How to Maximize Productivity with the Right Machinery: A Comprehensive Guide
.png)
Getting the right machinery can really up your productivity game. It's not just about buying the latest tech, but knowing what fits your needs best. We'll walk you through understanding your operations and making smart choices about machinery. From picking the right tools to using new tech and cutting down on downtime, this guide covers it all. Let's get started on how to maximize productivity with the right machinery.
Key Takeaways
- Understand your daily operations to choose machinery that fits.
- Explore different machine options to find what suits your needs.
- Use technology to simplify setups and boost efficiency.
- Train operators well to maximize machinery usage.
- Keep track of performance data to make informed decisions.
Understanding Your Operational Needs
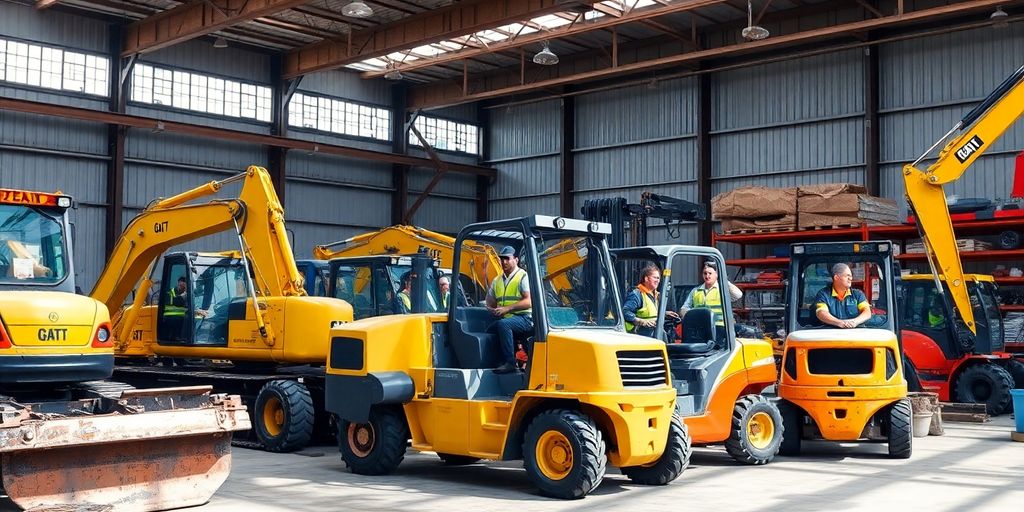
To get the most out of your machinery, you first need to understand what your daily operations require. This isn't just about knowing what machines you have but really digging into how they fit into your day-to-day tasks. Let's break it down:
Analyzing Daily Operations
Start by taking a good look at your daily routine. What are the tasks that keep your business running? Make a list of these tasks and note how each one contributes to your overall goals. This step is all about identifying where your strengths lie and where you might need a bit of help.
Utilizing Key Product Matrix
Once you have a handle on your operations, it's time to bring in some structure. The Key Product Matrix is a handy tool for this. It helps you map out which products or machines are crucial to your operations and which ones aren't pulling their weight. Think of it like a scorecard for your equipment.
Optimizing for Primary Workload
With your operations analyzed and your Key Product Matrix in hand, you can start optimizing. This means tweaking your processes and possibly even rearranging your workspace to make sure the most important tasks get done as efficiently as possible. It's about making sure every piece of equipment is used to its fullest potential, enhancing productivity and profitability in your operations.
Understanding your operational needs isn't just a one-time thing. It's an ongoing process that can help you adapt and grow as your business evolves.
Choosing the Right Machinery for Your Needs
Exploring Machine Options
When it comes to picking the right machinery, the first step is to know what you're dealing with. Consider your specific production needs and how different machines can meet them. Understanding your production requirements is key. You need to evaluate what kind of tasks your machinery needs to handle and how often. This isn't just about the present, but also about future needs. Think about how your choices today will affect your operations down the line.
- Identify the core tasks and operations your machinery must perform.
- Consider the scale of production and potential expansion.
- Evaluate the technology integrations required for your operations.
Engaging with Clients for Tailored Solutions
Working closely with clients is crucial to tailor machinery solutions that fit like a glove. This isn't just about selling a machine; it's about understanding the unique challenges and goals of each client. By engaging clients in the selection process, you can ensure that the machinery you choose aligns perfectly with their needs.
- Conduct detailed discussions to understand client needs and expectations.
- Offer demonstrations and trials to showcase how different machines can meet these needs.
- Gather feedback and adjust recommendations accordingly.
Crafting Customized Solutions
Customization is where the magic happens. It’s about tweaking and adjusting machinery to suit specific tasks and environments. This could mean modifying existing machines or even designing new components. The goal is to enhance productivity and efficiency by ensuring that the equipment is perfectly suited to its operational context.
Custom solutions are not just about having the best machinery; they are about having the right machinery for the job. This approach ensures flexibility and efficiency, allowing for a variety of tasks to be handled with ease.
In choosing the right machinery, remember that it’s not just about the machine itself, but about how it fits into your broader operational strategy. Consider specific production requirements, financial impacts, and future needs to make informed decisions.
Implementing Advanced Technologies
Simplifying Setups with Technology
Getting your machinery up and running doesn't have to be a headache. With the right tech, setting up can be a breeze. Think about using automated industrial machinery that integrates advanced control systems and AI technology. This improves manufacturing efficiency by streamlining processes and reducing manual intervention. Here’s a simple approach:
- Use smart sensors to monitor setup parameters in real-time.
- Implement software that automates the calibration of your machines.
- Regularly update your systems to incorporate the latest technological advancements.
By simplifying setups, you can minimize errors and reduce downtime.
Automating Tasks for Efficiency
Automation is key when it comes to making things run smoothly. With automation, repetitive tasks that once ate up hours of your day can now be done in minutes. Here’s how you can bring automation into your operations:
- Identify tasks that are repetitive and time-consuming.
- Choose automation tools or software that fit these tasks.
- Train your team to work alongside these automated systems.
The result? More consistent outputs and a workforce that can focus on more complex, value-adding activities.
Boosting Machine Speeds
Who doesn’t want their machines to work faster? Boosting machine speeds can significantly increase your output without needing additional resources. Here are some tips:
- Regularly maintain and service your machinery to ensure it runs at peak performance.
- Use high-quality parts and components that can withstand higher speeds.
- Optimize your production process to eliminate bottlenecks that slow down operations.
By focusing on speed, you can increase productivity and keep up with demand without compromising on quality.
Optimizing Machinery Usage
Matching Equipment to Task Requirements
To get the best performance out of your machinery, it's important to match the right equipment to the specific task at hand. This means understanding the capabilities of your machines and aligning them with the job requirements. Selecting the right equipment not only boosts productivity but also reduces wear and tear. For instance, using a bulldozer for light-duty tasks can lead to unnecessary fuel consumption and increased maintenance costs.
- Evaluate the task requirements thoroughly.
- Choose equipment that meets or exceeds these requirements.
- Consider the long-term operational costs when selecting machinery.
Training Operators for Efficiency
The efficiency of machinery usage heavily depends on the skill and knowledge of the operators. Investing in comprehensive training programs ensures that operators are well-versed in the latest techniques and safety protocols. This not only improves efficiency but also reduces the likelihood of accidents and equipment misuse.
- Conduct regular training sessions.
- Update training materials to include new technologies and methods.
- Encourage operators to provide feedback on equipment performance.
Implementing Site Layout Plans
A well-thought-out site layout can significantly reduce machinery travel distances and idle time. By organizing the site to minimize unnecessary movement, you can enhance operational efficiency and reduce fuel costs. This involves strategic placement of materials, equipment, and personnel to streamline workflows.
- Design a layout that minimizes travel distances.
- Place frequently used equipment and materials in easily accessible locations.
- Regularly review and adjust the layout to accommodate changes in operations.
Implementing these strategies can lead to substantial improvements in productivity and cost savings. By focusing on matching equipment to tasks, training operators, and optimizing site layouts, businesses can maximize the utility of their machinery and ensure smoother operations.
Monitoring Performance and Making Data-Driven Decisions
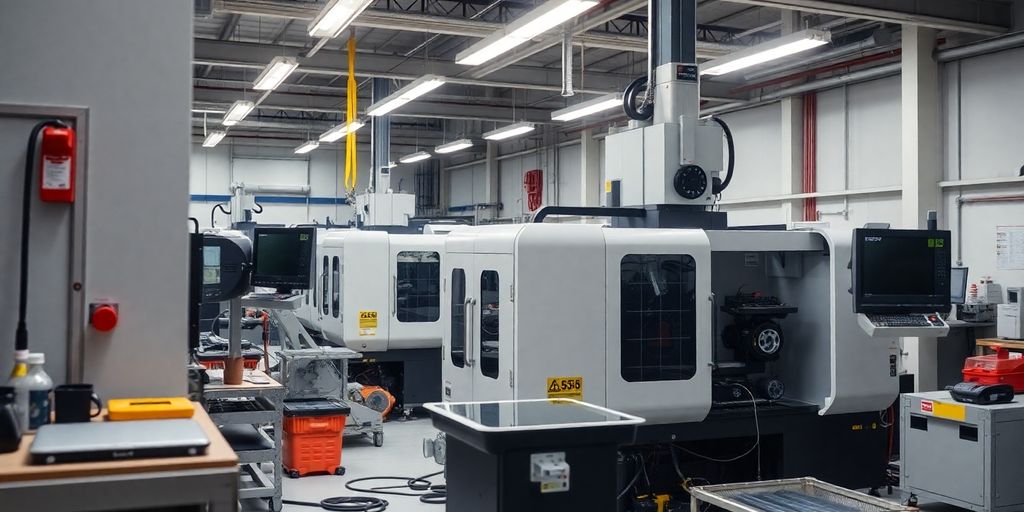
In the world of manufacturing, keeping a close eye on performance metrics is like having a secret weapon. By leveraging data-driven decision-making, companies can boost efficiency, cut costs, and improve product quality. This not only enhances performance but also leads to better profitability.
Tracking Productivity KPIs
To get started, it's essential to track key performance indicators (KPIs) that matter to your operations. These KPIs can include machine uptime, production rates, and defect rates. By regularly monitoring these metrics, manufacturers can identify bottlenecks and inefficiencies. This allows for targeted improvements, leading to cost savings and increased output.
Utilizing Predictive Maintenance Technologies
Predictive maintenance is a game-changer in reducing downtime. By using advanced technologies like predictive analytics, manufacturers can foresee equipment failures before they happen. This proactive approach not only extends machinery life but also optimizes maintenance schedules, ensuring that machines are serviced only when needed.
Benchmarking Performance Across Assets
Benchmarking is another powerful tool in the arsenal. By comparing performance across different machines, shifts, or even plants, companies can identify best practices and areas for improvement. This internal and external benchmarking helps set realistic targets and drives continuous improvement.
Embracing data and automation in manufacturing not only boosts quality control but also maximizes output, helping companies thrive in a competitive landscape.
For those looking to dive deeper into data-driven decision-making in manufacturing, the benefits are clear: enhanced efficiency, reduced costs, and improved product quality. It's all about making smarter, informed decisions that lead to better performance and profitability.
Enhancing Efficiency Through Automation
Automating Data Collection
Automating data collection is a game-changer. It cuts out the errors that come with manual data entry and saves time. By using automated systems, you get accurate, real-time data that paints a clear picture of what's happening on the production floor. This data helps in spotting trends and making informed decisions.
Leveraging AI for Predictive Insights
Artificial intelligence isn't just for tech geeks. It's transforming how we work by providing predictive insights that help in planning and decision-making. Integrating artificial intelligence and machine learning into industrial automation means systems can adapt and improve continuously, boosting efficiency. AI helps in identifying potential issues before they become problems, saving time and resources.
Standardizing Processes for Consistency
Consistency is key in manufacturing. By standardizing processes, you ensure that every operation follows the same steps, reducing variability and errors. This not only makes the workflow smoother but also increases productivity. Standardized processes mean less downtime and more consistent output, which is a win-win for any operation.
Automation isn't just about replacing human tasks with machines; it's about making those tasks more efficient and freeing up human resources for more strategic roles. With automation, you can focus on what truly matters and let the machines handle the repetitive tasks.
Reducing Idle Time and Wear
Using Equipment Tracking Software
Idle machinery is like money sitting on the table—it's not doing you any good. Equipment tracking software can be a game-changer. By keeping an eye on where your machines are and how they're being used, you can cut down on unnecessary downtime. This tech lets you see real-time data, so if a machine is just sitting there, you know about it and can make adjustments. Plus, it helps in planning and optimizing routes, which means less time wasted moving machines around.
- Track machine location and usage in real-time.
- Optimize equipment deployment based on current needs.
- Identify underutilized assets and reassign them to where they're needed most.
Implementing Just-in-Time Delivery Systems
Ever had a project stall because the materials weren't there on time? Just-in-time (JIT) delivery systems can help with that. By syncing material delivery with your schedule, you ensure everything arrives when you need it, not before or after. This reduces the time your machinery sits idle waiting for supplies.
- Schedule deliveries to match project timelines.
- Reduce storage costs and minimize clutter on site.
- Improve workflow by having materials ready when needed.
Adopting Wear-Resistant Materials
Machinery wear and tear is unavoidable, but you can slow it down. Using wear-resistant materials in key parts of your machines can extend their lifespan. This means fewer breakdowns and less time spent on repairs, keeping your projects on track.
- Select materials designed to withstand harsh conditions.
- Regularly inspect and replace worn parts to prevent failures.
- Consider coatings or treatments that enhance durability.
Regularly reviewing schedules and adjusting based on asset performance data can help minimize idle time, enhancing material flow and supply chain coordination. Learn more about optimizing schedules.
Conclusion
So there you have it, folks. Getting the most out of your machinery isn't just about having the latest gadgets or the fanciest tools. It's about understanding what you really need, how your operations tick, and making smart choices based on that. By focusing on the right equipment and keeping an eye on how it's used, you can really boost productivity. Remember, it's not just about working harder, but working smarter. And with the right approach, you'll see improvements not just in output, but in efficiency and even cost savings. So, take a step back, assess your needs, and make those machines work for you. It's all about finding that sweet spot where everything clicks and your operations run like a well-oiled machine.
Frequently Asked Questions
Why is it important to understand our daily operations?
Understanding daily operations helps identify areas for improvement and ensures that the right machinery is used to enhance productivity.
What is a Key Product Matrix?
A Key Product Matrix is a tool used to gather detailed information about products, helping to tailor solutions to specific operational needs.
How do advanced technologies boost productivity?
Advanced technologies simplify setups, automate tasks, and increase machine speeds, which helps improve overall efficiency.
What is predictive maintenance?
Predictive maintenance involves using technology to predict when equipment might fail, allowing for timely repairs and reducing downtime.
How can automation enhance efficiency?
Automation streamlines processes, reduces human error, and allows for faster data collection, leading to more consistent and efficient operations.
What are some ways to reduce equipment idle time?
Using tracking software, implementing just-in-time delivery systems, and choosing wear-resistant materials can help reduce idle time and wear.