How to Increase Productivity with the Right Industrial Equipment
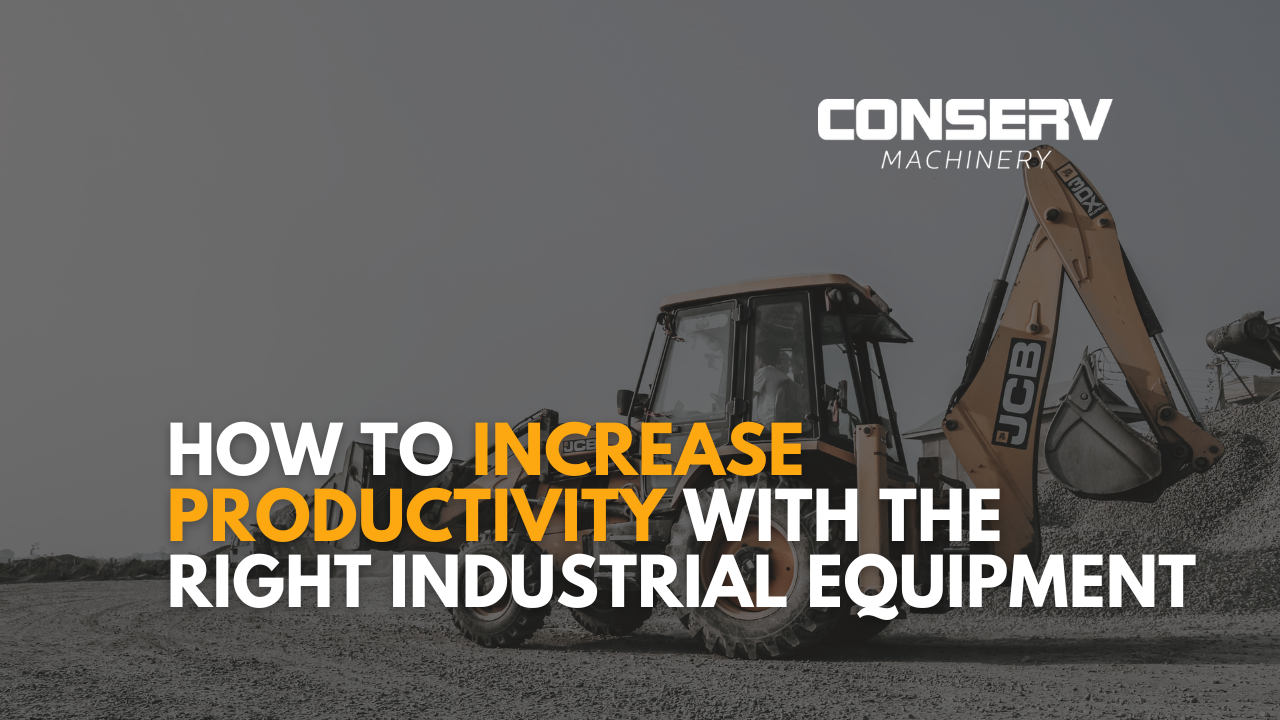
How to Increase Productivity with the Right Industrial Equipment
In today's fast-paced industrial landscape, choosing the right equipment is crucial for boosting productivity. This article explores how the right tools can streamline operations, enhance efficiency, and ultimately lead to greater success in your business. By understanding the importance of industrial equipment and implementing effective strategies, you can significantly improve your productivity levels.
Key Takeaways
- Selecting the right industrial equipment is essential for improving workflow and productivity.
- Investing in employee training ensures that workers can effectively use new tools and technologies.
- Regular maintenance of equipment helps prevent downtime and prolongs the lifespan of machines.
- Utilizing technology, such as automation and data analytics, can greatly enhance operational efficiency.
- Safety training and compliance are vital to maintaining a productive and safe work environment.
Understanding the Role of Industrial Equipment in Productivity
Industrial equipment plays a crucial role in enhancing productivity within manufacturing environments. Choosing the right equipment can significantly boost efficiency and streamline operations. Here’s how:
The Importance of Choosing the Right Equipment
- Selecting equipment that fits your specific needs can lead to:
- Faster production times
- Reduced operational costs
- Improved product quality
How Equipment Impacts Workflow Efficiency
The right tools can transform workflows by:
- Minimizing downtime through reliable machinery.
- Enhancing employee performance with user-friendly designs.
- Allowing for better resource management.
Case Studies of Successful Equipment Implementation
Many companies have seen remarkable improvements after upgrading their equipment. For instance:
- A manufacturing firm increased output by 30% after investing in automated systems.
- Another company reduced waste by 25% through better machinery.
Investing in modern equipment not only enhances productivity but also ensures that your operations remain competitive in a fast-paced market.
In conclusion, understanding the role of industrial equipment is essential for any business aiming to improve productivity. By focusing on the right tools, companies can achieve significant gains in efficiency and effectiveness.
Key Factors in Selecting Industrial Equipment
Assessing Your Operational Needs
When choosing industrial equipment, it’s crucial to understand your specific needs. This includes:
- Analyzing the type of work you do.
- Considering the size and scale of your operations.
- Evaluating the environment where the equipment will be used.
Evaluating Equipment Features and Benefits
Not all equipment is created equal. Here are some features to look for:
- Durability: Ensure the equipment can withstand your work conditions.
- Efficiency: Look for machines that save time and energy.
- Ease of Use: Equipment should be user-friendly to minimize training time.
Considering Long-term Maintenance and Support
Maintenance is key to keeping equipment running smoothly. Consider:
- The availability of spare parts.
- The cost of regular maintenance.
- The support services offered by the manufacturer.
Regular maintenance not only extends the life of your equipment but also ensures that it operates at peak performance, reducing unexpected downtime.
By focusing on these key factors, you can make informed decisions that enhance productivity and efficiency in your operations.
Training and Skill Development for Optimal Equipment Use
Importance of Employee Training Programs
Employee training is essential for maximizing productivity. Regular training ensures that workers are skilled and safe. Here are some key points to consider:
- Training should cover both basic and advanced equipment operations.
- Safety protocols must be included to prevent accidents.
- Continuous training helps employees adapt to new technologies.
Integrating New Equipment with Existing Processes
When new equipment is introduced, it’s crucial to integrate it smoothly into current workflows. This can be achieved by:
- Assessing how the new equipment fits into existing operations.
- Providing hands-on training sessions for employees.
- Encouraging feedback from operators to improve integration.
Continuous Learning and Skill Enhancement
To keep up with industry changes, ongoing education is vital. Here are some strategies:
- Offer specialized courses on advanced topics like electrical systems and HVAC systems.
- Create a culture of learning where employees can share knowledge.
- Use online resources for self-paced learning opportunities.
Investing in employee training not only boosts productivity but also enhances job satisfaction and retention rates.
Leveraging Technology for Enhanced Productivity
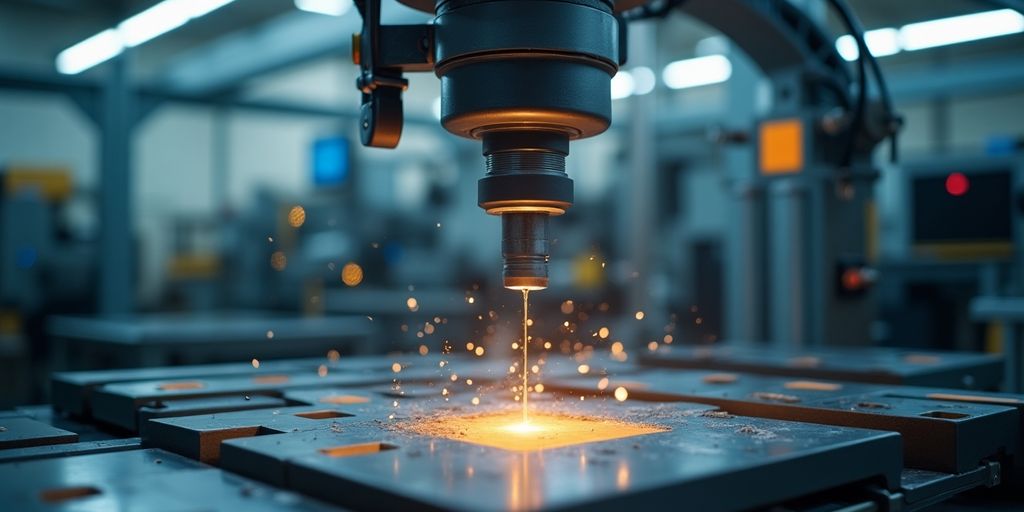
The Role of Automation in Industrial Settings
Automation is a game changer in the industrial world. Companies that strategically leverage technology tools for productivity see a 25% increase in overall operational efficiency. By using automated systems, businesses can:
- Reduce human error
- Speed up production processes
- Improve product quality
Utilizing Data Analytics for Performance Improvement
Data analytics helps companies understand their operations better. By analyzing data, businesses can:
- Identify areas for improvement
- Track performance metrics
- Make informed decisions based on real-time data
Adopting Cutting-edge Technologies
Investing in the latest technologies can lead to significant productivity gains. Some benefits include:
- Enhanced safety features that protect workers
- Faster production times that meet market demands
- The ability to innovate and stay competitive in the market
Investing in technology not only boosts productivity but also creates a safer and more efficient workplace.
Maintaining and Upgrading Equipment for Sustained Productivity
Regular Maintenance Schedules and Practices
To keep your equipment running smoothly, it’s essential to follow a regular maintenance schedule. This helps prevent unexpected breakdowns and keeps your machines in good shape. Here are some key practices:
- Inspect equipment before and after each use for any signs of damage.
- Follow the manufacturer’s guidelines for maintenance intervals.
- Train operators on basic maintenance tasks to ensure they can spot issues early.
Identifying Signs for Equipment Upgrades
Knowing when to upgrade your equipment can save time and money. Look for these signs:
- Frequent breakdowns that disrupt work.
- Increased repair costs that exceed the value of the equipment.
- Inability to meet production demands due to outdated technology.
Balancing Cost and Benefits of New Investments
When considering new equipment, it’s important to weigh the costs against the benefits. Here’s how:
- Calculate potential productivity gains from new equipment.
- Consider long-term savings on repairs and maintenance.
- Evaluate the return on investment (ROI) to ensure it aligns with your business goals.
Regular maintenance and timely upgrades are crucial for keeping your operations efficient and productive. By staying proactive, you can avoid costly downtime and ensure your equipment meets your needs.
In summary, maintaining and upgrading your equipment is vital for sustained productivity. By following a structured maintenance plan, recognizing when upgrades are necessary, and balancing costs with benefits, you can keep your operations running smoothly and efficiently. Remember, equipment maintenance 101: what you need to know is essential for long-term success.
Safety and Compliance in Equipment Usage
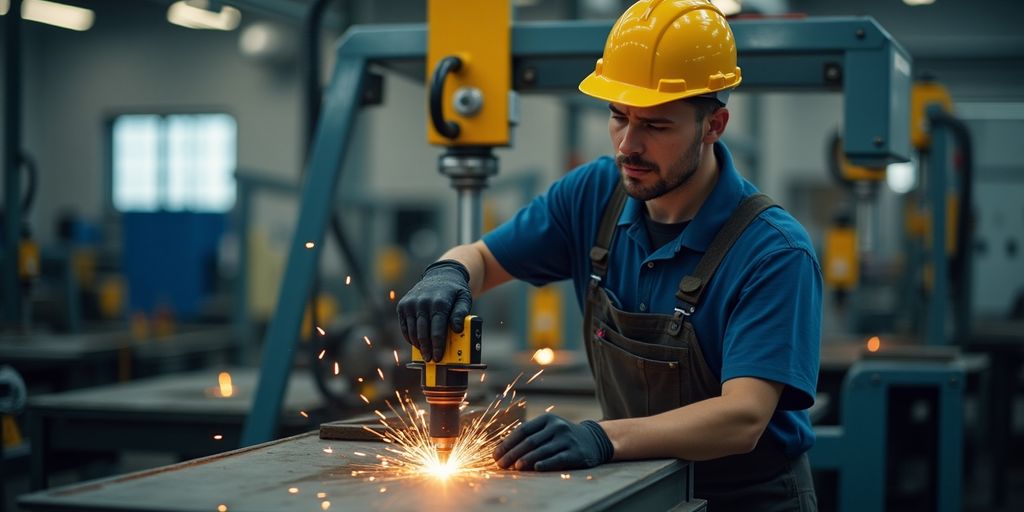
Ensuring Workplace Safety with Modern Equipment
Safety is crucial in any industrial setting. Using modern equipment can significantly enhance workplace safety. Here are some key points to consider:
- Regularly inspect equipment for any signs of wear or damage.
- Ensure all operators are trained in safety protocols.
- Use safety gear and equipment that meet regulatory standards.
Understanding Regulatory Compliance Requirements
Compliance with safety regulations is not just a legal obligation; it’s essential for protecting your workforce. Here are some important regulations to keep in mind:
- Follow OSHA guidelines to ensure a safe working environment.
- Maintain proper documentation of safety training and equipment inspections.
- Stay updated on changes in safety regulations that may affect your operations.
Implementing Safety Training and Protocols
Training is vital for maintaining safety standards. Here’s how to implement effective safety training:
- Schedule regular training sessions for all employees.
- Use real-life scenarios to teach safety protocols.
- Encourage feedback from employees about safety practices.
Regular training and adherence to safety protocols can prevent accidents and ensure a productive work environment.
By focusing on safety and compliance, companies can protect their workers and avoid fines, ensuring a more productive and efficient workplace. Investing in safety measures is investing in productivity.
Measuring and Analyzing Productivity Gains
Setting Key Performance Indicators (KPIs)
To effectively measure productivity, it’s essential to establish Key Performance Indicators (KPIs). These are specific metrics that help you track progress and performance. Here are some common KPIs:
- Output per hour: Measures how much product is made in a given time.
- Downtime: Tracks how often machines are not in use.
- Quality rates: Assesses the number of products that meet quality standards.
Using Software Tools for Productivity Tracking
Utilizing software tools can greatly enhance your ability to monitor productivity. These tools can:
- Provide real-time data on machine performance.
- Help identify trends and patterns in production.
- Allow for easy reporting and analysis of productivity metrics.
Interpreting Data to Drive Continuous Improvement
Once you have collected data, the next step is to analyze it. This can help you understand where improvements can be made. Consider the following:
- Look for patterns in productivity data to identify bottlenecks.
- Compare current performance against historical data to see progress.
- Use insights to make informed decisions about equipment upgrades or employee training.
Regularly measuring and analyzing productivity is crucial for ongoing success. It helps businesses adapt and thrive in a competitive environment.
Conclusion
In summary, boosting productivity in your industrial operations requires a mix of smart choices and ongoing efforts. Training your employees is key; when they know how to use the equipment well, they work better and safer. Investing in the right tools, not just the most expensive ones, can fill gaps in your processes and help your team perform at their best. Regular maintenance of machines is also crucial to avoid unexpected breakdowns that can slow down work. By focusing on these areas, you can create a more efficient workplace that not only meets production goals but also keeps your team happy and safe.
Frequently Asked Questions
Why is choosing the right industrial equipment important for productivity?
Choosing the right industrial equipment is key because it can help make work easier and faster. The right tools can improve how workers do their jobs and reduce mistakes.
How does equipment affect workflow efficiency?
Good equipment helps workers complete tasks more smoothly. When machines work well, it means less waiting time and more getting done, which boosts overall efficiency.
What should I consider when selecting industrial equipment?
When picking equipment, think about what your business needs, the features that will help you, and how easy it will be to maintain the equipment over time.
Why is employee training important for using new equipment?
Training employees on new tools is important because it helps them use the equipment correctly and safely. This can lead to better productivity and fewer accidents.
How can technology improve productivity in industrial settings?
Technology, like automation and data analysis, can make tasks faster and easier. It helps track performance and find areas that need improvement.
What are the benefits of regular equipment maintenance?
Regular maintenance keeps machines running well and can prevent costly breakdowns. It helps ensure that equipment is safe and efficient, which supports ongoing productivity.