Industrial Machinery Safety: Essential Tips for Your Workplace
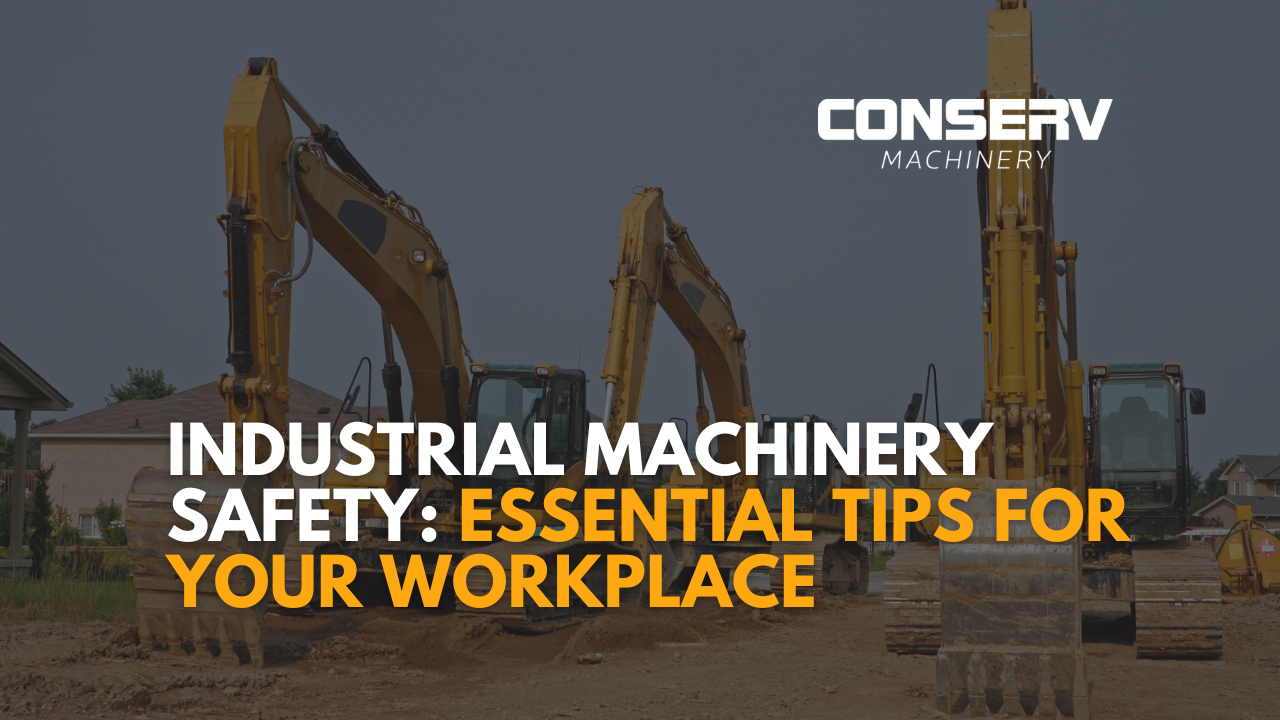
Industrial Machinery Safety: Essential Tips for Your Workplace
Ensuring safety in industrial settings is crucial for protecting workers and maintaining a productive environment. This article will cover essential tips for industrial machinery safety, focusing on how to create a culture of safety, the importance of personal protective equipment (PPE), and strategies for keeping the workplace secure. By following these guidelines, you can help prevent accidents and injuries in your workplace.
Key Takeaways
- Create a culture of safety by encouraging open communication among employees.
- Ensure proper use of personal protective equipment (PPE) to minimize risks.
- Keep work areas organized and free from hazards to prevent accidents.
- Only allow trained and authorized personnel to operate machinery.
- Regularly conduct inspections and audits to maintain a safe working environment.
Fostering a Safety-Focused Culture
Creating a safety-focused culture is essential in any workplace, especially in industrial settings. This culture encourages everyone to prioritize safety and communicate openly about potential hazards. Here are some key components:
Encouraging Open Communication
- Listen to Employees: Make sure workers feel comfortable sharing their safety concerns.
- Feedback Channels: Establish ways for employees to report issues without fear of retaliation.
- Regular Updates: Keep everyone informed about safety policies and changes.
Implementing Safety Committees
- Diverse Representation: Include members from different departments to get various perspectives.
- Regular Meetings: Schedule consistent meetings to discuss safety issues and solutions.
- Action Plans: Develop and implement plans based on committee discussions to improve safety.
Leadership's Role in Safety
- Lead by Example: Managers should follow safety protocols to set a standard.
- Training and Resources: Provide necessary training and resources to all employees.
- Recognize Safe Behavior: Acknowledge and reward employees who demonstrate safe practices.
A strong safety culture not only protects employees but also enhances productivity and morale. Safety is everyone's responsibility.
By fostering a safety-focused culture, companies can significantly reduce workplace accidents and create a more positive environment for all employees. Remember, manufacturing safety is about teamwork and commitment to a safer workplace.
Ensuring Proper Use of Personal Protective Equipment (PPE)
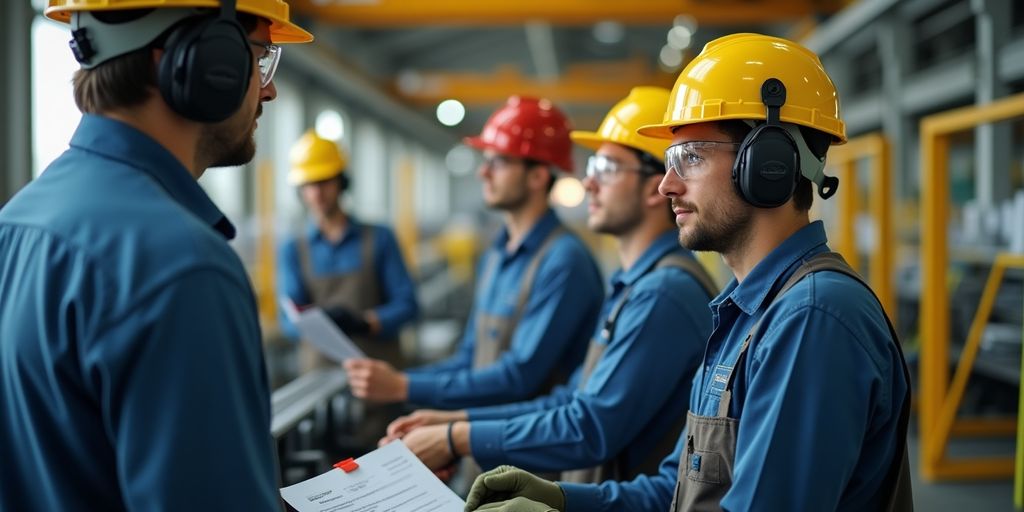
Types of PPE Required
Personal Protective Equipment (PPE) is crucial for keeping workers safe in industrial settings. Here are some common types of PPE:
- Hard hats: Protect against head injuries from falling objects.
- Safety glasses: Shield eyes from flying debris and chemicals.
- Hearing protection: Prevent hearing loss in noisy environments.
- Gloves: Safeguard hands from cuts and chemicals.
- Protective clothing: Offers a barrier against hazardous materials.
Training Employees on PPE Usage
To ensure that all employees use PPE correctly, training is essential. This training should cover:
- Proper fitting: Ensure PPE fits well to provide maximum protection.
- Usage guidelines: Teach when and how to wear each type of PPE.
- Maintenance: Instruct on how to clean and store PPE properly.
Regular PPE Inspections
Regular inspections of PPE are necessary to maintain safety standards. Employers should:
- Check for wear and tear on all equipment.
- Ensure that PPE is clean and functional.
- Replace any damaged items immediately to avoid risks.
Remember: All personal protective equipment (PPE) should be well maintained, clean, and reliable. Employers should check if it is safely designed and constructed to ensure maximum protection for workers.
Maintaining a Safe Work Environment
Creating a safe work environment is crucial for the well-being of all employees. A clean and organized workspace can significantly reduce accidents. Here are some key practices to maintain safety:
Keeping Work Areas Clear
- Regularly remove clutter from workspaces to prevent accidents.
- Ensure that emergency exits are unobstructed at all times.
- Designate specific areas for tools and materials to keep them organized.
Proper Storage of Hazardous Materials
- Store hazardous materials in clearly labeled containers.
- Keep flammable substances away from heat sources.
- Regularly check storage areas for leaks or spills to prevent accidents.
Regular Safety Audits
- Conduct safety audits at least once a month to identify potential hazards.
- Involve employees in the audit process to gain insights on safety improvements.
- Document findings and create action plans to address any issues.
Maintaining a safe work environment is not just about following rules; it’s about fostering a culture of safety where everyone feels responsible for their own safety and that of their coworkers.
By implementing these practices, companies can create a safer workplace that protects employees and enhances productivity. Remember, safety is a shared responsibility!
Training and Authorizing Machinery Operators
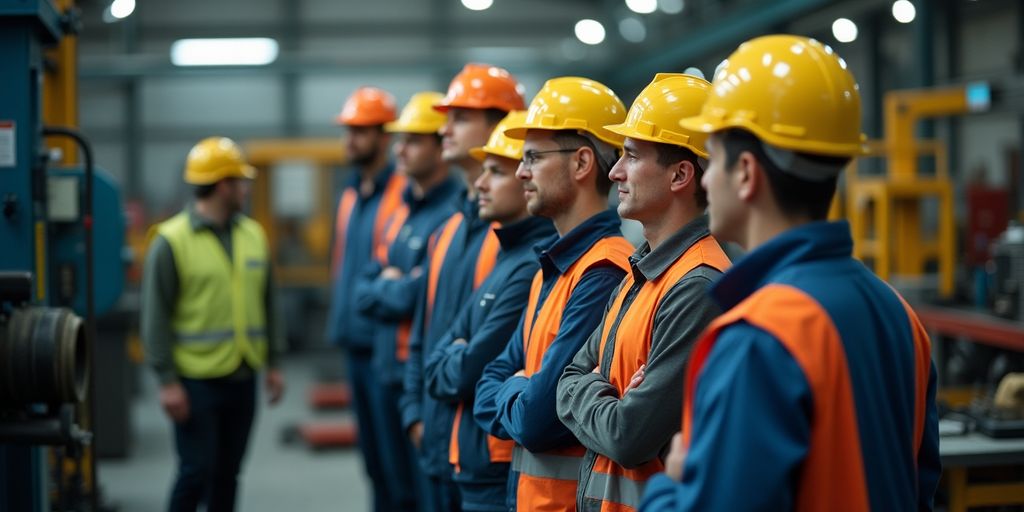
Certification Requirements
To operate machinery safely, employees must meet specific certification requirements. This ensures that they have the necessary skills and knowledge. Here are the key steps:
- Complete machine safety training.
- Pass a written test on safety protocols.
- Demonstrate practical skills on the machinery.
Ongoing Training Programs
Training doesn't stop after initial certification. Regular ongoing training programs are essential to keep operators updated on safety practices and machinery changes. Consider the following:
- Schedule refresher courses every year.
- Include new safety regulations in training.
- Use hands-on training to reinforce learning.
Monitoring and Supervision
Supervision is crucial to ensure that operators follow safety protocols. Here are some effective monitoring strategies:
- Conduct regular safety audits.
- Assign experienced operators to mentor new ones.
- Use checklists to verify compliance with safety standards.
Regular training and supervision help create a safer work environment, reducing the risk of accidents and injuries.
By focusing on these areas, companies can ensure that their machinery operators are well-trained and authorized to work safely with industrial equipment.
Implementing Risk Management Strategies
In any workplace, especially those involving heavy machinery, risk management is crucial. It helps in identifying and reducing potential dangers that could lead to accidents. Here are some key strategies to implement:
Conducting Risk Assessments
- Identify hazards: Look for anything that could cause harm, such as moving parts or electrical issues.
- Evaluate risks: Determine how likely it is for these hazards to cause an accident and how severe the consequences could be.
- Prioritize actions: Focus on the most dangerous risks first to ensure safety.
Developing Emergency Procedures
- Create a plan: Outline steps to take in case of an emergency, such as a machine malfunction or an injury.
- Train employees: Make sure everyone knows the emergency procedures and practices them regularly.
- Review and update: Regularly check the emergency plan to ensure it remains effective and relevant.
Using Safety Management Software
- Track incidents: Use software to log accidents and near misses, helping to identify patterns.
- Manage compliance: Ensure that all safety regulations are being followed and documented.
- Analyze data: Use the information gathered to improve safety measures and reduce risks.
Implementing these strategies not only helps in minimizing hazards but also fosters a culture of safety within the workplace. Regularly reviewing and updating these practices is essential for ongoing safety improvements.
Promoting Safe Work Practices
Creating a safe workplace is everyone's responsibility. By promoting safe work practices, you can help reduce accidents and injuries. Here are some effective strategies:
Regular Safety Meetings
- Hold safety meetings at least once a month to discuss safety concerns and updates.
- Encourage employees to share their experiences and suggestions for improvement.
- Use these meetings to review safety protocols and ensure everyone understands them.
Encouraging Reporting of Unsafe Conditions
- Make it easy for employees to report unsafe conditions without fear of punishment.
- Implement a simple reporting system, such as a suggestion box or an online form.
- Recognize and reward employees who report hazards, fostering a culture of safety.
Incorporating Safety into Daily Routines
- Integrate safety checks into daily tasks, such as inspecting equipment before use.
- Remind employees to wear their personal protective equipment (PPE) at all times.
- Encourage everyone to stay aware of their surroundings and potential hazards.
A safe workplace is not just about rules; it’s about creating a culture where everyone feels responsible for safety.
By following these practices, you can help ensure that safety becomes a natural part of your workplace culture. Remember, placing signs close to hazardous chemicals and machines is essential for adequate safety in the workplace. Make an effort to point out dangerous areas and keep everyone informed!
Conducting Pre-Use Machinery Inspections
Before using any industrial machinery, it is crucial to perform a thorough pre-use inspection. This step is essential for ensuring safety and preventing accidents in the workplace. Regular inspections help catch workplace safety hazards before they get out of hand. Here are the key components of a pre-use inspection:
Visual and Functional Checks
- Visual Inspection: Look for any visible defects or damage on the machinery. This includes checking for loose parts, leaks, or any signs of wear and tear.
- Functional Check: Ensure that all controls, safety devices, and other components are working correctly. Test the machinery to confirm it operates as intended.
- Safety Guards: Verify that all machine guards are in place and functioning properly to protect against injury.
Identifying Potential Hazards
- Trained Personnel: Only trained individuals should conduct these inspections to identify potential hazards effectively.
- Documentation: Keep a record of inspection results to track any issues and ensure they are addressed promptly.
- Immediate Reporting: Report any problems found during the inspection to a supervisor right away.
Final Thoughts on Industrial Machinery Safety
In conclusion, keeping your workplace safe when using industrial machinery is very important. By following the tips we discussed, like wearing the right safety gear and keeping work areas tidy, you can help prevent accidents. It’s also crucial to make sure only trained people operate the machines. Remember, safety is a team effort. Everyone in the workplace should be aware of the rules and feel comfortable speaking up about any dangers. By working together, we can create a safer environment for everyone.
Frequently Asked Questions
What is a safety-focused culture in the workplace?
A safety-focused culture means everyone in the workplace, from managers to workers, cares about safety. It encourages people to talk openly about safety issues and share their thoughts.
Why is Personal Protective Equipment (PPE) important?
PPE, like helmets and gloves, protects workers from injuries. Wearing the right PPE helps keep everyone safe from accidents and hazards.
How can I keep my work area safe?
To keep your work area safe, always keep it clean and organized. Make sure that walkways and emergency exits are clear of any obstacles.
What steps should I take before using a machine?
Before using a machine, check it carefully. Look for any visible damage and make sure all parts are working correctly.
How often should safety training happen?
Safety training should happen regularly. New employees should get training right away, and existing workers should have refresher courses often.
What should I do if I see a safety hazard?
If you see something unsafe, report it to your supervisor immediately. They are responsible for fixing safety issues in the workplace.