The Essential Guide to Maintaining Your Heavy Equipment
.png)
Hey there! If you're in the business of using heavy equipment, you know how vital it is to keep those machines running smoothly. Whether it's for construction, farming, or any other industry, regular maintenance isn't just a good idea—it's a must. It helps you avoid those frustrating breakdowns and saves you money in the long haul. In this guide, we're diving into the nuts and bolts of keeping your heavy equipment in top shape. From setting up a maintenance schedule to knowing what parts to check, we've got you covered. Let's get started!
Key Takeaways
- Regular maintenance is crucial to prevent costly breakdowns.
- Create a maintenance schedule that fits your equipment's usage.
- Always check key components like the engine and hydraulic systems.
- Proper lubrication and fluid management extend equipment life.
- Training operators on safety and maintenance can save time and money.
Understanding the Basics of Heavy Equipment Maintenance
Importance of Regular Maintenance
Regular maintenance is the backbone of keeping heavy equipment in top shape. Skipping these checks can lead to unexpected breakdowns and costly repairs. By sticking to a routine, you can catch small issues before they snowball into big problems. This proactive approach not only saves money but also extends the lifespan of your machinery. Plus, it ensures that your equipment is always ready to roll when you need it most.
Common Maintenance Challenges
Maintaining heavy equipment isn't always smooth sailing. One major challenge is dealing with wear and tear that comes from constant use. Parts can degrade over time, leading to potential failures if not addressed promptly. There's also the issue of finding the right parts and tools, which can sometimes be a hassle. And let's not forget the weather—extreme conditions can make maintenance tasks tougher than usual.
Benefits of Proper Maintenance
The benefits of keeping up with maintenance are numerous. First off, it boosts the reliability of your equipment, meaning fewer headaches on the job site. Proper maintenance also enhances safety, reducing the risk of accidents caused by equipment failure. Moreover, it can improve efficiency, as well-maintained machines tend to operate more smoothly. In the long run, this attention to detail can save you a significant amount of money by avoiding major repairs and extending the life of your equipment.
Taking the time to maintain your heavy equipment is an investment in your business's future. It keeps your operations running smoothly and your costs down.
Creating an Effective Maintenance Schedule
Developing a Maintenance Plan
Creating a maintenance plan is like building a roadmap for your heavy equipment. A well-structured plan helps avoid unexpected breakdowns and costly repairs. Start by listing all the equipment you have. Next, identify the specific maintenance needs for each machine based on the manufacturer's recommendations and your operational requirements. It's crucial to set clear responsibilities for who will oversee the plan, whether it's a senior technician or the owner in a smaller setup. This ensures accountability and consistency.
Scheduling Routine Inspections
Routine inspections are the backbone of any maintenance schedule. They help catch small issues before they turn into big problems. Consider setting up a preventive maintenance schedule that outlines when each piece of equipment needs attention. This could be based on hours of operation, mileage, or even calendar dates. Regular inspections help in planning for parts and tools, ensuring everything is ready when needed.
Adjusting for Seasonal Changes
Don't forget to adjust your maintenance schedule for seasonal changes. Different weather conditions can impact your equipment in various ways. For instance, colder months may require more frequent checks on batteries and antifreeze levels, while hotter months might need extra attention to cooling systems. Being proactive about these seasonal adjustments can help extend the life of your equipment and keep it running smoothly.
Consistent and timely maintenance not only keeps your machinery in top shape but also boosts productivity and safety on-site. It's about being prepared and staying ahead of potential issues.
Key Components to Inspect Regularly
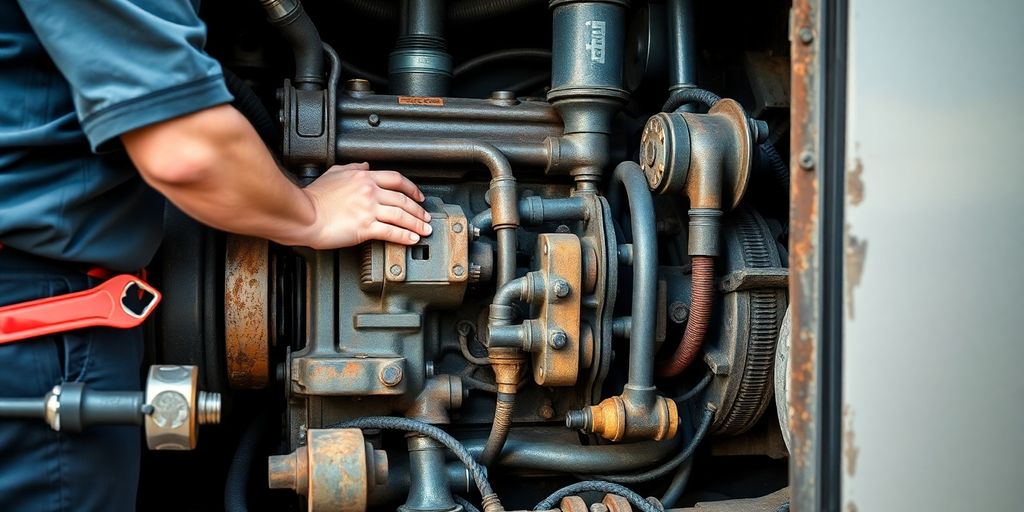
Engine and Transmission Checks
Engines are the heart of any heavy equipment. Regular inspections can prevent unexpected breakdowns that could halt your operations. Make sure to check the oil levels and change them as needed. Look for any signs of leaks or unusual noises. Inspect the air filters and replace them if they appear clogged. Transmission checks are equally important; ensure the fluid levels are adequate and that there are no signs of wear in the gears.
Hydraulic System Maintenance
Hydraulic systems are critical for the smooth operation of heavy machinery. Regularly inspect hoses for any signs of wear or leaks. Check the hydraulic fluid levels and top them up if necessary. It's also a good idea to monitor the pressure and make sure it's within the recommended range. Properly functioning hydraulics can save you from costly repairs and downtime.
Tire and Track Inspections
Whether your equipment runs on tires or tracks, regular inspections are vital. For tires, check the pressure and look for any signs of wear or punctures. Tracks require a bit more attention; inspect for any broken links or uneven wear. Keeping these components in good shape ensures your equipment moves efficiently and safely across different terrains.
Regular maintenance checks not only extend the life of your equipment but also keep your operations running smoothly and safely. Don't overlook these inspections—they're your first line of defense against costly repairs.
For a comprehensive preventive maintenance checklist that includes inspecting for visible damage such as dents, rust, and chipped paint, be sure to incorporate these steps into your routine.
Best Practices for Lubrication and Fluid Management
Choosing the Right Lubricants
Picking the right lubricant isn’t just a suggestion; it’s a must. You want to match the lubricant to the specific needs of your heavy equipment. Not all oils are created equal, and using the wrong type can lead to increased wear and tear. Always follow the manufacturer’s guidelines for selecting lubricants, whether it’s for the engine, hydraulics, or other components. This ensures optimal performance and longevity.
Monitoring Fluid Levels
Keeping an eye on fluid levels is like checking your car's gas gauge. Regular checks can prevent major headaches down the road. Make it a habit to inspect oil, coolant, and hydraulic fluid levels before starting up your machines. If you notice any sudden drops, it might be a sign of a leak or other issue that needs immediate attention.
Preventing Contamination
Contamination is the silent enemy of any fluid system. Dirt, water, or other impurities can sneak in, leading to corrosion and system failures. To keep your fluids clean, ensure all caps and seals are secure. Use clean containers and tools when refilling fluids. And remember, mixing different types of fluids can lead to chemical reactions that might harm your equipment. Stick to one type and keep it pure.
Training and Safety for Equipment Operators
Importance of Operator Training
Operating heavy machinery isn't just about turning the key and moving dirt. It's a skill that requires proper training. Operators need to know how to handle the equipment safely and efficiently. This training not only improves productivity but also reduces the risk of accidents on site. Emphasizing the importance of training helps ensure that operators can handle unexpected situations and understand the limitations of the machinery.
Safety Protocols and Guidelines
Safety on the job site is non-negotiable. Implementing clear safety protocols is essential. Operators should always:
- Conduct a pre-operation inspection.
- Wear appropriate personal protective equipment (PPE).
- Be aware of their surroundings and communicate with other team members.
By following these guidelines, operators can minimize risks and create a safer working environment for everyone.
Identifying Early Warning Signs
Recognizing early warning signs of equipment failure can prevent costly repairs and downtime. Operators should be trained to:
- Listen for unusual noises.
- Check for leaks or unusual vibrations.
- Monitor performance indicators on the equipment's dashboard.
Early detection of issues allows for timely maintenance, keeping the equipment running smoothly and safely.
Proper training and adherence to safety protocols not only protect operators but also extend the lifespan of the equipment, ensuring a more efficient and cost-effective operation.
Utilizing Technology in Equipment Maintenance
Benefits of Maintenance Software
Using maintenance software can really change the game when it comes to keeping track of your equipment. These programs help you manage schedules, track repairs, and even predict when something might go wrong. Having everything in one place makes it easier to keep your machines running smoothly. Plus, you can quickly access the history of any equipment to see what's been done and what needs attention. This kind of software also helps in cutting down on paperwork and streamlining communication between team members.
Tracking Maintenance History
Keeping a detailed log of all maintenance activities is crucial. With software, you can easily track who did what, when, and how long it took. This information is not just about keeping records; it helps in planning future maintenance tasks and budgeting. You can analyze how much time and resources are spent on each piece of equipment and adjust your strategy accordingly. This way, you're not just reacting to problems but proactively managing your assets.
Using Diagnostic Tools
Diagnostic tools are a must-have for any serious maintenance team. These tools help you identify issues before they become major problems. By using sensors and other tech, you can monitor the condition of your equipment in real-time. This is where Predictive Maintenance (PdM) comes into play. PdM uses sensor data to predict when maintenance should be performed, reducing downtime and improving efficiency. Investing in these tools might seem like a big step, but the payoff in terms of reduced breakdowns and longer equipment life is worth it.
Technology in maintenance isn't just about having the latest gadgets; it's about using the right tools to keep your equipment in top shape. With the right tech, you can save money, reduce downtime, and make your maintenance process more efficient.
Cost Management and Budgeting for Maintenance

Analyzing Maintenance Costs
Keeping track of your maintenance expenses is like balancing your checkbook. It’s essential to know where your money is going. Start by breaking down costs into categories like labor, parts, and vendor fees. Tracking these expenses helps in identifying areas where you might overspend. For instance, if labor costs are high, consider training your team to improve efficiency. Use a computerized maintenance management system (CMMS) to gather data and generate reports, which can offer insights into cost trends.
Budgeting for Repairs and Replacements
Creating a budget for repairs and replacements is not just about setting aside money. It involves forecasting future needs based on past data. Look at the history of your equipment failures and plan accordingly. You might want to establish a reserve fund for unexpected breakdowns. Regularly review your budget to ensure it aligns with your maintenance goals. By doing so, you can avoid financial surprises and ensure the maintenance department functions effectively.
Maximizing Equipment Lifespan
Extending the life of your equipment is a smart way to save money. Regular maintenance, timely repairs, and using quality parts can add years to your machinery. Consider implementing a preventive maintenance program. This proactive approach can help you catch issues early before they become costly problems. Keep an eye on metrics like mean-time-between-failures (MTBF) to gauge equipment health.
A well-planned maintenance strategy not only keeps your equipment running smoothly but also optimizes your investment over time.
In summary, effective cost management in maintenance requires a mix of careful planning, regular review, and strategic decision-making. By focusing on these areas, you can maintain your heavy equipment efficiently without breaking the bank.
Wrapping It Up
So, there you have it. Keeping your heavy equipment in top shape isn't just about following a checklist—it's about making it a habit. Regular maintenance, inspections, and a bit of TLC can go a long way in keeping those machines running smoothly. Sure, it might seem like a lot of work, but trust me, it's worth it in the long run. You'll save on costly repairs, avoid unexpected downtime, and maybe even extend the life of your equipment. Plus, a well-maintained machine is a safer machine, and that's something everyone can get behind. So, roll up those sleeves and get to it—your equipment will thank you!
Frequently Asked Questions
Why is regular maintenance important for heavy equipment?
Regular maintenance keeps your machines running smoothly, prevents unexpected breakdowns, and extends their lifespan.
What should I include in a maintenance schedule?
A good maintenance schedule should include routine inspections, timely repairs, and seasonal adjustments to keep your equipment in top shape.
How often should I check the engine and transmission?
It's best to check the engine and transmission regularly, ideally before each use, to ensure they are functioning properly.
What are the benefits of using the right lubricants?
Using the right lubricants reduces friction, prevents wear and tear, and helps your equipment run efficiently.
Why is operator training important?
Training helps operators use equipment safely and efficiently, reducing the risk of accidents and equipment damage.
How can technology help in equipment maintenance?
Technology, like maintenance software, helps track repairs, schedule inspections, and monitor equipment health for better management.