How to Prevent Costly Downtime with Proper Machinery Maintenance
.png)
Downtime can be a huge headache for any business. It costs money, disrupts production, and can lead to unhappy customers. To keep your machinery running smoothly and avoid those costly interruptions, you need to be proactive. This article will guide you through some practical steps on how to prevent costly downtime with proper machinery maintenance. We'll cover everything from risk audits to training your team effectively, so you can keep your operations running without a hitch.
Key Takeaways
- Conduct regular risk audits to identify outdated equipment and safety hazards.
- Establish a preventive maintenance plan to catch issues before they escalate.
- Use data and software tools to track equipment performance and predict failures.
- Train your maintenance team regularly to ensure they are knowledgeable and prepared.
- Calculate downtime costs to understand the financial impact and justify maintenance efforts.
Conduct Regular Risk Audits
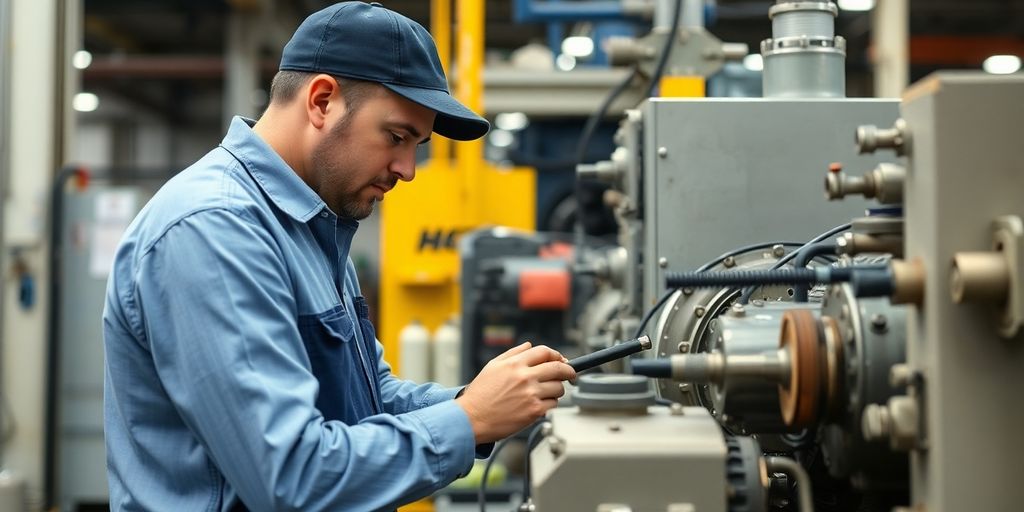
Most maintenance teams don't jump at the chance to do risk audits, but honestly, they're super important for keeping downtime low. Think of it as a health check for your equipment. You wouldn't skip your own doctor's appointment, right? Same idea here. Let's get into the details.
Identify Obsolete Equipment
Risk audits help you spot machines that are past their prime. I mean, if you've got a piece of equipment that's been around since the dinosaurs, it's probably time to consider an upgrade. Not only are these old machines more likely to break down, but finding spare parts can be a total nightmare. Sometimes, the company that made the thing doesn't even exist anymore! Replacing it might seem expensive, but trust me, it's often cheaper than constantly patching up a relic. You can consider such a machine obsolete when the time and money it would cost to replace it is more than the cost of acquiring new equipment. For guidance on when upgrading makes sense, check out these signs it's time to upgrade your industrial machines.
Assess Equipment Condition
It's not just about age, though. You need to really look at your equipment. Is it showing signs of wear and tear? Are there weird noises coming from it? Is it running less efficiently than it used to? These are all red flags that something's not right. A good risk audit involves a thorough inspection of each piece of equipment, checking for potential problems before they turn into full-blown breakdowns.
Evaluate Safety Risks
This is a big one. Obsolete or poorly maintained equipment isn't just bad for production; it can also be dangerous. We're talking about potential hazards for your maintenance team and other employees. Risk audits help you identify these safety risks so you can take steps to mitigate them. This could mean anything from replacing a faulty part to implementing new safety procedures. It's all about creating a safer work environment and avoiding costly accidents. Performing a risk audit can also inform you of any obsolete equipment that poses a risk to the safety of your maintenance team or employee well-being, reducing even more costly disaster recovery.
Think of risk audits as an investment, not an expense. They might take some time and effort upfront, but they can save you a ton of money and headaches in the long run. Plus, they help keep your employees safe, which is always the top priority.
Implement a Preventive Maintenance Plan
Okay, so you've audited your risks, now what? It's time to get proactive. A solid preventive maintenance plan is like insurance – you hope you don't need it, but you're sure glad it's there when things go south. It's all about stopping problems before they even start. Think of it as giving your machinery a regular check-up, just like you do with your car or your own health. It's not just about fixing things when they break; it's about preventing the breakdowns in the first place.
Schedule Regular Inspections
This is where the rubber meets the road. Regular inspections are your first line of defense. Set up a schedule – weekly, monthly, quarterly – whatever makes sense for each piece of equipment. Don't just eyeball it; use checklists, document everything, and make sure your team knows what to look for. Are there any weird noises? Any leaks? Any parts that look worn? Catching these things early can save you a ton of grief down the line.
Utilize Predictive Maintenance Techniques
Okay, this sounds fancy, but it's really just about using technology to get ahead of the game. Think vibration analysis, thermal imaging, oil analysis – stuff that can tell you what's going on inside the machine without taking it apart. It's like having a crystal ball for your equipment. This way, you're not just reacting to problems; you're predicting them and fixing them before they cause a shutdown.
Ensure Proper Lubrication
Seriously, don't skimp on the lube. It's the lifeblood of your machinery. Friction is the enemy, and lubrication is your weapon. Make sure you're using the right type of lubricant for each machine, and that you're applying it at the right intervals. A little grease can go a long way in preventing wear and tear, overheating, and all sorts of other nasty problems. It's a simple thing, but it can make a huge difference.
Implementing a preventive maintenance plan isn't just about saving money; it's about peace of mind. Knowing that you're doing everything you can to keep your equipment running smoothly lets you focus on other things, like growing your business.
Leverage Data for Maintenance Decisions
Data is super important when it comes to keeping your machinery up and running. It's not enough to just fix things when they break; you need to understand why they're breaking in the first place. Using data helps you predict problems and fix them before they cause downtime.
Utilize a Computerized Maintenance Management System
A CMMS is basically a central hub for all your maintenance info. Instead of keeping records scattered in different places, a CMMS puts everything in one spot. This makes it easier to track maintenance tasks, schedule work orders, and keep tabs on spare parts. Plus, a good CMMS can even help you predict when equipment might fail, giving you time to take action before it's too late.
Track Equipment Performance Metrics
Keeping an eye on how your equipment is performing is key. This means tracking things like operating hours, temperature, vibration levels, and energy consumption. By monitoring these metrics over time, you can spot patterns and identify potential problems early on. For example, if a machine's temperature starts to creep up, it could be a sign of an impending failure. You can also learn how to boost factory efficiency with advanced machinery.
Analyze Downtime Trends
It's important to dig into the reasons behind your downtime. Don't just count how often equipment breaks down; figure out why it's breaking down. Is it due to old equipment, lack of maintenance, or operator error? Once you know the root causes, you can take steps to address them. For instance, if you notice that a particular machine is frequently down due to a specific part failing, you might want to stock up on that part or consider upgrading the machine.
Analyzing downtime trends can reveal hidden inefficiencies and opportunities for improvement. By understanding the true cost of downtime, you can make informed decisions about maintenance investments and prioritize the most critical equipment.
Train Your Maintenance Team Effectively
It's easy to overlook, but a well-trained maintenance team is your first line of defense against costly downtime. If your team isn't up to par, all the fancy tech and expensive equipment in the world won't save you.
Develop Comprehensive Training Programs
Don't just throw new hires into the deep end. A structured training program is key. This should cover everything from basic equipment operation to advanced troubleshooting. Make sure the training is hands-on, not just theoretical. Include simulations and real-world scenarios to prepare them for anything. A good program will also cover safety procedures, which is non-negotiable. Consider using a CMMS software to track employee training progress and identify skill gaps.
Encourage Continuous Education
Technology changes fast, and your team needs to keep up. Encourage them to attend workshops, seminars, and online courses. Offer certifications and reward those who take the initiative to learn new skills. Continuous learning not only improves their abilities but also boosts morale and job satisfaction. It's an investment that pays off in the long run.
Foster a Culture of Safety
Safety should be more than just a set of rules; it should be ingrained in your team's mindset. Regular safety meetings, drills, and refresher courses are essential. Make sure everyone understands the potential hazards and knows how to mitigate them. A safe work environment is a productive work environment.
A strong safety culture reduces accidents, improves morale, and ultimately saves money by preventing downtime and injuries. It's a win-win for everyone involved.
Calculate and Analyze Downtime Costs
It's easy to overlook the real financial impact of downtime. We're not just talking about lost production; it's a ripple effect that hits various parts of the business. Understanding these costs is the first step in justifying investments in better maintenance practices. Let's break it down.
Identify Direct and Indirect Costs
Direct costs are the obvious ones: the cost of repairs, replacement parts, and the wages of the maintenance team working on the issue. But don't forget the indirect costs! These can include lost production time, missed deadlines, and even potential damage to your company's reputation. For example, consider the cost of spare parts and shipping. It's important to get a handle on all these factors to see the true picture.
Assess Impact on Production
Downtime directly impacts your production capacity. If a machine is down, it's not producing goods, and that means lost revenue. You need to figure out how much each hour of downtime costs you in terms of lost output. This involves calculating the value of the goods you would have produced if the machine were running. It's also important to consider whether you can make up for lost production later or if it's gone for good. Here's a simple way to think about it:
- Calculate the hourly production rate.
- Determine the value of each unit produced.
- Multiply to find the hourly revenue loss during downtime.
Accurately assessing the impact on production helps you prioritize maintenance efforts and justify investments in preventive measures. It's about understanding the trade-off between the cost of maintenance and the potential losses from downtime.
Use Data to Justify Maintenance Investments
Once you have a clear understanding of downtime costs, you can use this data to make a strong case for investing in better maintenance practices. Show management how much money can be saved by reducing downtime through preventive maintenance, improved training, or new equipment. For example, you can use downtime tracking software to collect data. Presenting a clear, data-driven argument is much more effective than simply saying that maintenance is important. Data speaks volumes when it comes to securing budget approvals. Consider these points:
- Quantify the potential savings from reduced downtime.
- Compare the cost of downtime to the cost of maintenance improvements.
- Highlight the long-term benefits of proactive maintenance strategies.
Utilize Technology for Enhanced Maintenance
Technology offers some pretty cool ways to make maintenance easier and more effective. It's not just about fancy gadgets; it's about using the right tools to get the job done smarter and faster. Let's look at some ways tech can help keep your machinery running smoothly.
Incorporate IoT Devices
IoT (Internet of Things) devices can be game-changers. Think sensors attached to your equipment that constantly monitor things like temperature, vibration, and pressure. These devices send data in real-time, allowing you to spot potential problems before they become major headaches. It's like having a 24/7 health monitor for your machines. You can set up alerts to notify you when something goes outside the normal range, giving you time to react and prevent a breakdown. This proactive approach can save you a ton of money and downtime in the long run. For example, you can use vibration analysis to monitor the state of your equipment.
Use Maintenance Tracking Software
Trying to keep track of maintenance schedules and repairs with spreadsheets? There's a better way! Maintenance tracking software can streamline the whole process. It lets you schedule maintenance tasks, track work orders, manage inventory, and generate reports. This software helps you stay organized and ensures that no maintenance task falls through the cracks. Plus, it gives you a central place to store all your equipment information, making it easy to access when you need it.
Implement Remote Monitoring Solutions
Remote monitoring is especially useful if you have equipment in remote locations or if you want to keep an eye on things outside of normal business hours. With remote monitoring, you can access data and control equipment from anywhere with an internet connection. This can be a huge time-saver and can help you respond quickly to any issues that arise.
Remote monitoring can also reduce the need for on-site visits, saving you travel time and expenses. It's a great way to improve efficiency and keep your equipment running smoothly, no matter where you are.
Establish Clear Maintenance Protocols
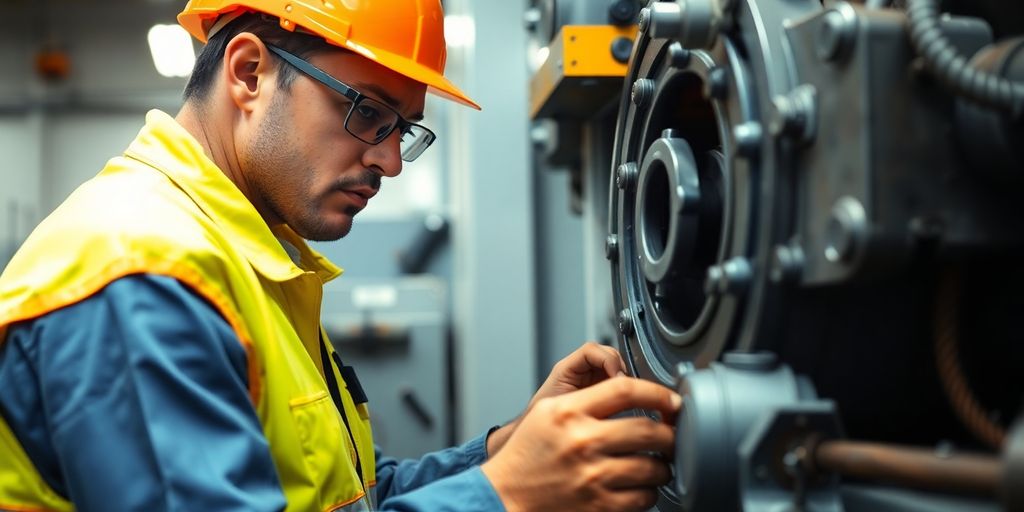
Having well-defined maintenance protocols is super important. It's not just about fixing things when they break; it's about having a system in place to prevent breakdowns in the first place. Clear protocols ensure everyone is on the same page, reducing errors and improving efficiency. It's like having a recipe for keeping your equipment running smoothly.
Document Maintenance Procedures
Make sure you write down everything. Detailed documentation is key. This includes step-by-step instructions for each maintenance task, specifying the tools needed, safety precautions, and expected outcomes. Think of it as a maintenance manual for each piece of equipment. This helps new team members get up to speed quickly and ensures consistency across all shifts. A preventive maintenance schedule is a great start.
Standardize Equipment Checks
Standardization is your friend. Create checklists for routine inspections and maintenance tasks. This ensures that nothing gets missed and that all equipment is checked in the same way, every time. Standardized checks also make it easier to track equipment performance over time and identify potential problems early. It's about creating a consistent baseline for evaluating equipment health.
Create Emergency Response Plans
Stuff happens, right? You need a plan for when things go wrong. Develop emergency response plans for different types of equipment failures. These plans should outline the steps to take to safely shut down the equipment, isolate the problem, and begin repairs. Include contact information for key personnel and external resources. It's like having a fire drill for your equipment.
Having these plans in place minimizes downtime and prevents further damage. It also ensures the safety of your team. It's better to be prepared than to scramble when something breaks down.
Wrapping It Up
In the end, keeping your machinery in good shape is key to avoiding those annoying downtimes that can really hurt your business. By sticking to a solid maintenance plan, training your team well, and using the right tools, you can catch problems before they turn into big headaches. Sure, it takes some effort upfront, but the savings in time and money down the line are totally worth it. So, take a moment to assess your current practices and make those changes. Your operations will run smoother, and you’ll be able to focus on what really matters—growing your business.
Frequently Asked Questions
What is a risk audit and why is it important?
A risk audit checks your equipment to find old machines that might break down. It helps you know what needs to be replaced to keep everything running smoothly.
How can I create a preventive maintenance plan?
To make a preventive maintenance plan, set regular times to check and fix your machines. This way, you can catch problems before they cause breakdowns.
What is predictive maintenance?
Predictive maintenance uses data and tools to predict when a machine might fail. This helps you fix it before it breaks down.
Why is training my maintenance team important?
Training helps your team know how to take care of machines properly. It ensures they can fix issues quickly and safely, reducing downtime.
How can I calculate the costs of downtime?
To find out how much downtime costs, look at lost production, labor hours, and other expenses. This information can help you make better maintenance decisions.
What technology can help with maintenance?
Using technology like maintenance tracking software can help you keep track of repairs and schedule maintenance. This makes it easier to manage your equipment.