The Impact of 3D Printing on Heavy Machinery Manufacturing
.png)
3D printing is shaking things up in heavy machinery manufacturing. This tech isn't just a passing trend; it's changing how companies design, produce, and manage parts. From speeding up prototyping to cutting costs, the impact of 3D printing on heavy machinery manufacturing is significant. Let's explore how this technology is reshaping the industry.
Key Takeaways
- 3D printing allows for innovative designs that traditional methods can't achieve.
- Production efficiency is greatly improved with reduced lead times and less waste.
- Companies save money on tooling and materials by using 3D printing.
- On-demand production helps companies avoid supply chain issues.
- Advanced materials used in 3D printing offer better durability and sustainability.
Transforming Design Processes in Heavy Machinery
3D printing is really shaking things up in how heavy machinery is designed. It's not just about making things faster; it's about making things better and in ways that weren't possible before. Think about it: engineers aren't stuck with the same old manufacturing limitations anymore. They can actually design parts based on what works best, not just what's easiest to make with traditional methods. It's a total game changer.
Innovative Design Capabilities
With 3D printing, engineers can create complex geometries and intricate designs that were previously impossible or too expensive to produce using traditional manufacturing techniques. This opens the door to lighter, stronger, and more efficient parts. It's like giving designers a whole new set of tools to play with. Caterpillar is a great example; they're letting their engineers design without the old boundaries, which is leading to some pretty exciting innovations.
Rapid Prototyping
Remember when prototyping took forever? Not anymore. 3D printing allows for rapid prototyping, meaning engineers can quickly create physical models of their designs, test them, and make changes on the fly. This iterative process significantly reduces development time and costs. It's way easier to catch problems early when you can actually hold a prototype in your hand. No more waiting weeks for a prototype – you can have one in hours.
Customization for Specific Needs
One of the coolest things about 3D printing is the ability to customize parts for specific applications. Need a part that's slightly different for a particular machine or environment? No problem. 3D printing makes it easy to create bespoke solutions that meet unique requirements. This is especially useful in heavy machinery, where equipment often operates in diverse and demanding conditions.
3D printing is changing the way companies approach design. It's not just about making things faster; it's about making them smarter and more tailored to specific needs. This shift is leading to more efficient, durable, and cost-effective heavy machinery.
Enhancing Production Efficiency
Reduced Lead Times
3D printing really speeds things up. Instead of waiting weeks or months for parts, companies can produce them in days, or even hours. This is a game-changer for keeping production lines moving and meeting deadlines. Lead time reduction is a major benefit.
Minimized Waste
Traditional manufacturing often involves cutting away material to create a part, which leads to a lot of waste. 3D printing, on the other hand, only uses the material needed for the part. This means less waste and lower material costs. Plus, some of the unused material can be collected and reused, making the process even more efficient. 3D printing helps reduce waste.
Streamlined Manufacturing Processes
3D printing can simplify the whole manufacturing process. It allows for the creation of complex parts in a single step, reducing the need for multiple machines and assembly processes. This not only saves time but also reduces the risk of errors and improves overall efficiency.
3D printing is not just about making parts faster; it's about rethinking the entire manufacturing process. It allows for more flexible and agile production, which can be a huge advantage in today's fast-paced market.
Cost Savings Through 3D Printing
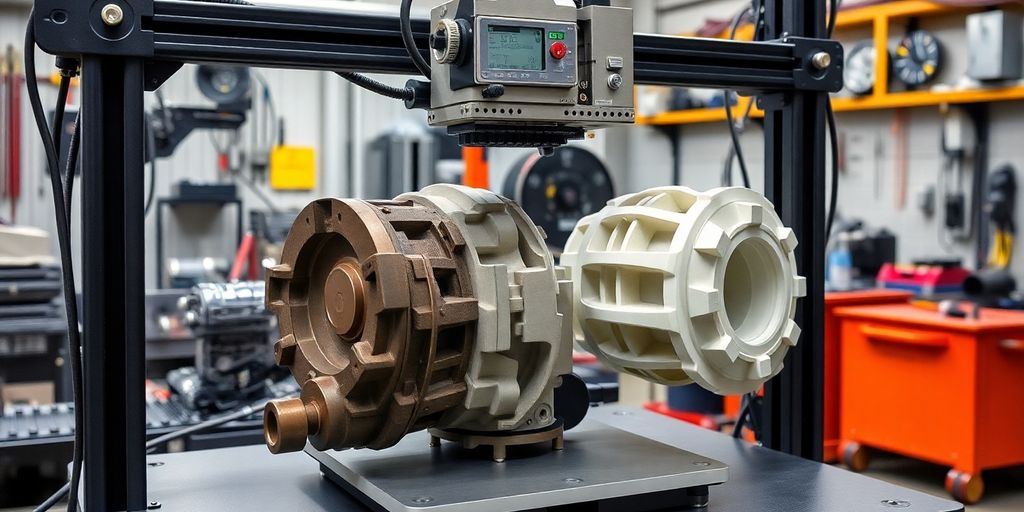
3D printing isn't just some futuristic tech; it's actually changing how companies manage their money, especially in heavy machinery. It's not just about making cool shapes; it's about cutting costs in ways that were impossible before. Let's get into the specifics.
Lower Tooling Costs
Traditional tooling can be a huge expense. Think about it: molds, dies, and specialized equipment all cost a lot to design, make, and store. 3D printing offers a way around this by creating tools and parts directly from digital designs. This means no more waiting weeks for a tool to be made, and no more paying for expensive custom molds. Neenah Foundry, for example, saved over $5,000 by 3D printing cores, and cut weeks off lead times. That's a big deal for any company.
Reduced Material Expenses
One of the coolest things about 3D printing is how little waste it produces. With traditional manufacturing, you often have to cut away material to get the shape you want, which leads to a lot of scrap. 3D printing, on the other hand, only uses the material it needs. This is especially important when working with expensive metals or specialized materials. Plus, some 3D printing processes even allow you to reuse unused material, further reducing waste and saving money. Sand 3D printers, for example, allow for the collection and reuse of unused sand powder.
Efficient Spare Parts Management
Keeping a stock of spare parts can be a logistical nightmare, especially for older machines. You have to predict what parts will break, store them somewhere, and hope you don't run out. 3D printing lets you make parts on demand, which means you only produce what you need, when you need it. This can save a ton of money on storage costs and prevent downtime caused by waiting for a part to be shipped. Caterpillar was able to print a two-piece plastic tool overnight to get a transmission assembly line up and running again after it had shut down due to a faulty component. That's the kind of responsiveness that can save a company serious cash.
3D printing is changing the game for spare parts. Instead of ordering a minimum quantity of 1000 parts, when you only need 5, you can print exactly what you need. This reduces waste, storage costs, and the risk of obsolescence. It's a more sustainable and cost-effective approach to managing spare parts inventories.
Improving Supply Chain Dynamics
3D printing is really shaking things up when it comes to how heavy machinery manufacturers handle their supply chains. It's not just about making parts anymore; it's about fundamentally changing how things get from the design table to the customer.
On-Demand Production
Imagine needing a specific part, but instead of waiting weeks or months for it to be manufactured and shipped, you can just print it yourself, right then and there. That's the promise of on-demand production. This capability drastically reduces lead times and minimizes downtime, which is a huge deal in the heavy machinery world where every minute of downtime can cost a fortune. It also means companies can keep their inventory lean, reducing storage costs and the risk of obsolescence. Think of it like this: instead of stocking a warehouse full of parts that might or might not be needed, you're stocking digital blueprints ready to be printed whenever the need arises. This is especially useful for older machines where parts are no longer in regular production. For example, military and defense sectors are using 3D printing to lower supply chain costs.
Localized Manufacturing
One of the coolest things about 3D printing is that it enables localized manufacturing. Instead of relying on a centralized factory, companies can set up smaller printing facilities closer to their customers or job sites. This has several advantages:
- Reduced shipping costs and transit times
- Greater responsiveness to local market needs
- Increased resilience to supply chain disruptions
It also opens up opportunities for creating jobs in areas that might not have traditionally been manufacturing hubs. Plus, it allows for quicker design iterations based on real-world feedback. It's like having a mini-factory right where you need it, capable of producing customized parts on the spot.
Mitigating Supply Chain Disruptions
We've all seen how fragile global supply chains can be, especially in recent years. 3D printing offers a way to build more resilient supply chains by reducing reliance on single suppliers or distant factories. By having the ability to produce parts in-house or through a network of local providers, companies can weather disruptions caused by natural disasters, political instability, or other unforeseen events. This agility is a major advantage in an increasingly uncertain world.
3D printing isn't just about making things faster or cheaper; it's about fundamentally changing the way we think about supply chains. It's about creating more flexible, responsive, and resilient systems that can adapt to whatever challenges the future may bring.
Advancements in Material Technology
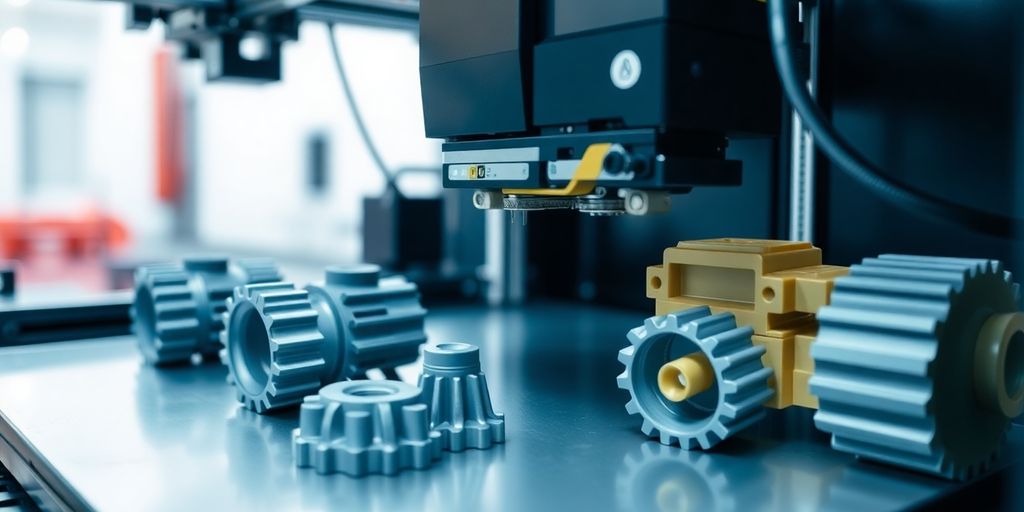
3D printing's impact on heavy machinery isn't just about new shapes; it's also about materials. We're seeing some cool stuff happen here, pushing the boundaries of what's possible.
Diverse Material Options
It's not just plastic anymore. We're talking metals, ceramics, composites – a whole range of materials that can now be used in 3D printing for heavy machinery. This opens up possibilities for parts with specific properties, like high strength or heat resistance. For example, you can now print parts using:
- Stainless steel alloys
- Titanium
- Nickel-based superalloys
- Various polymers with enhanced properties
Durability and Performance
The big question is, can these 3D-printed parts hold up in tough conditions? The answer is increasingly yes. Material science is advancing, and we're seeing 3D-printed parts that can withstand the stresses and strains of heavy machinery applications. Think about it: lighter parts that are just as strong, or even stronger, than traditionally manufactured ones.
Sustainability Considerations
3D printing can also be a more sustainable way to manufacture parts. It reduces waste by only using the material needed, and it can enable the use of recycled materials. Plus, localized production cuts down on transportation emissions. It's not a perfect solution, but it's a step in the right direction.
3D printing is changing how we think about materials in manufacturing. It's not just about making things faster; it's about making them better, stronger, and more sustainable. As material technology continues to evolve, we can expect even more exciting developments in the world of heavy machinery.
Case Studies of Successful Implementation
Caterpillar's Additive Manufacturing Factory
Caterpillar has seriously embraced 3D printing, and it's not just for show. They've built an entire additive manufacturing factory, and it's changing how they do things. This factory focuses on producing parts for their heavy machinery, and the results are pretty impressive.
- They're making parts faster.
- They're cutting down on waste.
- They're even able to create designs that weren't possible before.
Caterpillar's move shows that 3D printing isn't just a gimmick; it's a real solution for improving manufacturing processes and staying competitive.
Neenah Foundry's Cost Savings
Neenah Foundry, known for its metal castings, has found some serious cost savings by using 3D printing. Instead of relying solely on traditional methods, they're using 3D printing to create molds and patterns. This has a direct impact on their bottom line. The use of 3D printed designs has allowed them to optimize their production process.
- Reduced tooling costs.
- Faster turnaround times.
- Ability to handle complex geometries.
Real-World Applications in Heavy Equipment
3D printing is popping up in all sorts of heavy equipment applications. Think about it: custom parts, on-demand replacements, and even entirely new designs. It's not just about making things cheaper; it's about making them better.
- Creating lightweight components to improve fuel efficiency.
- Producing customized tools for specific tasks.
- Manufacturing replacement parts quickly to minimize downtime.
Future Trends in Heavy Machinery Manufacturing
It's interesting to think about where 3D printing is headed in the heavy machinery world. We're already seeing some cool stuff, but the future looks even more promising. It's not just about making parts anymore; it's about changing how we design, build, and maintain these massive machines. The industry is on the cusp of some pretty big changes, and those who adapt quickly will definitely have an advantage. By 2030, the 3D printing industry is projected to exceed a valuation of $40 billion, with significant adoption expected across the broader manufacturing sector.
Integration with IoT and AI
Imagine heavy machinery that can predict when it needs a new part before it breaks down. That's the power of combining 3D printing with IoT (Internet of Things) sensors and artificial intelligence. IoT sensors can monitor the performance of different components, and AI algorithms can analyze this data to identify potential failures. When a problem is detected, a replacement part can be 3D printed on demand, minimizing downtime and keeping operations running smoothly. It's all about smarter, more efficient machines.
Scalability of 3D Printing
Right now, 3D printing is often used for prototypes, custom parts, and small-batch production. But what about scaling it up to mass production? That's the next big challenge. We need to develop faster, more efficient 3D printing processes that can handle the demands of large-scale manufacturing. This includes:
- Developing new materials that are stronger and more durable.
- Improving the speed and accuracy of 3D printers.
- Creating automated systems for post-processing and finishing parts.
Overcoming these challenges will unlock the full potential of 3D printing and allow it to become a mainstream manufacturing technique for heavy machinery.
Potential for Mass Customization
One of the most exciting possibilities of 3D printing is the ability to create highly customized parts and machines. Instead of being limited to standard designs, manufacturers can tailor equipment to meet the specific needs of their customers. This could lead to:
- More efficient machines that are optimized for specific tasks.
- Reduced material waste, as parts are only made to the exact specifications required.
- New business models based on personalized products and services.
Mass customization could revolutionize the heavy machinery industry, allowing manufacturers to design for manufacturability and offer a level of personalization that was previously impossible.
Wrapping It Up
In the end, 3D printing is shaking things up in heavy machinery manufacturing. It’s not just about making parts faster; it’s about changing how companies think about design and production. With the ability to create complex shapes and reduce waste, manufacturers can save time and money while also being more innovative. As more companies jump on board, we can expect to see even more exciting developments. The future looks bright for 3D printing in this field, and it’s clear that those who embrace it will have a leg up in the competitive market.
Frequently Asked Questions
What is 3D printing and how does it work in heavy machinery?
3D printing is a technology that creates objects by adding material layer by layer. In heavy machinery, it helps produce parts and components quickly and with less waste.
How does 3D printing change the design process for heavy machinery?
It allows engineers to create more complex designs that were not possible before, making it easier to customize parts for specific needs.
What are the main benefits of using 3D printing in manufacturing?
Some benefits include faster production times, less material waste, and the ability to quickly make changes to designs.
Can 3D printing help reduce costs in heavy machinery manufacturing?
Yes, it can lower costs by reducing the need for expensive tools and by minimizing material waste.
How does 3D printing affect the supply chain for heavy machinery?
It allows for on-demand production, which means parts can be made as needed, reducing the need for large inventories and helping to avoid delays.
What materials can be used in 3D printing for heavy machinery?
A variety of materials can be used, including metals, plastics, and ceramics, allowing for strong and durable parts.