The Impact of GPS and Telematics on Heavy Equipment Management
.png)
In today's construction landscape, the integration of GPS and telematics technology has transformed how heavy equipment is managed. These advancements allow for real-time tracking, enhanced maintenance, and improved safety on job sites. This article explores the impact of GPS and telematics on heavy equipment management, highlighting the benefits and challenges that come with this technology.
Key Takeaways
- Telematics systems provide real-time data for better equipment allocation and usage.
- Predictive maintenance can prevent costly downtime by monitoring equipment health remotely.
- GPS tracking enhances safety by allowing for real-time location monitoring and geofencing.
- Telematics helps reduce operational costs by optimizing fuel consumption and minimizing idle time.
- The future of heavy equipment management will see more automation and integration with other technologies.
Understanding Telematics Technology
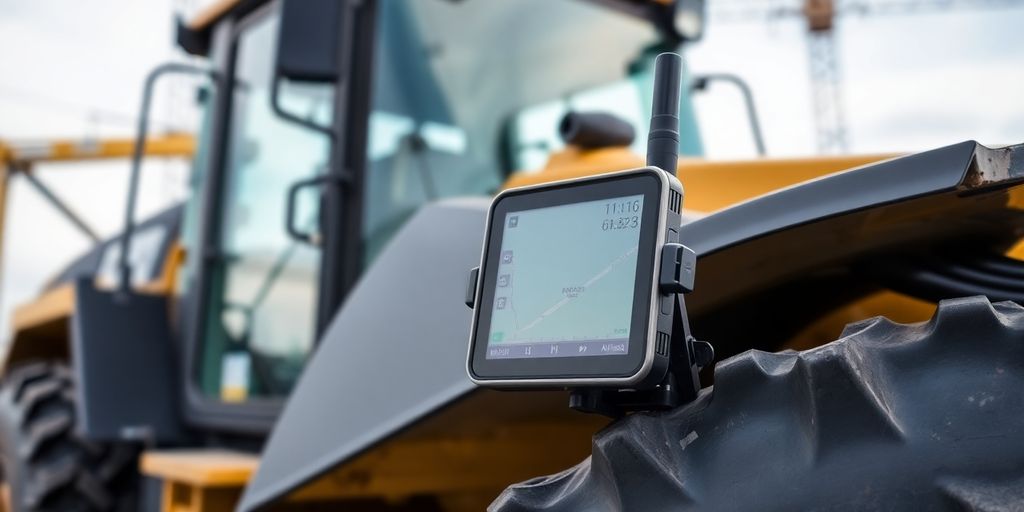
Telematics is changing how we manage heavy equipment. It's not just about knowing where your stuff is; it's about getting actionable data to make smarter decisions. Let's break down what makes up this technology.
Components of a Telematics System
A telematics system is more than just a GPS tracker. It's a combination of hardware and software working together. Here's a quick rundown:
- GPS receivers: These pinpoint the location of your equipment.
- Sensors: These monitor everything from engine performance to fuel levels.
- Data analytics: This turns raw data into useful insights.
- Connectivity: This allows data to be transmitted wirelessly.
The Role of GPS in Telematics
GPS is the foundation of telematics. It provides real-time location data, which is essential for tracking equipment, preventing theft, and optimizing routes. Think of it as the eyes and ears of your operation. Construction telematics uses GPS to monitor equipment location.
Data Analytics in Heavy Equipment Management
Telematics systems generate a ton of data. But raw data alone isn't helpful. That's where data analytics comes in. It processes the information collected by sensors and GPS, turning it into insights you can use to improve efficiency, reduce costs, and boost safety.
Data analytics helps you understand how your equipment is being used, identify potential problems, and make informed decisions about maintenance and operations. It's like having a virtual mechanic and operations manager all rolled into one.
Enhancing Equipment Utilization
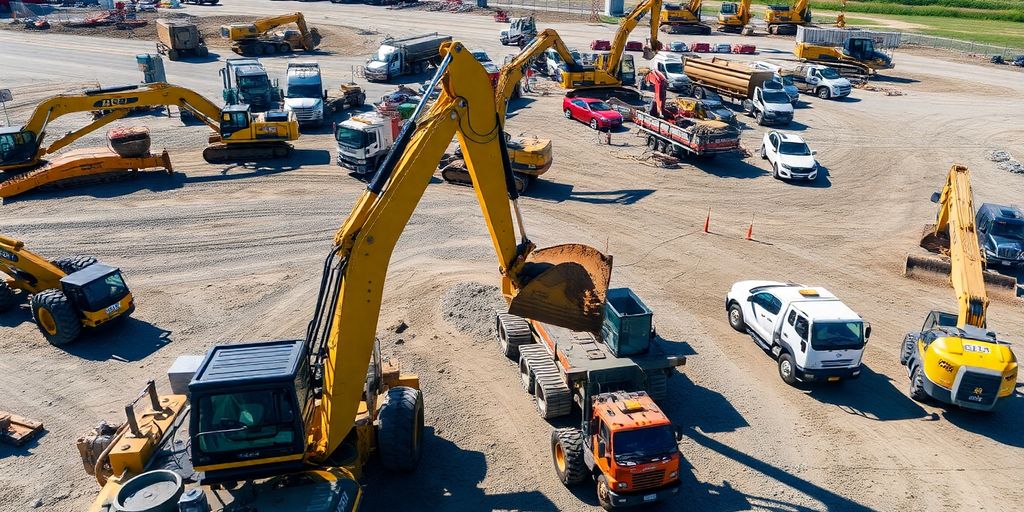
Improved Equipment Allocation Strategies
Okay, so think about it: how often do you see equipment sitting around, not doing anything? Or maybe you've got two machines doing the job of one, or one machine struggling to do the job of two. It's a common problem, and it costs money. Telematics can help with equipment runtime analysis. By tracking how often equipment is used, where it's used, and for how long, you can make smarter decisions about where to send it. This means fewer instances of equipment being underutilized or overused.
Monitoring Idle Time and Usage
Idle time is a silent killer of efficiency. You're burning fuel, racking up hours on the engine, and not getting any work done. Telematics systems can monitor idle time in real-time, giving you the data you need to address the problem. Maybe you need to adjust work schedules, retrain operators, or simply shut down equipment when it's not needed. The data doesn't lie.
Maximizing Asset Efficiency
Asset efficiency is the name of the game. It's about getting the most out of every piece of equipment you own. Telematics provides the insights needed to optimize equipment usage, reduce downtime, and extend the lifespan of your assets. This isn't just about saving money in the short term; it's about building a more sustainable and profitable business for the long haul.
Telematics helps you understand exactly how your equipment is being used, allowing you to make data-driven decisions that improve efficiency and reduce waste. It's about working smarter, not harder, and getting the most out of your investment.
Proactive Maintenance Strategies
Predictive Maintenance Benefits
Okay, so predictive maintenance is a big deal. Instead of just changing the oil every X number of hours, you're actually looking at the data to see when something needs to be changed. It's like going to the doctor for a checkup instead of waiting until you're really sick. This approach helps avoid unexpected breakdowns, which can save a ton of money and time.
- Reduced downtime
- Extended equipment lifespan
- Lower repair costs
Predictive maintenance uses data to forecast when equipment might fail. This allows for scheduled maintenance during off-peak times, minimizing disruptions and maximizing operational efficiency.
Remote Monitoring of Equipment Health
With telematics, you can keep an eye on your equipment from anywhere. This means you don't have to physically check every machine every day. Sensors on the equipment send data back to a central system, so you can see things like engine temperature, oil pressure, and fuel consumption in real-time. If something looks off, you can address it before it becomes a major problem. This is especially useful for equipment that's located in remote areas or on multiple job sites. Telematics offers maintenance automation tools that help reduce unexpected equipment failures.
Scheduling Maintenance for Optimal Performance
Telematics data helps you schedule maintenance at the best possible time. Instead of following a rigid schedule based on hours, you can tailor the schedule to the actual usage and condition of the equipment. This means you're not wasting time and money on unnecessary maintenance, and you're also ensuring that your equipment is always running at its best.
Consider this:
Boosting Safety on Job Sites
Telematics isn't just about tracking equipment; it's also a game-changer for safety. By providing real-time data and monitoring capabilities, telematics systems help create safer work environments, reducing the risk of accidents and injuries. It's about making sure everyone goes home safe at the end of the day.
Real-Time Location Tracking
Knowing where your equipment is at all times is more than just theft prevention. It's about safety. Real-time location tracking allows supervisors to quickly locate equipment in case of an emergency, ensuring help can arrive promptly. Plus, it helps prevent collisions by giving operators a clear picture of nearby equipment and personnel. This is especially useful in crowded or complex job sites. You can use equipment technologies to improve safety.
Geofencing for Equipment Security
Geofencing creates virtual boundaries around job sites or specific areas within them. If a piece of equipment enters or exits a geofenced area without authorization, an alert is triggered. This helps prevent theft, but it also keeps equipment out of dangerous zones. For example, you can set up geofences around environmentally sensitive areas or unstable ground, preventing operators from accidentally entering those areas. It's like a digital safety net.
Imagine a scenario where a new operator accidentally drives a bulldozer too close to a protected wetland. With geofencing, an alert would immediately notify the supervisor, allowing them to intervene before any damage occurs. This proactive approach is key to preventing accidents and protecting the environment.
Reducing Worksite Accidents
Telematics systems can monitor a range of equipment parameters that contribute to accidents, such as speed, sudden stops, and excessive idling. By analyzing this data, managers can identify risky behaviors and provide targeted training to operators. This helps reduce the likelihood of accidents caused by human error.
Here's a quick look at how telematics can help reduce accidents:
- Monitoring speed and location to prevent collisions.
- Tracking equipment usage to identify potential maintenance issues.
- Providing alerts for unauthorized equipment use.
- Analyzing operator behavior to identify training needs.
The Future of Heavy Equipment Management
The heavy equipment industry is on the cusp of some pretty big changes, driven by tech. We're not just talking about incremental improvements; we're looking at shifts in how equipment is managed, operated, and even owned. It's a pretty exciting time, honestly.
Trends in Telematics Adoption
Telematics is becoming less of a 'nice-to-have' and more of a 'must-have'. More companies are realizing the value of real-time data for decision-making. It's not just about tracking location anymore; it's about understanding equipment health, usage patterns, and overall efficiency. This increased adoption is also pushing telematics providers to innovate and offer more sophisticated solutions. For example, equipment scheduling is becoming more efficient.
- Increased data integration across different equipment types.
- More user-friendly interfaces for easier data interpretation.
- Greater emphasis on cybersecurity to protect sensitive data.
Impact of Autonomous Equipment
Autonomous equipment is no longer a sci-fi fantasy; it's slowly becoming a reality on some job sites. While fully autonomous operation is still a ways off for many applications, we're seeing more semi-autonomous features being implemented. This includes things like automated grading, obstacle avoidance, and remote operation. The impact on productivity and safety could be huge, but there are also questions about job displacement and the need for new skill sets.
The integration of autonomous features will require a shift in how we train and manage equipment operators. It's not about replacing humans entirely, but about augmenting their capabilities and allowing them to focus on more complex tasks.
Integration with Other Technologies
Telematics isn't operating in a vacuum. It's becoming increasingly integrated with other technologies like IoT sensors, AI-powered analytics, and even blockchain. This integration is creating a more holistic view of equipment management and enabling new possibilities. For example, IoT sensors can provide more granular data on equipment performance, while AI can help predict maintenance needs and optimize operations. It's all about connecting the dots and creating a smarter, more efficient ecosystem.
- Integration with building information modeling (BIM) for better project planning.
- Use of augmented reality (AR) for remote diagnostics and repair.
- Development of digital twins for virtual equipment management.
Challenges in Implementing Telematics
While the advantages of telematics in heavy equipment management are clear, getting started isn't always easy. Several hurdles can slow down or even stop the adoption process. It's important to know these challenges upfront to plan for them.
Barriers to Adoption
One of the biggest issues is the initial cost. Setting up a telematics system can be expensive, especially for smaller companies. There's the cost of the hardware (the GPS trackers and sensors), plus the software and the ongoing subscription fees. Convincing decision-makers to invest can be tough, especially if they don't fully understand the long-term benefits. Another barrier is resistance to change. Some operators and managers might be used to doing things a certain way and may not want to learn a new system. It's important to show them how telematics can make their jobs easier, not harder. Finally, a lack of reliable internet connectivity on remote job sites can also be a problem. Without a good connection, the data can't be transmitted in real-time, which defeats the purpose of using telematics systems.
Data Management Issues
Telematics systems generate a lot of data. Knowing what to do with all that information can be overwhelming. It's not enough to just collect the data; you need to be able to analyze it and turn it into actionable insights. This requires having the right tools and expertise. Many companies struggle with this aspect of telematics. They might not have the staff or the skills to effectively manage and interpret the data. This can lead to data overload, where they're collecting tons of information but not actually using it to improve their operations. Also, data security is a concern. You need to make sure the data is protected from unauthorized access and cyber threats.
Training and Education Needs
To get the most out of a telematics system, everyone needs to be properly trained. This includes operators, managers, and maintenance personnel. They need to understand how the system works, how to use the software, and how to interpret the data. Without proper training, people won't be able to use the system effectively, and the company won't see the full benefits. Training should be ongoing, not just a one-time thing. As the technology evolves and new features are added, people need to be kept up-to-date. Also, it's important to educate key stakeholders about the value of telematics. They need to understand how it can improve efficiency, reduce costs, and boost profits. This will help them support the adoption and implementation of the system.
Implementing telematics is not just about installing hardware and software. It's about changing the way you do business. It requires a commitment to training, education, and data-driven decision-making.
Wrapping It Up
In the end, GPS and telematics are game changers for managing heavy equipment. They give managers a clear view of where their machines are and how they're being used. This means less downtime and better maintenance schedules. Plus, with real-time data, you can spot issues before they become big problems. It's not just about keeping track of equipment; it's about making smarter decisions that save time and money. As more companies start using this tech, we can expect to see even more improvements in efficiency and safety on job sites. So, if you're in the construction business and haven't jumped on the telematics bandwagon yet, now's the time to consider it.
Frequently Asked Questions
What is telematics in construction equipment?
Telematics in construction equipment is a technology that helps track and monitor machines. It allows you to see important information like fuel levels, maintenance needs, and how often the equipment is used.
How can telematics improve equipment usage?
Telematics helps managers see if equipment is being used properly. They can find out if machines are sitting idle too long or if they need more machines on a job site, which helps use resources better.
What are the benefits of predictive maintenance?
Predictive maintenance uses data to figure out when a machine might need repairs. This means you can fix things before they break, which saves time and money.
How does telematics enhance safety on job sites?
Telematics improves safety by allowing real-time tracking of equipment. It can also set up boundaries to keep machines in safe areas, reducing accidents.
Can telematics help reduce costs?
Yes, telematics can lower costs by monitoring fuel use and reducing downtime. It helps ensure machines are running efficiently and not wasting resources.
What challenges do companies face when using telematics?
Some challenges include getting everyone trained to use the technology, managing all the data collected, and overcoming any resistance to change from workers.