How to Make Your Heavy Machinery Fleet More Energy-Efficient
.png)
Running a heavy machinery fleet can be quite costly, especially when it comes to fuel expenses. However, there are plenty of ways to improve energy efficiency and keep those costs in check. By focusing on maintenance, training, and the right technology, you can make a real difference in how your machinery performs. Here’s a look at some practical tips to help you save energy and boost efficiency in your operations.
Key Takeaways
- Regular maintenance is key to keeping your machinery running efficiently and saving on fuel.
- Training your operators on best practices can lead to significant fuel savings.
- Upgrading to newer, energy-efficient models can reduce operational costs and environmental impact.
- Using technology like telematics can help monitor performance and identify areas for improvement.
- Choosing the right equipment for each job can prevent unnecessary fuel waste and enhance productivity.
Regular Maintenance and Inspections to Enhance Efficiency
It's easy to overlook regular maintenance when you're busy, but trust me, it's worth it. Think of it like this: a little bit of attention now can save you from huge headaches (and expenses) later. We're talking about keeping your heavy machinery in top shape, which directly translates to better energy efficiency and a longer lifespan.
Importance of Routine Maintenance
Routine maintenance is the backbone of a well-oiled machine fleet. It's not just about fixing things when they break; it's about preventing them from breaking in the first place. Think of it as preventative care for your equipment. By staying on top of things like scheduled service, you're nipping potential problems in the bud before they turn into major disasters. This means less downtime, fewer unexpected repairs, and ultimately, more money in your pocket. Learn more about regular maintenance.
Skipping maintenance to save time is like skipping breakfast to lose weight – it might seem like a good idea in the short term, but it'll catch up with you eventually.
Here's a quick list of things to keep an eye on:
- Engine health: Keep it clean and tuned.
- Filters: Air and fuel filters need regular checks and replacements.
- Hydraulics: Inspect those hoses and fluid levels.
- Tires: Proper inflation is key, and watch out for wear.
Scheduling Regular Inspections
Okay, so you know maintenance is important, but how do you actually make it happen? That's where scheduling regular inspections comes in. Don't just wait for something to go wrong; proactively check your equipment on a consistent basis. This could be daily, weekly, or monthly, depending on the type of machinery and how often you're using it.
Here's a simple way to think about it:
- Create a checklist: List all the key components that need to be inspected.
- Set a schedule: Determine how often each item needs to be checked.
- Assign responsibility: Make sure someone is in charge of performing the inspections.
Identifying Early Signs of Wear
Knowing what to look for is half the battle. It's not enough to just glance at your equipment and say, "Looks good!" You need to train yourself (or your team) to spot the early signs of wear and tear. This could be anything from a small leak to a strange noise to a decrease in performance. Early detection is key.
Here are some things to watch out for:
- Unusual noises or vibrations
- Leaks (oil, coolant, hydraulic fluid)
- Decreased power or fuel efficiency
- Visible damage (cracks, dents, rust)
Upgrading to Energy-Efficient Models
Okay, so your heavy machinery is getting a little old? It might be time to think about upgrading. It's a big decision, sure, but the payoff in the long run can be huge. We're talking lower costs, less environmental impact, and just overall better performance. Let's break it down.
Evaluating Current Equipment Performance
First things first, you gotta know where you stand. How's your current equipment really doing? Are you pouring money into repairs every other week? Is the fuel consumption through the roof? Take a hard look at the numbers. Track fuel usage, maintenance costs, and downtime. If you see a pattern of increasing expenses and decreasing productivity, that's a major red flag. Don't just guess; get the data. This will help you make a solid case for upgrading.
Benefits of Modern Machinery
Modern machinery isn't just about looking shiny and new. It's packed with features designed to save you money and reduce your environmental footprint. Think about it: newer engines are way more fuel-efficient. They often come with eco modes and automatic shutdowns that cut down on wasted energy. Plus, they're built with better materials and technology, meaning they'll likely last longer and require less maintenance. See the top energy-efficient industrial machines for 2024.
Here's a quick rundown:
- Lower operating costs due to less fuel consumption.
- Reduced environmental impact with lower emissions.
- Improved productivity with advanced tech.
- Longer equipment lifespan with less wear and tear.
- Compliance with environmental rules.
Signs It's Time to Upgrade
So, how do you know it's time to bite the bullet and upgrade? Here are a few telltale signs:
- Excessive fuel consumption: If your machines are guzzling fuel like there's no tomorrow, that's a big problem.
- Frequent breakdowns: Constant repairs are a drain on your wallet and your time.
- Decreased productivity: If your equipment is struggling to keep up with demand, it's time for a change.
- Outdated technology: Older models may lack the energy-efficient features of modern machines.
- Increasing maintenance costs: If you're spending more and more on repairs, it's a sign that your equipment is nearing the end of its life.
Upgrading your heavy machinery isn't just an expense; it's an investment. By carefully evaluating your current equipment, understanding the benefits of modern machinery, and recognizing the signs that it's time to upgrade, you can make a smart decision that will pay off in the long run.
Implementing Technology and Automation for Efficiency
Technology and automation are changing how we manage heavy machinery. It's not just about having fancy gadgets; it's about using them to make smarter decisions and get more out of your equipment. Let's explore how to make it happen.
Utilizing Telematics Systems
Telematics systems can really change the game. They give you real-time data on how your machines are doing. Think of it as having a constant checkup on your equipment. Telematics systems provide managers and operators with insights that help increase fuel efficiency, set servicing reminders and prevent costly repairs. More importantly, telematics helps reduce human error. For example, you can track equipment idle time and see if machines are running longer than they should be. This helps you make changes to improve efficiency.
Real-Time Data Monitoring
With telematics, you can monitor things like fuel consumption, engine performance, and how long equipment is used each day. Real-time data helps you spot problems early and make quick adjustments. It's like having a dashboard that shows you exactly what's going on with your fleet.
By keeping an eye on this data, you can make sure your equipment is running at its best and avoid costly breakdowns.
Automated Maintenance Scheduling
Telematics systems can also help you schedule maintenance automatically. Instead of guessing when a machine needs servicing, the system can track usage and alert you when it's time for maintenance. This ensures timely servicing by requiring less maintenance. Here's how it helps:
- Reduces downtime by scheduling maintenance proactively.
- Extends the life of your equipment by keeping it in good condition.
- Saves money by preventing major repairs.
It's a simple way to keep your fleet running smoothly and efficiently.
Operator Training and Best Practices
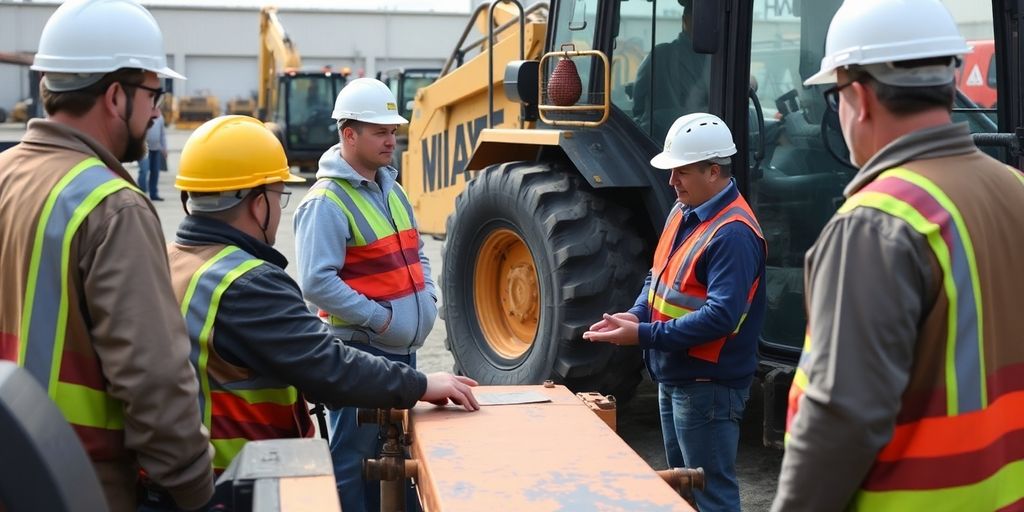
It's easy to overlook operator training, but it's a huge deal for energy efficiency. You can have the fanciest, most modern equipment, but if the person running it doesn't know what they're doing, you're throwing money away. Let's get into how to make sure your operators are part of the solution, not the problem.
Techniques for Fuel Efficiency
Training operators in fuel-efficient techniques is a game-changer. It's not just about saving money; it's about reducing your environmental impact and extending the life of your equipment. Here are some things to keep in mind:
- Limit idle time: Turn off engines when not in use. It sounds simple, but it adds up.
- Smooth operation: Avoid rapid acceleration and harsh braking. It wastes fuel and puts unnecessary stress on the machine.
- Consistent speed: Keeping a steady pace reduces unnecessary fuel consumption. Think of it like cruise control in your car.
- Proper route planning: Plan routes to minimize travel distance and avoid congested areas.
Creating a Fuel-Smart Culture
It's not enough to just tell operators what to do; you need to create a culture where fuel efficiency is valued and encouraged. Here's how:
- Lead by example: Show that management is committed to fuel efficiency.
- Provide incentives: Reward operators who consistently demonstrate fuel-efficient practices.
- Share data: Make fuel consumption data transparent so operators can see how they're performing.
- Encourage feedback: Ask operators for their ideas on how to improve fuel efficiency. They're the ones in the field, after all.
Creating a fuel-smart culture is about more than just saving money. It's about creating a sense of ownership and responsibility among your operators. When they feel like they're part of a team working towards a common goal, they're more likely to be engaged and motivated.
Evaluating Operator Performance
How do you know if your training is working? You need to track and evaluate operator performance. Safe equipment operation is key. Here are some ways to do that:
- Track fuel consumption: Monitor fuel usage per operator and per machine.
- Use telematics data: Telematics systems can provide detailed data on operator behavior, such as idle time, speed, and braking habits.
- Conduct regular performance reviews: Discuss fuel efficiency with operators during performance reviews.
- Provide ongoing training: Offer refresher courses and advanced training to keep operators up-to-date on the latest fuel-efficient techniques.
By implementing these strategies, you can transform your operators into fuel-saving machines and significantly reduce your operating costs.
Optimizing Equipment Usage and Selection
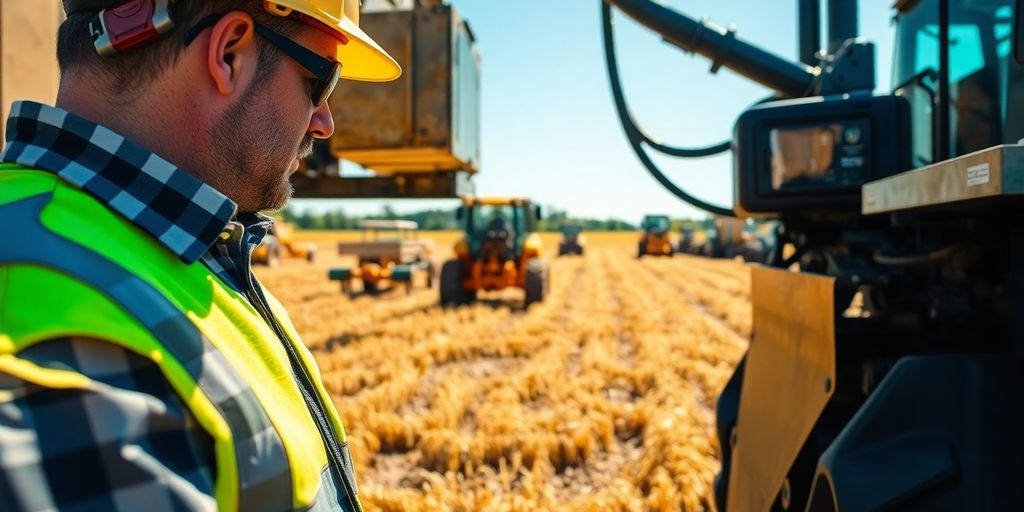
It's easy to overlook how much the right equipment impacts efficiency. You might think, "A machine is a machine," but that's not true. Getting the most out of your fleet means thinking strategically about what you're using and how you're using it. It's not just about having the biggest or newest machines; it's about having the appropriate machines and using them in the most effective way.
Choosing the Right Equipment for the Job
Picking the right equipment isn't just about getting the job done; it's about getting it done efficiently. Matching the equipment size to the task is crucial. Using a massive excavator for a small job is a waste of fuel. Similarly, a tiny machine won't cut it for heavy-duty work, and you'll end up running it longer, which also wastes fuel. Think about the specific needs of your site and choose accordingly. It's about balance.
Matching Equipment to Project Needs
Think of your equipment like tools in a toolbox. You wouldn't use a hammer to screw in a screw, right? The same logic applies to heavy machinery. Consider the project requirements. Is it a demolition job? A landscaping project? A road construction task? Each requires different equipment. Don't just grab the first machine you see. Take a moment to assess the project and select the equipment that's best suited for the job. This will save you time, fuel, and wear and tear on your machines. You can also look into energy-efficient optimization method.
Utilizing Attachments Effectively
Attachments can significantly expand the capabilities of your existing equipment. Instead of buying a whole new machine for a specific task, consider whether an attachment could do the job. For example, a skid steer with a brush cutter attachment can clear vegetation just as effectively as a dedicated brush clearing machine. Using attachments effectively can reduce the number of machines you need on-site, which translates to lower fuel consumption and reduced operating costs.
Think about attachments as force multipliers. They allow you to get more done with less, which is the name of the game when it comes to energy efficiency.
Here are some ways to make sure you're using attachments effectively:
- Ensure operators are properly trained on how to use each attachment.
- Regularly inspect attachments for wear and tear.
- Choose the right attachment for the specific task at hand.
Adopting Energy-Efficient Technologies
Okay, so you're thinking about making your heavy machinery more efficient? Smart move. It's not just about being green; it's about saving some serious cash in the long run. Let's talk tech.
Benefits of Modern Equipment Features
Switching to newer machines can really change things. Modern equipment is designed to use less energy while doing the same amount of work. Think about it: better motors, smarter designs, and less wasted power. Plus, newer stuff often needs less fixing, which is always a win. For example, upgrading to advanced motor technology can significantly lower energy usage. Not only do these machines save energy, but they also tend to be more reliable and require less maintenance. electric and hydrogen-powered equipment is becoming more common.
Utilizing Eco Modes and Automatic Shutdowns
Most new machines come with eco modes. These modes adjust the machine's power based on what it's doing. If it's not working hard, it uses less power. Simple as that. Automatic shutdowns are great too. If a machine is sitting idle, it'll just turn itself off. No wasted energy. It's like having a smart thermostat for your bulldozer.
Investing in Advanced Motor Technology
Think about the motors in your machines. Are they old and inefficient? Upgrading to something newer, like an IE3 or IE4 motor, can make a huge difference. These motors are designed to waste less energy, which means more power for the job and less money spent on fuel. It's an investment that pays off over time.
Upgrading to energy-efficient technologies isn't just about saving money. It's about making a commitment to a more sustainable way of doing things. As energy costs keep going up, these changes will become more and more important for staying competitive.
Monitoring and Analyzing Fuel Consumption
Tracking Fuel Usage Patterns
Okay, so you're trying to get a handle on fuel consumption? The first step is actually tracking it. I mean, you can't fix what you don't measure, right? Start by recording how much fuel each piece of equipment uses, and when. Keep it consistent. Are you using spreadsheets? A dedicated software? Doesn't matter, just get the data down. This will give you a baseline to work from. I've found it's helpful to break it down by machine, by operator, and by type of job. You'll start to see patterns emerge, trust me.
Identifying Inefficiencies
Once you've got some data, it's time to play detective. Look for the outliers. Which machines are guzzling more fuel than others for the same tasks? Which operators seem to burn through fuel faster? Is there a particular job site where fuel consumption is always high? These are the questions you need to ask. Maybe a machine needs maintenance, or an operator needs more training. Or maybe the job itself is just inherently inefficient. Whatever it is, you won't know until you dig into the numbers. Telematics systems can be a huge help here, giving you real-time data and alerts.
Implementing Corrective Actions
Okay, you've found the problems. Now what? Time to fix them! This is where things get interesting. Maybe you need to schedule some maintenance on that gas-guzzling excavator. Or maybe you need to retrain that operator who's idling too much. Or maybe you need to rethink the way you're doing things on that one job site. Whatever it is, make a plan, implement it, and then track the results. Did your changes actually make a difference? If not, go back to the drawing board. It's all about continuous improvement.
It's important to remember that fuel efficiency isn't just about saving money. It's also about reducing your environmental impact. By tracking your fuel consumption and implementing corrective actions, you're not just improving your bottom line, you're also doing your part to protect the planet.
Wrapping It Up
At the end of the day, making your heavy machinery fleet more energy-efficient is about more than just saving a few bucks. It’s also about doing your part for the planet. By keeping up with regular maintenance, choosing the right machines, and training your operators to be smart about fuel use, you can really stretch your budget. Plus, using tech like telematics can help you catch any fuel waste before it becomes a bigger problem. It’s all about those little changes that can lead to big savings. Whether you’re in construction, mining, or any field that relies on heavy machinery, these tips can help you run things smoother and keep costs down. Remember, every bit counts, and over time, these efforts can lead to a more sustainable and cost-effective operation.
Frequently Asked Questions
Why is routine maintenance important for heavy machinery?
Routine maintenance helps machines run better, saves fuel, and prevents big problems before they happen.
How does operator training help with fuel efficiency?
When operators learn the best ways to use machines, they can save fuel by avoiding wasteful habits like letting machines idle too long.
What are the advantages of using telematics systems?
Telematics systems track how machines are used, showing where improvements can be made to save fuel and cut costs.
How does selecting the right equipment affect fuel use?
Using the correct size and type of equipment for each job helps avoid wasting fuel and ensures the machine works efficiently.
What are some examples of energy-efficient technologies in heavy machinery?
These include features like eco modes and automatic shutdowns that help machines use less fuel and operate more efficiently.
Why is it important to use high-quality fuel for machinery?
High-quality fuel keeps engines clean and running smoothly, which helps save fuel and reduces the need for repairs.