The Future of Industrial Machinery: Trends to Watch in 2024
.png)
As we look ahead to 2024, the industrial machinery sector is set to experience significant changes. These shifts are driven by new technologies, sustainability goals, and evolving workforce dynamics. Understanding these trends will be crucial for manufacturers aiming to stay competitive in a rapidly changing landscape. Here are the key takeaways to keep in mind for the future of industrial machinery.
Key Takeaways
- Smart factories will become more common, using technology like IoT and data analytics to improve efficiency.
- Sustainability efforts will grow, with a focus on reducing carbon footprints and adopting eco-friendly practices.
- Digital transformation will accelerate, incorporating AI, digital twins, and virtual reality into manufacturing processes.
- Supply chain resilience will be prioritized, with data-driven strategies to manage disruptions effectively.
- The workforce will evolve, addressing labor shortages through training and adapting to the impact of automation.
Embracing Smart Factory Technologies
In today's manufacturing world, smart factories are becoming essential. These factories use advanced technologies like AI, IoT, and data analytics to improve production. They help manufacturers gain real-time insights and make better decisions. Here are some key areas to focus on:
Integration of IoT in Manufacturing
- IoT devices connect machines and systems, allowing for better communication.
- They help monitor equipment health and performance, reducing downtime.
- Manufacturers can gather valuable data to improve processes and efficiency.
Role of Data Analytics in Smart Factories
- Data analytics helps in understanding trends and patterns in production.
- It enables manufacturers to make informed decisions based on real-time data.
- Companies can optimize their operations, leading to cost savings and improved quality.
Advancements in Robotics and Automation
- Robotics is transforming manufacturing by automating repetitive tasks.
- Advanced robots can work alongside humans, enhancing productivity.
- Automation reduces human error and increases safety in the workplace.
The future of manufacturing is bright, driven by technology and the need for greater adaptability.
As we move into 2024, embracing these smart factory technologies will be crucial for manufacturers to stay competitive and efficient.
Sustainability and Green Manufacturing
In today's world, sustainability is becoming a key focus for manufacturers. Companies are realizing that adopting green practices is not just good for the planet, but also beneficial for their business. Here are some important trends to consider:
Carbon Neutrality Goals
- Many companies are setting carbon neutrality goals to reduce their greenhouse gas emissions.
- A significant number of businesses are committing to removing as much carbon dioxide from the atmosphere as they emit.
- This shift is largely influenced by younger generations, especially Gen Z, who are pushing for more sustainable practices in the manufacturing sector.
Eco-friendly Manufacturing Processes
- Manufacturers are exploring various eco-friendly processes, such as:
- Using renewable energy sources for production.
- Implementing recycling programs to minimize waste.
- Investing in energy-efficient machinery to lower energy consumption.
- These practices not only help the environment but can also lead to cost savings in the long run.
Impact of ESG on Industrial Practices
- Environmental, Social, and Governance (ESG) factors are becoming increasingly important in the manufacturing industry.
- Companies that prioritize ESG are often viewed more favorably by consumers, leading to increased sales and customer loyalty.
- A recent survey found that 84% of consumers are willing to pay more for products from socially responsible companies.
By focusing on sustainability, manufacturers can create a positive impact on the environment while also enhancing their brand reputation and profitability.
Overall, the move towards sustainability and green manufacturing is not just a trend; it is becoming a necessity for companies looking to thrive in the future.
Digital Transformation in Industrial Machinery
The manufacturing industry is undergoing a significant change as it embraces digital transformation. This shift is not just about using new technology; it’s about changing how businesses operate to become more efficient and responsive to market needs.
Adoption of AI and Machine Learning
- Artificial Intelligence (AI) is becoming a key player in manufacturing. It helps in:
- Automating routine tasks.
- Enhancing product design.
- Improving quality control.
- Machine learning allows systems to learn from data, making them smarter over time.
Role of Digital Twins in Manufacturing
- Digital twins are virtual models of physical objects. They help manufacturers:
- Monitor equipment in real-time.
- Simulate changes before applying them in the real world.
- Predict maintenance needs, reducing downtime.
Industrial Metaverse and Virtual Reality Applications
- The industrial metaverse is a digital space where manufacturers can:
- Create virtual representations of their factories.
- Train employees in a safe environment.
- Test products without physical prototypes.
The future of manufacturing lies in the integration of technology and data, which will lead to smarter operations and better products.
In summary, the digital transformation in manufacturing is set to revolutionize how companies operate, making them more agile and efficient. As we move into 2024, these trends will continue to shape the industry, driving innovation and growth.
Navigating Supply Chain Challenges
Strategies for Supply Chain Resilience
To tackle the ongoing challenges in supply chains, manufacturers are adopting several key strategies:
- Leveraging Technology: Many manufacturers are using digital tools to improve visibility and resilience in their supply chains. For instance, 76% of manufacturers are now adopting these technologies to enhance transparency. This includes using software for work instructions and digital ecosystems that help streamline workflows and keep communication open with suppliers.
- Strengthening Relationships: Building strong connections with suppliers can lead to better support during tough times. Companies with solid relationships may receive benefits like modified shipment routes and prioritized access to materials in high demand.
- Diversifying Suppliers: To avoid relying on a few main suppliers, many businesses are investing in multiple suppliers for the same materials. This strategy helps ensure they can still access essential materials even if their primary suppliers face disruptions.
Impact of Global Disruptions on Supply Chains
Despite some signs of recovery, supply chains are still vulnerable to various external threats. Events like natural disasters, geopolitical tensions, and trade disputes can cause significant delays. For example, the average delivery time for production materials was 87 days in August 2023, which is an improvement from 100 days in July 2022 but still longer than the pre-pandemic average of 63 days.
Data-driven Supply Chain Management
Using data effectively is crucial for managing supply chains. By analyzing data, manufacturers can identify potential risks and make informed decisions to enhance their supply chain strategies. This approach not only helps in mitigating risks but also improves overall efficiency.
In 2024, understanding and adapting to supply chain challenges will be essential for manufacturers to thrive.
Workforce Evolution in Manufacturing
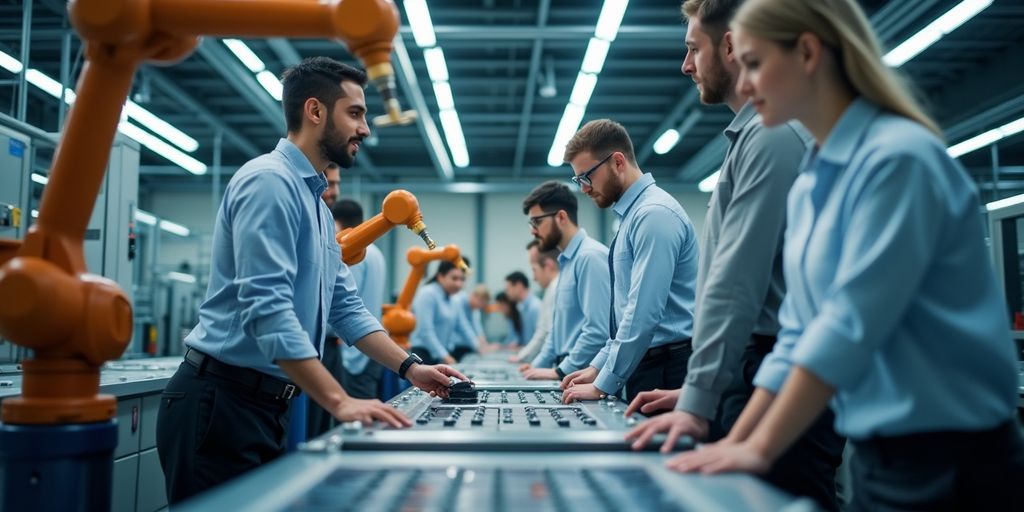
Addressing Skilled Labor Shortages
The manufacturing industry is facing a significant challenge with skilled labor shortages. Many workers are retiring, and younger generations are not filling these roles. To tackle this issue, manufacturers can:
- Invest in training programs to help new employees gain necessary skills.
- Offer competitive wages to attract talent.
- Create flexible work environments to appeal to younger workers.
Training and Development in the Digital Age
As technology evolves, so must the workforce. Companies are focusing on continuous learning to keep their employees updated. Effective strategies include:
- Online courses that allow employees to learn at their own pace.
- In-person workshops for hands-on experience.
- Mentorship programs to guide new employees.
Impact of Automation on Employment
Automation is changing the landscape of manufacturing jobs. While some jobs may be lost, new opportunities are also created. It's essential to:
- Embrace technology to improve efficiency.
- Reskill workers to handle new roles created by automation.
- Promote a culture of adaptability within the workforce.
The future of manufacturing relies on a skilled and adaptable workforce. By investing in training and embracing technology, companies can ensure they remain competitive in a rapidly changing industry.
Innovations in Product Lifecycle Management
Integration of Cloud Technologies
The use of cloud technologies is transforming how manufacturers manage their product lifecycles. By moving to the cloud, companies can:
- Access real-time data from anywhere.
- Collaborate more effectively across teams.
- Scale their operations without heavy investments in hardware.
Enhancing Product Design with AI
Artificial Intelligence (AI) is playing a crucial role in product design. It helps manufacturers to:
- Analyze customer feedback quickly.
- Predict design flaws before production.
- Optimize materials for better performance.
AI-driven design tools are becoming essential for staying competitive in the market.
Lifecycle Assessment for Sustainability
Sustainability is a key focus for manufacturers today. Conducting a lifecycle assessment helps companies to:
- Identify areas for reducing waste.
- Ensure compliance with new regulations.
- Improve their overall environmental impact.
As regulations around sustainability tighten, manufacturers must adapt their practices to meet new standards and expectations.
In summary, innovations in product lifecycle management are essential for manufacturers to remain competitive and sustainable in the evolving market landscape. Embracing these trends will not only enhance efficiency but also align with the growing demand for eco-friendly practices.
Cybersecurity in Industrial Machinery
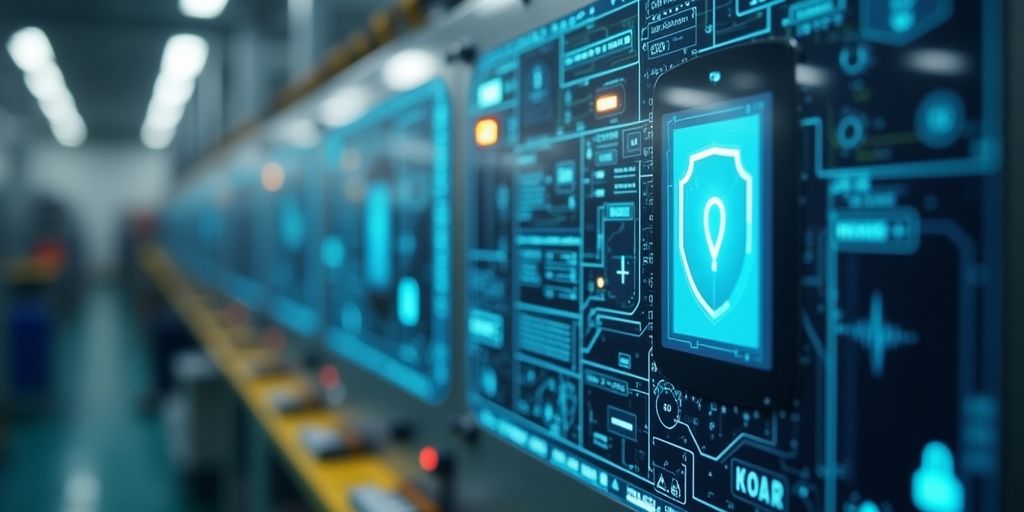
In today's world, cybersecurity is a major concern for industrial machinery. As factories become smarter and more connected, they also become more vulnerable to attacks. In fact, a recent study found that 65% of manufacturing organizations faced ransomware attacks, a significant increase from previous years. This highlights the urgent need for manufacturers to prioritize their cybersecurity measures.
Protecting Industrial IoT Systems
- Regular Updates: Ensure all systems and software are up-to-date to protect against vulnerabilities.
- Access Control: Limit access to sensitive data and systems to only those who need it.
- Employee Training: Regularly train employees on cybersecurity best practices to prevent human errors.
Cyber Threats in Manufacturing
Manufacturers face various cyber threats, including:
- Ransomware: Malicious software that locks data until a ransom is paid.
- Phishing Attacks: Deceptive emails that trick employees into revealing sensitive information.
- Data Breaches: Unauthorized access to confidential data, which can lead to significant financial losses.
Building a Secure Manufacturing Environment
To create a secure environment, manufacturers should:
- Develop a comprehensive incident response plan.
- Conduct regular security audits to identify weaknesses.
- Collaborate with suppliers to ensure their cybersecurity measures are robust.
Cybersecurity is not just an IT issue; it’s a critical part of business strategy. Manufacturers must take proactive steps to protect their operations and data from cyber threats.
Conclusion
As we look towards 2024, the industrial machinery sector is set to undergo significant changes. The rise of smart factories and advanced technologies will reshape how we manufacture goods. Companies are focusing on using new tools like AI and automation to improve efficiency and safety. Sustainability is also becoming a key priority, with many businesses aiming for greener practices. While challenges like labor shortages and supply chain issues remain, the future holds exciting possibilities. By embracing these trends, manufacturers can not only survive but thrive in a rapidly changing environment.
Frequently Asked Questions
What are smart factories?
Smart factories use advanced technology like IoT and robots to improve production. They help make manufacturing faster and more efficient.
How is sustainability affecting manufacturing?
Manufacturers are focusing on eco-friendly practices to reduce their carbon footprint and meet environmental standards.
What role does AI play in manufacturing?
AI helps manufacturers analyze data, improve processes, and create better designs. It can also predict maintenance needs.
What challenges are supply chains facing?
Supply chains are dealing with disruptions from global events and are looking for ways to be more flexible and resilient.
How is the workforce changing in manufacturing?
There is a shortage of skilled workers, so companies are investing in training programs to help employees adapt to new technologies.
Why is cybersecurity important in manufacturing?
As factories become more connected, protecting against cyber threats is crucial to ensure safety and efficiency in operations.