How to Extend the Life of Your Heavy Equipment
.png)
Keeping your heavy equipment in good shape is key to getting the most out of your investment. Regular maintenance and smart practices can really help extend the life of your machinery. Whether you're dealing with bulldozers, excavators, or any other heavy gear, a few simple steps can save you time and money down the line. Let’s explore some practical ways to ensure your equipment lasts as long as possible.
Key Takeaways
- Perform daily inspections to catch issues early.
- Stick to a preventative maintenance schedule to avoid costly repairs.
- Train operators on proper usage and maintenance needs.
- Store equipment properly to protect it from the elements.
- Use quality parts and fluids to enhance performance.
Daily Equipment Inspections
Importance of Daily Checks
Okay, so picture this: you're about to start a big job, and the excavator decides it's not feeling up to it. That's what we're trying to avoid with daily checks. These aren't just a formality; they're your first line of defense against downtime. A quick walk-around can catch small problems before they turn into big, expensive headaches. Think of it like a doctor's check-up for your machines – preventative care is key. Plus, OSHA mandates daily inspections for heavy machinery, so it's not just good practice, it's the law.
Common Issues to Look For
Alright, what exactly are we looking for? Well, it's more than just kicking the tires (though, check those too!). Here's a quick rundown:
- Fluid Levels: Oil, coolant, hydraulic fluid – are they where they should be? Low levels can spell trouble.
- Leaks: Any drips or puddles? Find the source and address it ASAP.
- Hoses and Belts: Cracks, frays, or looseness? These are wear items that need regular attention.
- Tire Pressure: Underinflated tires can reduce fuel efficiency and increase wear. Proper inflation is crucial.
- Lights and Signals: Are all lights working? Horn, backup alarms? Safety first!
Don't just glance – really look. Get familiar with how your equipment should look and sound. That way, you'll notice anything out of the ordinary right away.
Benefits of Familiarity with Equipment
This is where it gets interesting. The more you inspect, the more you learn. You'll start to recognize subtle changes in sound or performance that might indicate a problem brewing. It's like developing a sixth sense for your equipment. Plus, when you know your machines inside and out, you're better equipped to troubleshoot minor issues yourself, saving time and money on repair calls. Regular inspections can help you spot any issues early on. It's all about being proactive, not reactive.
Preventative Maintenance Practices
Okay, so you want your heavy equipment to last? Then you absolutely must get serious about preventative maintenance. It's not just about fixing things when they break; it's about stopping them from breaking in the first place. Think of it like going to the doctor for a check-up, even when you feel fine. It's the same principle. Regular maintenance will save you money and headaches down the road.
Scheduled Maintenance Plans
Having a solid, scheduled maintenance plan is key. This isn't something you can just wing. You need a detailed plan that outlines when each piece of equipment needs servicing, what needs to be checked, and who is responsible. A well-structured plan will cover everything from oil changes to filter replacements, and even tire rotations. It's also a good idea to keep detailed service records of all maintenance performed. This helps you track what's been done and when it's due again.
Fluid Sampling and Analysis
This might sound a bit technical, but it's actually pretty straightforward. Fluid sampling involves taking small samples of your equipment's fluids (oil, coolant, hydraulic fluid) and sending them to a lab for analysis. The lab can tell you if there are any contaminants in the fluid, if the fluid is breaking down, or if there are any signs of wear and tear inside the equipment. Catching these problems early can prevent major failures. It's like getting a blood test for your machine.
Addressing Minor Repairs Promptly
Don't ignore those little problems! That small leak, that funny noise, that slightly loose bolt – they can all turn into big, expensive problems if you let them go. Think of it like a cavity; if you don't get it filled, it'll eventually turn into a root canal. Addressing minor repairs promptly not only prevents further damage but also extends the life of your equipment. Plus, it's often cheaper to fix a small problem than a big one. Consider regular inspections to catch these issues early.
Ignoring minor issues is like ignoring a small leak in your roof. It might not seem like a big deal at first, but eventually, it will cause major damage. The same goes for your heavy equipment. Don't let small problems turn into big ones. Take care of them right away, and you'll save yourself a lot of time, money, and hassle in the long run.
Operator Training and Education
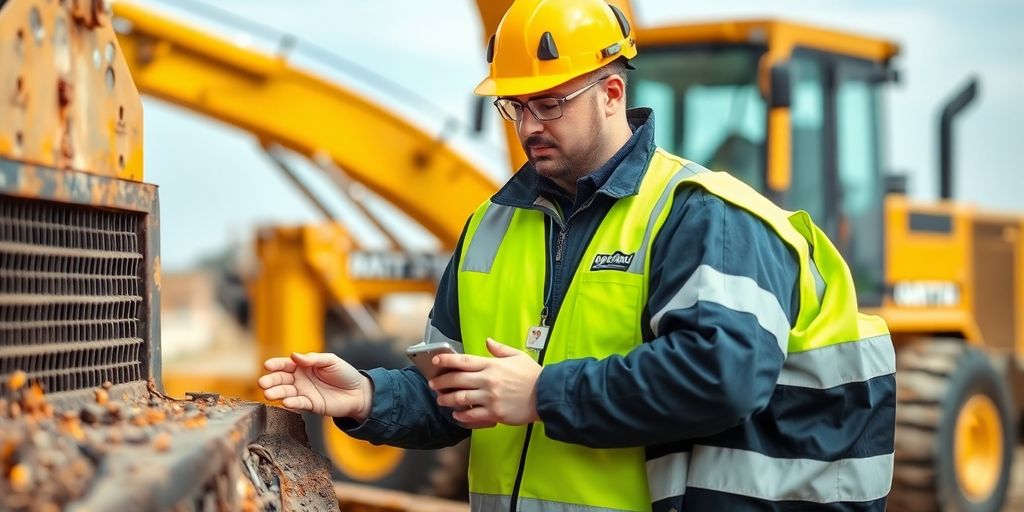
It's easy to overlook, but how well your operators are trained directly impacts the lifespan of your equipment. It's not just about knowing how to turn it on and off; it's about understanding the machine's capabilities, limitations, and how to operate it efficiently. A well-trained operator is less likely to abuse the equipment, leading to fewer breakdowns and a longer service life. Plus, they're more likely to spot potential problems early on, preventing small issues from turning into major (and expensive) repairs.
Training on Equipment Use
Proper training on equipment use is more than just showing someone the controls. It's about teaching them the best practices for operating the machine in various conditions. This includes understanding the proper techniques for excavators and loaders, as well as how to adjust the equipment for different types of materials and terrain. Good training emphasizes safety and efficiency, ensuring that operators can perform their jobs effectively without putting themselves or the equipment at risk. Regular, on-the-job training can help reinforce good habits and address any bad ones that may have developed. It's also important to provide training when new equipment or technology is introduced. This ensures that everyone is on the same page and can contribute to projects productively. Don't forget to monitor workers after training to reinforce good practices.
Understanding Maintenance Needs
Operators should also be trained to understand the basic maintenance needs of the equipment they're using. This doesn't mean they need to be certified mechanics, but they should be able to perform daily checks, identify potential problems, and know when to report issues to the maintenance team. This includes knowing how to check fluid levels, inspect hoses and belts, and identify unusual noises or vibrations. By understanding these basic maintenance needs, operators can help prevent minor issues from escalating into major repairs. This proactive approach can significantly extend the life of the equipment and reduce downtime. Consider using quality tags and labels to help operators easily identify key maintenance points.
Minimizing Idle Time
Excessive idling is a silent killer of heavy equipment. It wastes fuel, increases wear and tear on the engine, and contributes to unnecessary emissions. Training operators to minimize idle time can have a significant impact on the lifespan of the equipment. This includes teaching them to shut down the engine when the equipment is not in use, to avoid unnecessary idling during breaks, and to plan their work efficiently to minimize the need for idling. Effective training should cover the costs associated with idling, such as increased fuel consumption and maintenance expenses.
By reducing idle time, you can save money on fuel, reduce wear and tear on the engine, and extend the overall lifespan of your equipment. It's a simple change that can have a big impact.
Here are some ways to minimize idle time:
- Turn off the engine during breaks and lunch periods.
- Plan work efficiently to minimize the need for idling.
- Use auto-idle shutdown features, if available.
Proper Equipment Storage Techniques
Proper storage is more than just parking your equipment; it's about protecting your investment when it's not in use. Think of it as giving your machines a well-deserved rest in a safe environment. Neglecting this aspect can lead to unnecessary wear and tear, corrosion, and even component failure. Let's explore some key techniques to ensure your equipment is ready to go when you need it.
Indoor vs Outdoor Storage
The age-old question: inside or outside? Ideally, indoor storage is the way to go. A controlled environment protects against the elements, reducing the risk of rust, UV damage, and temperature-related issues. However, indoor space isn't always available. If outdoor storage is your only option, consider these points:
- Use equipment covers: Invest in high-quality, waterproof covers to shield your machines from rain, snow, and sun.
- Elevate equipment: Place equipment on wooden blocks or pallets to prevent direct contact with the ground and reduce moisture exposure. This is especially important during wet seasons.
- Choose a well-drained location: Avoid storing equipment in low-lying areas prone to flooding or standing water.
Outdoor storage can be tough on equipment. Always prioritize protection from the elements to minimize potential damage.
Winterization Procedures
Winter can be especially harsh on heavy equipment. Proper winterization is crucial to prevent damage from freezing temperatures. Here's a basic checklist:
- Drain fluids: Drain all water-based fluids, such as coolant and windshield washer fluid, to prevent freezing and expansion, which can crack engine blocks and other components.
- Add fuel stabilizer: Add a fuel stabilizer to the fuel tank to prevent fuel degradation and keep the fuel system clean.
- Lubricate: Lubricate all moving parts to prevent rust and corrosion during storage. Pay special attention to exposed metal surfaces.
- Battery care: Remove the battery and store it in a warm, dry place. Use a trickle charger to maintain the battery's charge throughout the winter.
Protecting from Environmental Damage
Beyond weather, other environmental factors can impact equipment during storage. Consider these preventative measures:
- Pest control: Implement pest control measures to prevent rodents and insects from damaging wiring, hoses, and other components. Regularly inspect storage areas for signs of infestation.
- UV protection: If storing equipment outdoors, use UV-resistant covers or apply a protective coating to prevent sun damage to paint, rubber, and plastic parts.
- Security: Secure storage areas to prevent theft and vandalism. Install security cameras, fences, and lighting to deter unauthorized access. Consider sturdy pallet racking systems for organized storage of smaller parts and components.
Utilizing Quality Parts and Fluids
It's tempting to save a few bucks by going with cheaper, generic parts and fluids for your heavy equipment. But trust me, that initial savings can quickly disappear when you're dealing with breakdowns and repairs down the road. Investing in high-efficiency machinery and components is an investment in the longevity and reliability of your machines.
Benefits of Genuine Parts
Using genuine parts, especially from the original equipment manufacturer (OEM), offers several advantages:
- Guaranteed Compatibility: OEM parts are designed to work seamlessly with your equipment, eliminating guesswork and potential fitment issues.
- Enhanced Performance: These parts are engineered to meet the exact specifications of your machine, ensuring optimal performance and efficiency.
- Extended Lifespan: Genuine parts are typically made from higher-quality materials and undergo rigorous testing, resulting in a longer service life.
Think of it like this: your heavy equipment is a complex system, and each part plays a vital role. Using subpar components can throw off the entire system, leading to premature wear and tear on other parts.
Choosing the Right Lubricants
Lubricants are the lifeblood of your heavy equipment. Selecting the correct type and grade of lubricant is crucial for protecting engine components, reducing friction, and preventing overheating. Here's what to consider:
- Viscosity: Choose a viscosity that's appropriate for the operating temperature and load conditions.
- Additives: Look for lubricants with additives that provide enhanced protection against wear, corrosion, and oxidation.
- OEM Recommendations: Always consult your equipment's manual for the manufacturer's recommended lubricants.
Impact of Quality Fuels
Fuel quality can significantly impact your equipment's performance and lifespan. Contaminated or low-quality fuel can lead to:
- Reduced Power Output: Poor fuel combustion can decrease engine power and efficiency.
- Increased Emissions: Low-quality fuel often contains higher levels of pollutants, leading to increased emissions.
- Engine Damage: Contaminants in fuel can damage fuel injectors, pumps, and other engine components.
To ensure optimal fuel quality, consider the following:
- Source from Reputable Suppliers: Choose fuel suppliers with a reputation for quality and reliability.
- Use Fuel Additives: Consider using fuel additives to improve fuel stability, prevent corrosion, and clean fuel injectors.
- Regularly Inspect Fuel Filters: Check and replace fuel filters regularly to remove contaminants from the fuel system.
Monitoring Equipment Performance
Using Technology for Tracking
Keeping tabs on how your heavy equipment is performing can feel like a huge task, especially when you're dealing with multiple machines across different job sites. Luckily, we've got technology on our side. There are a bunch of systems out there that let you track all sorts of data, from engine hours to fuel consumption. This data can be a game-changer for spotting potential problems early on.
- GPS tracking for location and movement.
- Telematics systems for real-time data on performance.
- Software solutions for data analysis and reporting.
By using these tools, you can get a much clearer picture of how your equipment is being used and identify areas where you can improve efficiency or prevent breakdowns. It's all about working smarter, not harder.
Identifying Performance Issues
Once you've got the data flowing in, the next step is to actually make sense of it. Look for patterns or anomalies that could signal trouble. Is a certain machine consistently using more fuel than it should? Are there unusual spikes in engine temperature? These could be signs of underlying problems that need attention. Regular equipment inspections are also important.
- Analyze fuel consumption rates.
- Monitor engine temperature and pressure.
- Track error codes and warning lights.
Adjusting Operations Based on Data
Okay, so you've identified some performance issues. Now what? This is where you take action based on what the data is telling you. Maybe you need to adjust your maintenance schedule, retrain operators on proper equipment use, or even re-evaluate whether you're using the right machine for the job. Remember to study the performance limitations of your equipment.
Matching Equipment to Job Requirements
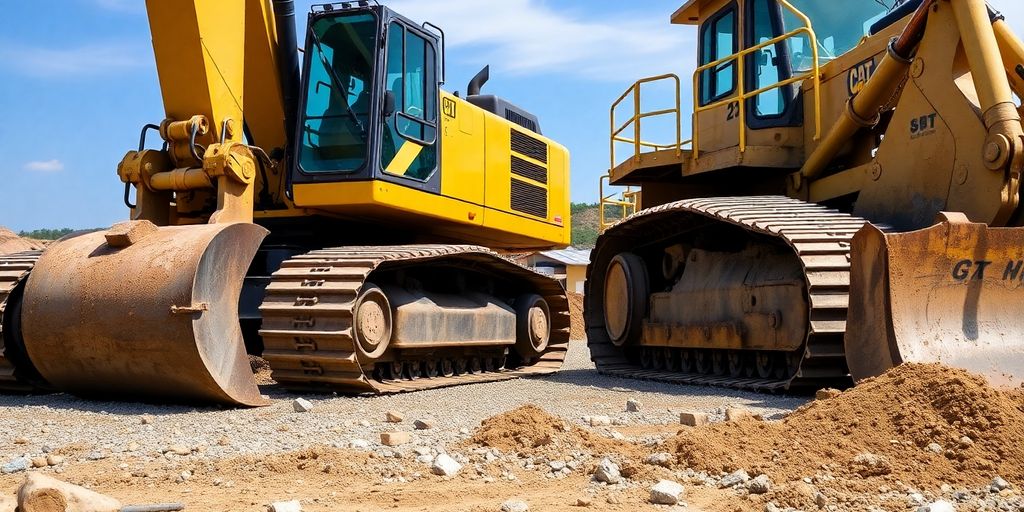
It's easy to think any piece of heavy equipment can handle any task, but that's just not true. Using the wrong equipment can lead to breakdowns, reduced efficiency, and even safety hazards. Let's look at how to make sure you're using the right tool for the job.
Choosing the Right Size Equipment
Selecting equipment of the appropriate size is paramount for optimizing both efficiency and safety on any job site. It's tempting to go with the biggest machine available, but that's not always the best approach. A too-large machine can be unwieldy and consume excessive fuel, while a too-small machine will struggle and wear out faster. Consider the scope of the project, the space available, and the specific tasks that need to be completed. Proper calculations can help determine the appropriate size needed for efficiency and effectiveness.
Understanding Load Capacities
Every piece of equipment has a load capacity, and exceeding it is a recipe for disaster. Overloading can damage the machine, compromise its stability, and put operators at risk. Always consult the manufacturer's specifications to understand the load limits and ensure that you're operating within those boundaries. It's also important to consider the type of load being handled. Unevenly distributed loads can create additional stress on the equipment, so proper load distribution is essential.
Avoiding Overuse and Underuse
Using equipment outside its intended purpose or capacity can significantly shorten its lifespan. Overusing equipment, by pushing it beyond its limits, leads to increased wear and tear on components. Underusing equipment, on the other hand, can result in inefficiencies and wasted resources. Diesel engines, for example, perform best under optimal loads. If a machine spends too much time idling, it wastes fuel and increases engine wear. Matching the equipment to the job requirements ensures that it operates within its designed parameters, maximizing its lifespan and productivity.
It's not just about having the right equipment; it's about using it correctly. Proper training and adherence to manufacturer guidelines are essential for preventing damage and ensuring safe operation. Regular inspections and maintenance can also help identify potential problems before they escalate, further extending the life of your heavy equipment.
Wrapping It Up
In the end, taking care of your heavy equipment is all about being proactive. Regular checks, proper maintenance, and using the right parts can make a huge difference. Sure, it might take some time and effort, but it pays off in the long run. You’ll save money, avoid unexpected breakdowns, and keep your machines running smoothly. So, make it a habit to stay on top of your equipment care. It’s not just about keeping things working; it’s about getting the most out of your investment. Keep your gear in shape, and it’ll serve you well for years to come.
Frequently Asked Questions
How often should I inspect my heavy equipment?
You should inspect your heavy equipment every day, at the start and end of each work shift.
What are some common issues to look for during inspections?
Look for leaks, worn-out parts, low fluid levels, and any unusual noises or vibrations.
Why is preventative maintenance important?
Preventative maintenance helps catch small problems before they become big, costly repairs.
How can operator training help extend equipment life?
Proper training teaches operators how to use equipment correctly, reducing wear and tear.
What should I consider for equipment storage?
Store equipment indoors if possible, and winterize it to protect it from cold weather and moisture.
Why is using quality parts and fluids important?
Using genuine parts and high-quality fluids can prevent breakdowns and improve the overall performance of your equipment.