards
Routine inspections are essential for spotting safety risks. Here are some common hazards to look for:
- Loose components that could fall off during operation.
- Fluid leaks that can create slippery surfaces.
- Faulty brakes that may fail when needed most.
Creating a Safer Work Environment
By prioritizing safety through preventative maintenance, you foster a culture of safety on the job site. This not only helps in avoiding accidents but also enhances your reputation as an OSHA-compliant employer. Regular maintenance can significantly reduce the risk of equipment failure, which is crucial for keeping your team safe and productive.
Regular maintenance is key to ensuring that your heavy equipment operates safely and efficiently, ultimately protecting both your workers and your investment.
Proactive vs. Reactive Maintenance Strategies
Understanding Proactive Maintenance
Proactive maintenance is all about preventing problems before they happen. This means taking steps to keep equipment running smoothly, rather than waiting for something to break down. For example, regular checks and servicing can help spot issues early. Here are some key points about proactive maintenance:
- Regular inspections help identify wear and tear.
- Scheduled maintenance keeps equipment in top shape.
- Training operators to notice small issues can prevent bigger problems.
Minimizing Unscheduled Repairs
By focusing on proactive strategies, companies can significantly reduce the number of unscheduled repairs. This leads to:
- Less downtime for equipment.
- Improved safety for operators.
- Better overall performance of machinery.
Proactive maintenance not only saves money but also helps keep equipment running efficiently and safely.
In conclusion, while reactive maintenance is necessary at times, a proactive approach is far more beneficial for maintaining heavy equipment. It ensures that problems are addressed before they escalate, leading to a more efficient and cost-effective operation.
Environmental and Economic Impact of Preventative Maintenance
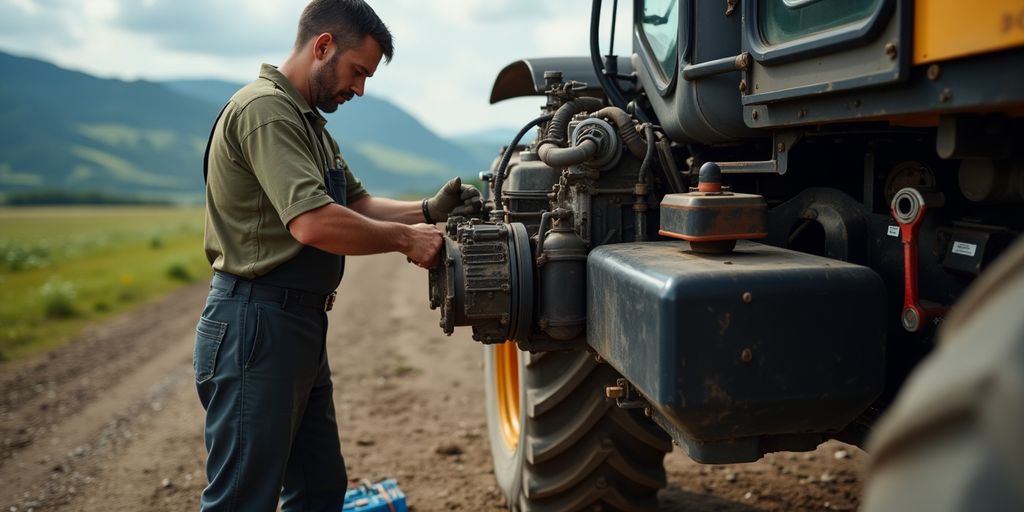
Reducing Fuel and Resource Waste
Preventative maintenance plays a crucial role in minimizing waste. By keeping equipment in top shape, companies can significantly reduce their consumption of fuel and other resources. This not only benefits the environment but also lowers operational costs. Regular checks and maintenance ensure that machines run efficiently, which leads to less energy use and fewer emissions.
Lowering Operating and Repair Costs
Investing in preventative maintenance can lead to substantial savings over time. Here are some key points to consider:
- Fewer emergency repairs: Regular maintenance helps catch issues early, preventing costly breakdowns.
- Extended equipment lifespan: Well-maintained machines last longer, reducing the need for replacements.
- Improved efficiency: Efficient machines consume less fuel and resources, leading to lower operating costs.
Enhancing Company Reputation
A commitment to preventative maintenance can enhance a company's reputation. Clients and partners appreciate businesses that prioritize sustainability and efficiency. This can lead to:
- Increased customer trust
- More business opportunities
- A positive public image
By adopting a proactive maintenance strategy, companies not only save money but also contribute to a healthier planet. In effect, maintenance closes the loop—ensuring resources keep circulating within the economy rather than being prematurely discarded.
Conclusion
In summary, regular preventive maintenance is essential for keeping heavy equipment running smoothly and efficiently. By sticking to a maintenance schedule, companies can save money, improve safety, and extend the life of their machines. This proactive approach helps catch small problems before they become big issues, which can lead to costly repairs and downtime. Moreover, well-maintained equipment is safer for workers and can perform better, leading to higher productivity. Investing in preventive maintenance not only protects your equipment but also ensures that your team can work confidently and effectively.
Frequently Asked Questions
What is preventative maintenance for heavy equipment?
Preventative maintenance is a planned approach to keep heavy equipment running smoothly. It involves regular checks and repairs to catch small problems before they become big issues.
Why is routine maintenance important?
Routine maintenance helps save money in the long run by preventing costly repairs and reducing equipment downtime. It ensures that machines work efficiently and safely.
How does preventative maintenance improve safety?
By regularly checking and maintaining equipment, you can identify and fix potential safety hazards, reducing the risk of accidents on the job site.
What are the benefits of regular inspections?
Regular inspections help spot minor issues early, ensuring that the equipment operates at its best and extends its lifespan.
How can preventative maintenance save money?
While it may seem like an extra cost, preventative maintenance can save you money by avoiding expensive repairs and minimizing downtime.
What should be included in a maintenance checklist?
A maintenance checklist should include tasks like oil changes, tire inspections, and regular tune-ups to keep equipment in top shape.