The Importance of Regular Equipment Inspections for Compliance
.png)
Regular equipment inspections are not just a good practice; they're essential for maintaining safety and compliance in any workplace. Whether in construction, manufacturing, or any other industry, keeping a close eye on equipment can prevent accidents, ensure regulatory adherence, and ultimately save time and money. In this article, we’ll explore why regular inspections are critical and how they contribute to a safer and more efficient work environment.
Key Takeaways
- Regular equipment inspections help ensure compliance with safety regulations.
- They can prevent unexpected equipment failures, saving time and money.
- Documenting inspections demonstrates a commitment to safety and can protect against legal issues.
- Engaging your team in inspections fosters a culture of safety and responsibility.
- Using technology can streamline inspections and maintain thorough records.
Understanding Compliance Requirements
Overview of Regulatory Standards
Keeping up with all the rules and regulations can feel like a never-ending task. It's not just about knowing the rules, but also understanding why they exist. These standards are in place to protect workers, the environment, and the public. Think of it as a framework that helps everyone stay safe and responsible. Different industries have different sets of rules, so what applies to a construction site won't necessarily apply to a food processing plant. It's important to know which regulations apply to your specific situation.
Key Organizations Involved
There are several organizations that play a big role in setting and enforcing compliance standards. You've probably heard of some of them. These organizations create the guidelines and rules that companies need to follow. Here are a few:
- OSHA (Occupational Safety and Health Administration): Focuses on workplace safety.
- EPA (Environmental Protection Agency): Deals with environmental regulations.
- ANSI (American National Standards Institute): Develops voluntary consensus standards.
Understanding which organizations have authority over your industry is key. They often provide resources and guidance to help you stay compliant. It's a good idea to check their websites regularly for updates and changes.
Consequences of Non-Compliance
Ignoring compliance requirements can lead to some serious problems. It's not just about getting a slap on the wrist; the consequences can be quite severe. Here's what you might face:
- Fines and penalties: These can be hefty and can really hurt your bottom line. Regular safety compliance services can help avoid these.
- Legal action: In some cases, non-compliance can lead to lawsuits and other legal troubles.
- Damage to reputation: A company known for cutting corners on safety can lose customers and damage its brand.
- Project delays: Non-compliance can halt operations and delay project completion.
It's better to invest in compliance upfront than to deal with the fallout later. Documented inspection records can serve as proof of compliance during safety audits.
Benefits of Regular Equipment Inspections
Regular equipment inspections? Yeah, they might seem like a pain, another thing on the to-do list. But honestly, they're super important. It's not just about ticking boxes for compliance; it's about keeping things running smoothly and safely. Think of it as preventative medicine for your equipment.
Enhancing Workplace Safety
Okay, first and foremost, safety. Regular inspections directly contribute to a safer work environment. It's pretty simple: if you know your equipment is in good shape, you reduce the risk of accidents.
- Peace of mind for workers.
- Proactive safety culture.
- Reduced liability.
When equipment is regularly checked, everyone feels more secure. This creates a better atmosphere where people are more likely to report concerns and follow safety procedures.
Preventing Equipment Failures
Think of inspections as a way to catch problems early. Like, really early. It's way better to fix a small issue than deal with a major breakdown. Regular machine health checks can save you a ton of headaches.
- Catch problems before they snowball.
- Preventative maintenance becomes easier.
- Effective project execution.
Minimizing Downtime
Downtime is a killer. It messes with schedules, costs money, and just generally makes everyone stressed. Regular inspections help keep downtime to a minimum. By spotting potential problems early, you can schedule repairs when it's convenient, not when something breaks down unexpectedly. Plus, it helps with safety compliance.
- Less downtime.
- Prolonging equipment lifespan.
- Enhancing performance and efficiency.
Creating an Effective Inspection Checklist
Tailoring Checklists to Equipment Types
One size definitely doesn't fit all when it comes to equipment inspections. A bulldozer checklist will look very different from a forklift checklist. Always start with the manufacturer's recommendations. They know their equipment best. Consider breaking down your inspections into daily, weekly, and monthly checks. This way, you're not overwhelming anyone with a massive list every single day, but you're still catching potential problems early.
Essential Components to Include
What should always be on your checklist? Here's a start:
- Fluid levels (oil, coolant, hydraulic fluid)
- Tire condition and pressure
- Brake function
- Lights and signals
- Safety devices (alarms, guards)
It's a good idea to include a section for the inspector to sign off, confirming they've completed the check. This adds accountability and makes it clear who is responsible.
Frequency of Inspections
How often should you inspect? It depends. High-use equipment needs more frequent checks. Consider the operating environment too. Dusty, rough conditions mean more wear and tear. Don't just set a schedule and forget it. Review your inspection frequency regularly and adjust as needed. Here's a basic guideline:
- Daily: Visual checks before each shift.
- Weekly: More in-depth checks of critical systems.
- Monthly: Comprehensive inspections, including fluid changes and lubrication.
The Role of Documentation in Compliance
Importance of Keeping Records
Maintaining detailed records of equipment inspections is super important for compliance. It's not just about ticking boxes; it's about creating a history of your equipment's health. Think of it like this: if something goes wrong, those records are your best friend. They show you've been proactive and diligent. Plus, it helps spot trends. Is a certain part failing more often than it should? Records will tell you. This helps with equipment compliance and preventative maintenance.
How to Document Inspections
Okay, so you know why to document, but how? Here's the deal:
- Be thorough: Don't just write "Looks good." Note the date, time, inspector, and specific readings or observations. Use a checklist to make sure you cover everything.
- Be consistent: Use the same format every time. This makes it easier to compare inspections over time.
- Be organized: Keep records in a safe, accessible place. Digital systems are great, but paper works too, as long as it's organized.
Proper documentation isn't just about compliance; it's about creating a culture of accountability and continuous improvement. It allows you to track the effectiveness of your maintenance programs and make data-driven decisions about equipment management.
Using Records for Audits
Audits. The word alone can send shivers down your spine. But with good documentation, they don't have to be scary. Your inspection records are proof that you're taking compliance seriously. They show auditors that you're not just saying you're doing things right; you're proving it. Make sure your records are easy to understand and readily available. A well-organized system can save you time, money, and a whole lot of stress during an audit. Think of it as your insurance policy against fines and penalties.
Training and Engaging Your Team
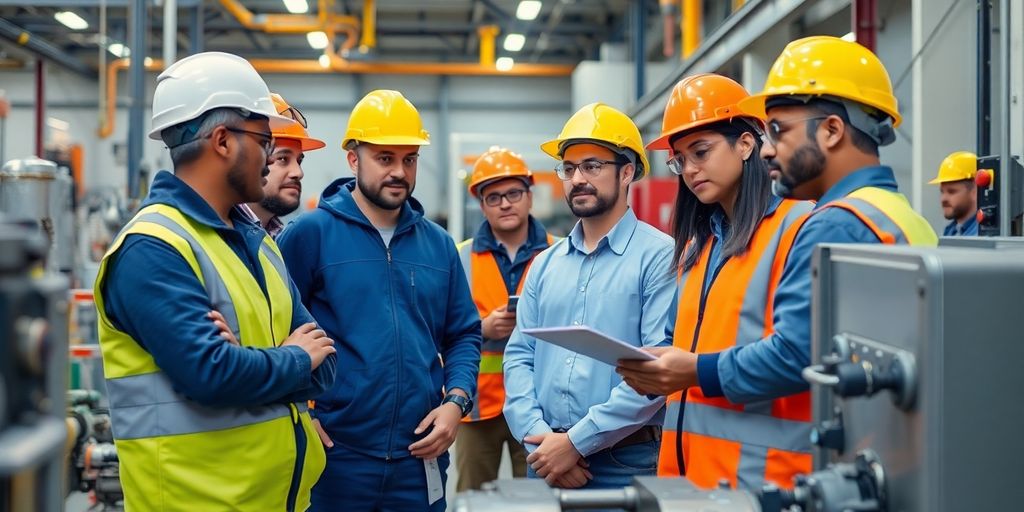
It's easy to think that compliance is just about ticking boxes, but it's way more than that. It's about getting everyone on board and making safety a real priority. If your team isn't properly trained and engaged, all the checklists in the world won't make a difference.
Fostering a Safety Culture
Creating a safety culture isn't something that happens overnight. It starts from the top, with leadership demonstrating a commitment to safety in everything they do. It's about making safety a core value, not just a set of rules. This means open communication, where employees feel comfortable reporting hazards or near misses without fear of reprisal. Regular meetings to discuss safety concerns, celebrate successes, and learn from incidents can also help build a strong safety culture.
Training Programs for Inspectors
Proper training is non-negotiable. You can't expect people to perform effective inspections if they don't know what to look for or how to document it. Training programs should cover:
- Equipment-specific knowledge: Understanding how each piece of equipment works and its potential hazards.
- Inspection procedures: Step-by-step instructions on how to conduct thorough inspections.
- Documentation requirements: Knowing how to accurately record findings and report issues.
- Regulatory updates: Staying current with changes in compliance standards.
Investing in comprehensive training shows your team that you value their safety and their ability to do their jobs effectively. It also reduces the risk of errors and oversights that could lead to accidents or compliance violations.
Encouraging Team Participation
Compliance shouldn't be a top-down mandate; it should be a team effort. Encourage employees to take ownership of safety by:
- Involving them in the development of inspection checklists.
- Soliciting their feedback on safety procedures.
- Recognizing and rewarding employees who go above and beyond to promote safety.
By making compliance a collaborative process, you can create a more engaged and safety-conscious workforce. Consider personalized programs to improve compliance training effectiveness.
Common Pitfalls to Avoid
Neglecting Routine Inspections
It's easy to let equipment inspections slide, especially when deadlines loom and projects pile up. However, skipping these inspections can lead to serious problems down the road. Regular inspections are the cornerstone of a safe and compliant operation. Without them, you're essentially gambling with the safety of your team and the reliability of your equipment. Think of it like ignoring that weird noise your car is making – it might go away on its own, but it's more likely to turn into a much bigger, more expensive issue.
Inadequate Training
Having a checklist is one thing, but having a team that knows how to use it properly is another. If your inspectors aren't adequately trained, they might miss critical issues or perform inspections incorrectly. This can create a false sense of security, leading to accidents and compliance violations. Make sure your team understands the equipment, the inspection procedures, and what to look for. equipment service is essential for maintaining operational efficiency.
Ignoring Regulatory Changes
Compliance isn't a static thing; regulations change, and it's your responsibility to stay up-to-date. Ignoring these changes can lead to fines, penalties, and even legal action. Make sure you're subscribed to industry updates, attending relevant training sessions, and regularly reviewing your inspection procedures to ensure they align with the latest requirements.
Failing to keep up with regulatory changes is like driving with an outdated map – you might think you know where you're going, but you could end up in the wrong place, facing unexpected obstacles.
Leveraging Technology for Inspections
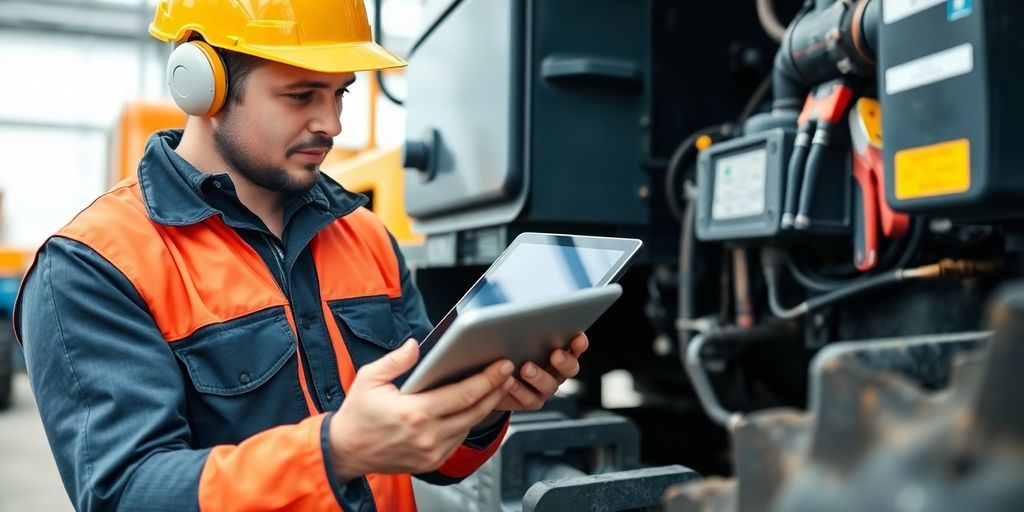
Technology is changing how we approach equipment inspections. It's not just about clipboards and checklists anymore. We can now use digital tools to make the process faster, more accurate, and way more efficient. Let's look at how technology can help.
Using Digital Tools for Efficiency
Digital tools are a game-changer. Think about it: no more paper checklists that get lost or damaged. Everything is stored in the cloud, accessible from anywhere. You can use tablets or smartphones to conduct inspections, adding photos, videos, and notes directly to the report. This makes it easier to share information with your team and track progress. Plus, digital tools often come with built-in reporting features, so you can quickly generate reports and identify trends. Using a no-code computer vision platform can also help automate defect detection.
Benefits of Automated Reminders
How many times have you forgotten to schedule an inspection? It happens. But with automated reminders, you can set up notifications to remind you when inspections are due. This helps ensure that inspections are completed on time, every time.
Here's why automated reminders are great:
- They reduce the risk of missed inspections.
- They help you stay on schedule.
- They improve compliance.
Tracking Inspection History
Having a detailed inspection history is super important. It allows you to see how your equipment has been performing over time, identify potential problems, and make informed decisions about maintenance and repairs. With digital tools, you can easily track inspection history and generate reports. This information can be used to ensure safety compliance and extend the lifespan of your equipment.
Keeping a detailed record of inspections is essential for identifying patterns and trends that might indicate potential problems. This information allows you to schedule preventative maintenance before issues become severe, ultimately saving time and money.
Wrapping It Up
In summary, keeping up with regular equipment inspections is not just a good idea; it's a necessity. These checks help catch problems before they turn into big headaches, keeping your team safe and your projects on track. Plus, staying compliant with safety regulations can save you from costly fines and legal troubles down the line. So, make inspections a routine part of your operations. It’s a simple step that pays off in safety, efficiency, and peace of mind.
Frequently Asked Questions
Why are regular equipment inspections important?
Regular equipment inspections are essential to ensure safety and compliance with regulations. They help identify problems before they lead to accidents or equipment failures.
What should be included in an equipment inspection checklist?
An equipment inspection checklist should include key areas like fluid levels, safety features, and operational parts. Tailoring it to specific equipment types is also important.
How often should equipment inspections be conducted?
The frequency of inspections can vary based on the type of equipment, but routine checks should be done daily, weekly, or monthly to catch issues early.
What are the consequences of not inspecting equipment?
Neglecting inspections can lead to serious accidents, costly repairs, and legal penalties due to non-compliance with safety regulations.
How can documentation help with compliance?
Keeping detailed records of inspections shows that you follow safety rules. This documentation can be crucial during audits and helps demonstrate your commitment to safety.
What role does team training play in equipment inspections?
Training your team on how to conduct inspections fosters a culture of safety and responsibility, encouraging everyone to participate in maintaining e