Top 5 Common Heavy Machinery Failures and How to Prevent Them
.png)
Heavy machinery is the backbone of many industries, but when it breaks down, it can bring everything to a halt. From construction to agriculture, these machines are vital for getting the job done. However, understanding why they fail and how to avoid those failures can save you time, money, and a lot of frustration. In this article, we'll break down the top 5 common heavy machinery failures and, more importantly, how to prevent them.
Key Takeaways
- Improper operation is a leading cause of machinery damage. Always ensure operators are trained and follow correct procedures.
- Skipping preventive maintenance can lead to costly repairs. Stick to a regular maintenance schedule to catch issues early.
- Extreme weather conditions can damage machinery. Protect equipment with proper storage and weatherproofing.
- Untrained operators can cause accidents and equipment failure. Invest in proper training and certifications.
- Mechanical failures are often preventable with routine inspections and timely part replacements.
1. Improper Operation
Operating heavy machinery is no joke. It’s not just about pressing buttons or pulling levers—it’s a skill that demands focus, precision, and understanding. When machines are used incorrectly, it can lead to serious issues, from minor inefficiencies to catastrophic breakdowns.
Common Mistakes in Operation
Here are a few ways improper operation can cause trouble:
- Ignoring the Operator’s Manual: Every machine comes with a manual, but let’s be real—how often do people actually read them? These guides are packed with essential information about calibration, troubleshooting, and safe operation. Skipping this step can cost you big time.
- Overloading the Machine: Pushing equipment beyond its limits might get the job done faster, but it’s a short-term gain with long-term consequences. Overloading can strain joints, damage parts, and lead to premature failure.
- Disregarding Warning Signals: Machines often have warning systems to alert operators when something’s off, like high engine temps or low hydraulic pressure. Ignoring these signals is like driving with the check engine light on—it’s only going to get worse.
Preventing Improper Operation
To avoid these pitfalls, follow these steps:
- Train Operators Thoroughly: Make sure every operator knows how to use the equipment correctly. Regular training updates don’t hurt either.
- Stick to the Manual: Keep the operator’s manual handy and refer to it whenever needed. It’s not just a book—it’s a lifesaver.
- Monitor and Address Warning Signs: Don’t ignore those blinking lights or unusual noises. They’re there for a reason.
Improper operation is one of the easiest issues to prevent if operators are given the right tools and training. Skimping on this can lead to downtime, costly repairs, and safety hazards.
For example, uneven weight distribution during transport, a common mistake, can lead to accidents and delays. Paying attention to these details can save you a lot of headaches later.
2. Failure to Perform Preventive Maintenance
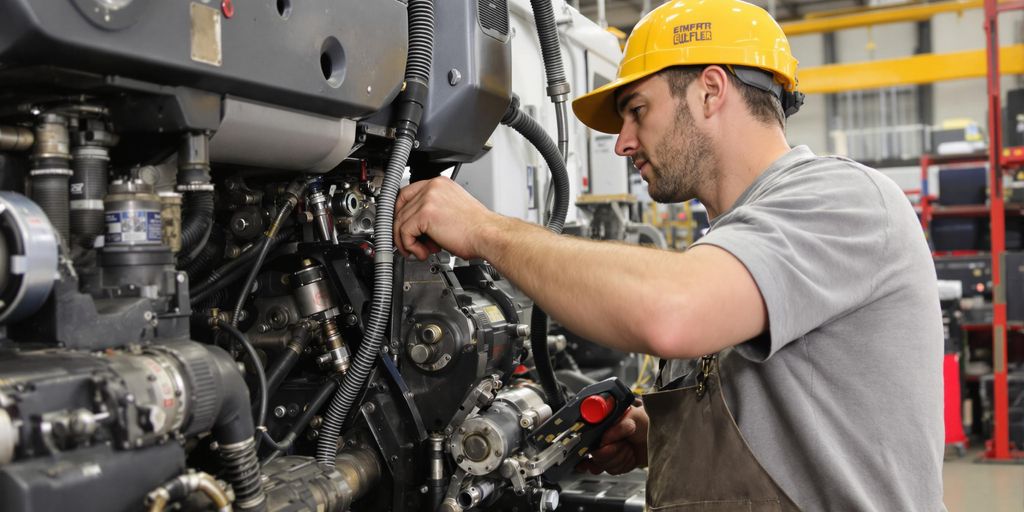
Skipping preventive maintenance is like ignoring a small leak in your roof—it might seem fine now, but it can lead to a disaster later. Heavy machinery needs consistent care to keep running smoothly. Unfortunately, maintenance often gets pushed aside when teams are short-staffed or overwhelmed with other tasks.
Why Preventive Maintenance Matters
- Prolongs Equipment Life: Regular servicing ensures machines last longer, saving money in the long run.
- Reduces Downtime: Catching issues early prevents unexpected breakdowns.
- Cuts Costs: Fixing small problems is cheaper than addressing major failures.
Common Issues When Maintenance Is Neglected
- Overlooking routine checks due to busy schedules.
- Lack of clear instructions for maintenance teams.
- Improper scheduling—servicing too often or not enough.
Quick Tips to Stay on Top of Maintenance
- Create a detailed maintenance schedule for each machine.
- Train your team to spot early signs of wear and tear.
- Use software to track servicing and avoid missed checkups.
Regular maintenance isn’t just about fixing what’s broken—it’s about preventing problems before they start. A little effort now can save a lot of headaches later.
For example, regular inspections can help identify leaks or hose failures early. Common maintenance issues like hydraulic fluid contamination are easier to handle when caught in time.
3. Weather-Related Issues
Heavy machinery and extreme weather don't mix well. Whether it's blistering heat, freezing cold, or heavy rain, each type of weather brings its own challenges to the table. Failing to prepare for these conditions can lead to costly downtime or even permanent damage.
Common Weather-Related Problems
- Cold Weather Challenges
- Heat and Overheating
- Rain and Humidity
Prevention Tips
- Perform regular maintenance checks tailored to the season. For instance, inspect cooling systems in summer and antifreeze levels in winter.
- Store machinery in covered or indoor areas when not in use, especially during extreme weather.
- Always clear snow and ice from walking and working surfaces like scaffolding and ladders to ensure safety.
Preparation is key. Weather is unpredictable, but taking small, consistent steps can save you from bigger headaches later on.
4. Untrained Operators
Heavy machinery is no joke—it’s powerful, complex, and needs to be handled with care. When someone who isn’t properly trained gets behind the controls, things can go south fast. Untrained operators are one of the biggest risks to both safety and equipment longevity.
Why It’s a Problem
The issue with untrained operators isn’t just about mistakes. It’s about the ripple effects those mistakes can cause. For instance:
- Misusing controls can lead to mechanical wear and tear.
- Skipping safety protocols might put everyone on-site in danger.
- Not recognizing warning signs could mean small issues turn into major repairs.
How to Prevent It
- Invest in Training: Make sure every operator gets proper hands-on training for every piece of machinery they’ll use. Don’t assume experience with one machine translates to another.
- Cross-Training: Whenever possible, train operators to handle multiple types of equipment. This way, you’re not stuck if someone’s out sick or on leave.
- Digital Monitoring Tools: Use smart tools to track operator performance and ensure compliance with safety standards. Effective management of equipment failure often starts with keeping untrained staff away from machinery.
"If you think training is expensive, try an accident." This saying hits home when it comes to heavy machinery. Spending time and money on training now can save you from costly repairs—or worse—down the line.
5. Mechanical Failures
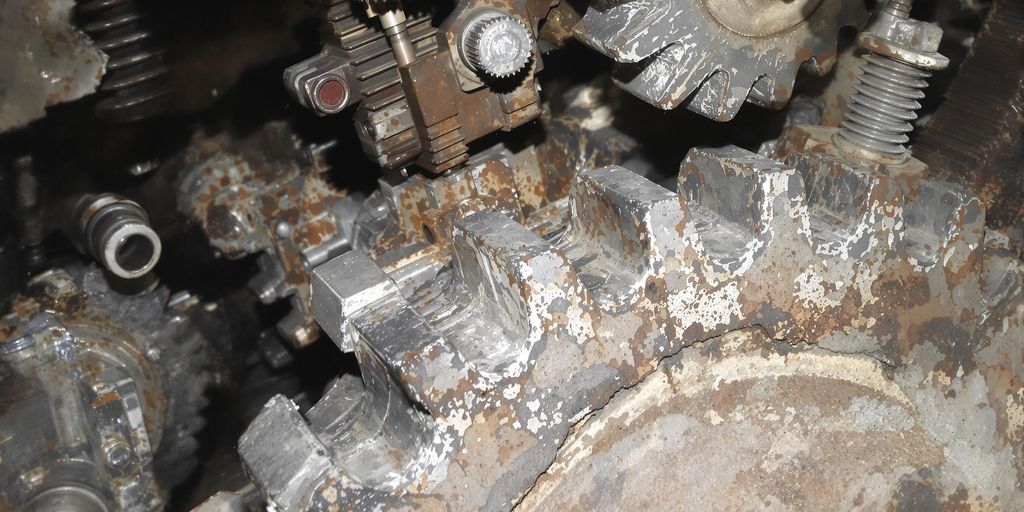
Mechanical failures in heavy machinery can be a real headache. These issues don’t just slow down operations—they can bring everything to a grinding halt. What’s worse, they’re often avoidable with the right approach.
Common Causes of Mechanical Failures
- Shock and Vibration: Machines are built to handle a lot, but constant shock or excessive vibrations can wear them down over time. Think of it like shaking a soda can every day—it’s bound to lose its fizz eventually.
- Overloading: Pushing equipment beyond its limits might get the job done faster, but it’s a shortcut to disaster. Components can bend, break, or just give out entirely.
- Collision: Accidental bumps or crashes can misalign parts, cause cracks, or even lead to total failure. It’s like dropping your phone—sometimes it’s fine, but other times, it’s toast.
Types of Mechanical Failures
- Sudden Failures: These happen out of nowhere. One minute the machine’s fine, and the next, it’s not. Often, these are linked to undetected issues like worn-out parts.
- Intermittent Failures: These are the worst for diagnosing. The machine stops, then starts working again like nothing happened. It’s frustrating and makes troubleshooting a guessing game.
- Gradual Failures: Over time, wear and tear take their toll. You might notice reduced performance before the machine finally gives out.
Preventing Mechanical Failures
Here’s the deal: most mechanical failures can be avoided with a solid plan. Here’s how:
- Schedule regular maintenance checks. Don’t wait for something to go wrong.
- Train operators to use machinery correctly—no shortcuts or risky maneuvers.
- Keep an eye on warning signs like unusual noises, leaks, or performance dips.
A well-maintained machine is like a well-fed athlete—it performs better, lasts longer, and is less likely to quit on you mid-task.
For example, hydraulic system failures often stem from issues like fluid contamination or pressure imbalances. Tackling these proactively can save you a lot of time and money in the long run.
Conclusion
Heavy machinery is a big investment, and keeping it running smoothly is no small task. From training operators properly to sticking to a solid maintenance schedule, there are plenty of ways to avoid costly breakdowns. Sure, things like weather or unexpected failures can still happen, but being proactive can save you a lot of headaches—and money—in the long run. At the end of the day, taking care of your equipment means taking care of your business. So, put in the effort now, and you’ll thank yourself later.
Frequently Asked Questions
What are the main reasons heavy machinery fails?
Heavy machinery can fail due to improper use, lack of regular maintenance, extreme weather conditions, untrained operators, and mechanical issues.
How can I avoid machinery breakdowns?
You can prevent breakdowns by following the manufacturer's maintenance schedule, training operators, and checking equipment regularly for wear and tear.
Why is operator training so important?
Trained operators know how to properly handle machinery, which reduces the risk of accidents and equipment damage.
What role does weather play in machinery failure?
Extreme weather, such as intense heat or heavy rain, can cause machinery to overheat, corrode, or malfunction.
How often should I perform maintenance on heavy equipment?
It depends on the type of machinery, but most equipment requires maintenance after a specific number of hours of use, as recommended by the manufacturer.
What should I do if my machinery breaks down unexpectedly?
Stop using the equipment immediately, inspect it for obvious issues, and contact a professional technician to diagnose and repair the problem.