How AI and Automation Are Changing the Heavy Machinery Industry
.png)
The heavy machinery industry is undergoing a major transformation thanks to advancements in artificial intelligence (AI) and automation. These technologies are not just buzzwords; they are reshaping how machinery operates, how maintenance is performed, and even how construction sites are managed. As companies increasingly adopt these innovations, the industry is becoming more efficient, safer, and environmentally friendly. Let's explore the various ways AI and automation are making an impact in this field.
Key Takeaways
- AI is revolutionizing predictive maintenance, extending equipment life and reducing downtime.
- Autonomous vehicles are becoming common, improving safety and efficiency on construction sites.
- Integrating AI with IoT leads to smarter manufacturing and real-time monitoring of machinery.
- Challenges like high costs and the need for skilled workers still exist in AI adoption.
- Sustainability is enhanced through automation, contributing to energy efficiency and reduced waste.
Transforming Predictive Maintenance
Enhancing Equipment Longevity
Modern heavy machinery now uses smart sensors that keep a regular check on equipment condition. Data from these sensors, such as temperature and vibration levels, helps spot signs of wear early. Using predictive data to act before a breakdown happens extends machine life considerably.
Key benefits include:
- Timely repairs that stop small issues from becoming big expensive problems.
- Better scheduling of routine check-ups avoids the need for emergency fixes.
- More predictable maintenance work that fits into daily operations.
Reducing Downtime
Sensors alert maintenance teams when equipment starts to show signs of trouble. This early warning system means repairs can be done during controlled breaks rather than unexpected stops.
By keeping a close eye on machines, teams can fix issues before they cause long, costly delays.
Steps to reduce downtime:
- Regularly monitor sensor data and run quick inspections.
- Plan repairs at moments when production is less intense.
- Use the data to set up a repair schedule that minimizes work interruptions.
Data-Driven Insights
Gathering information over time builds a clear record of how equipment behaves. This record helps teams understand why parts may need replacement on a set schedule, and even spot trends that predict future issues. For instance, analysis of data shows that small adjustments can lead to longer periods between repairs.
Here’s a simple table to illustrate some measurements:
These insights, taken together, help operations run smoother, cutting down on costs and keeping machinery active for longer periods.
The Rise of Autonomous Construction Vehicles
Self-Driving Technology
Autonomous construction vehicles are gradually taking over parts of construction sites. They are equipped with systems that let them drive on their own, detect obstacles, and keep themselves on course. This shift means that fewer drivers are needed behind the wheel, and operators can focus on monitoring overall sites instead.
Some points about Self-Driving Technology:
- They use sensors to detect their surroundings.
- Software helps them decide the best path forward.
- They operate continuously with limited human input.
Often, these vehicles are updated with new algorithms that improve how they respond to everyday challenges. With AI at the core, these machines can adjust to changing conditions in real time.
Safety Improvements
One of the ways autonomous vehicles are making a mark is by reducing the risks usually seen in construction sites. They are designed to do repetitive tasks with fewer errors and can work in conditions that might be risky for a human operator.
- Automated systems help cut down on accidents.
- A consistent response to hazards boosts on-site safety.
- Reduced fatigue since tasks are not physically demanding.
Safety measures have become more robust with systems that react faster than a human ever could.
The move towards automation in construction vehicles is slowly changing the way work is done on sites. Workers see improvements in day-to-day operations and better safety records, adding overall value to their work environment.
Efficiency Gains
Efficiency gains are a major reason companies are excited about these self-operating vehicles. They do more in less time compared to traditional machinery.
Below is a brief table summarizing some efficiency gains:
Here are some more observations:
- They work longer hours without breaks.
- Their precision reduces waste of materials.
- System updates help to fine-tune their performance consistently.
Overall, these vehicles represent a new way of looking at construction safety and productivity, making day-to-day tasks simpler and more reliable.
Integrating AI with Digital Technologies
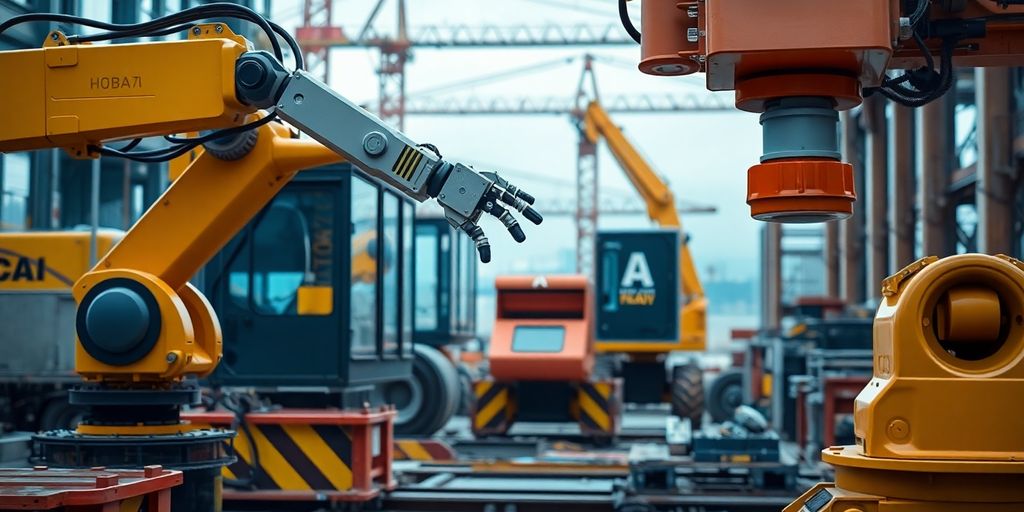
This section shows how mixing AI with digital tools is creating a new way to run heavy machinery. Machines are now connected and sharing data, and the blend of smart sensors with computer-driven analysis is making systems work better and faster.
IoT and AI Synergy
When you put the Internet of Things (IoT) together with AI, you get systems that can instantly react to changes in the environment. Here are a few ways this plays out:
- Constant data flow from sensors that monitor machine health.
- Automated corrections on the fly to keep operations smooth.
- Reduced manual checks and more informed maintenance scheduling.
Integration of these systems allows plants to optimize operations in ways that weren’t imagined before.
Smart Manufacturing Solutions
Modern factories are adopting smart solutions that mix digital control with hands-on manufacturing work. The changes are visible in several areas:
- Modern control systems that adjust operations automatically.
- Step-by-step process updates that make sure every action is on track.
- Automated alerts to help teams fix small issues before they become big problems.
The fusion of these technologies brings new levels of efficiency to traditional manufacturing.
Real-Time Monitoring
Keeping an eye on everything in real time means problems get spotted and fixed as they happen. This feature boosts productivity and safety. Consider this simple table:
This system of keeping track of every part of the operation makes the work more straightforward and cuts down on surprises.
A solid real-time monitoring setup can be a game changer in busy work environments, making sure issues are caught before they cause delays.
By blending these digital tools with traditional methods, the heavy machinery industry is stepping into a whole new way of working that mixes ease with smart tech.
Challenges in AI Adoption
High Initial Investment
Adopting AI can feel like stepping off a financial cliff because the upfront costs are steep. Companies must invest in new hardware, updated software, network overhauls, and training initiatives all at once. These costs often strain budgets before any tangible savings appear. Many businesses face challenges such as:
- Large capital allocation requirements
- Extended timelines before return on investment is evident
- Limited access to financing options
Privacy and Data Security
As machinery becomes smarter, keeping operational data safe grows tougher. There’s always a risk that sensitive information might slip into the wrong hands. Firms are taking steps like:
- Employing robust encryption measures
- Routine security audits and updates
- Implementing strict access controls
These efforts aim to reduce the chance of data breaches while managing increasing interconnectivity.
Need for Skilled Labor
A critical yet often overlooked hurdle is finding workers who can handle advanced AI tech. The shortage of skilled talent forces many companies to spend extra time and money on recruitment and training. Common approaches to this challenge include:
- Developing in-house training programs tailored to new tech
- Collaborating with technical schools for fresh talent
- Partnering with industry experts during transition phases
Tackling these challenges requires patience, investment, and a willingness to adjust company culture. A focus on making early investments affordable and supported by the right team can eventually lead to smoother, more secure operations.
Sustainability Through Automation
Energy Efficiency
Automation now plays a big role in saving energy in ways that make a real difference. Modern systems can quietly adjust power usage so nothing is wasted. For instance, here’s a simple table comparing energy usage before and after automation:
A smart system can shave off major wasted energy on a daily basis. This shift often allows facilities to not only cut costs, but also to operate with less strain on resources, making operations smoother.
Waste Reduction
A major benefit of smarter processes is the reduction of waste. By streamlining production, automation minimizes the chances of producing off-spec products or overusing materials. Consider a few ways this happens:
- Automated sensors trigger shutoffs to stop excess use of materials.
- Early detection systems catch errors before they balloon into waste.
- Cleaner process cycles help handle byproducts safely.
Adding zero emission electric models into a setup boosts these efforts, merging efficiency with environment-friendly practices.
Sustainable Practices
Automation also helps companies adopt more sustainable practices by modernizing maintenance and better scheduling operations. This approach is breaking down old habits and setting up systems that make work cleaner and greener. Look at some common changes:
- Regular checks are scheduled automatically to prevent breakdowns.
- Energy and material usage are tracked in real time, letting teams adjust plans quickly.
- Logistics are streamlined, reducing unnecessary trips and emissions.
Even small changes in machine management can make a big environmental impact over time. By integrating smart systems, businesses gradually lower their carbon footprint while boosting overall operation performance.
Future Trends in Heavy Machinery
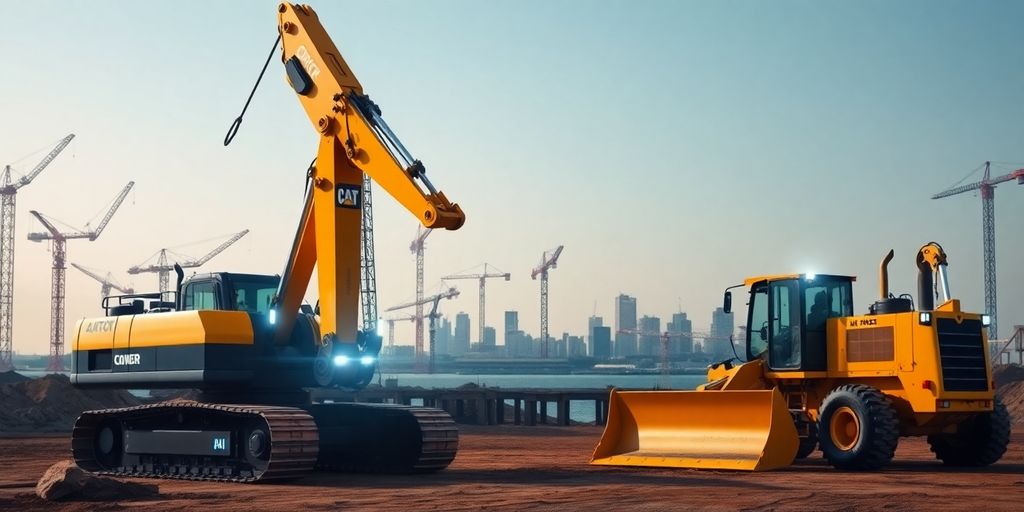
Innovations on the Horizon
The heavy machinery industry is experimenting with new ideas that are reshaping what equipment can do. Many companies are now trying out more flexible machines that work on their own and need less help from people. Some builders are mixing new sensors with smart systems to diagnose issues early. For example, the days of waiting until something fails are becoming history as parts get replaced before problems start. This trend is connected to market innovations, which is drawing interest across the board.
Market Growth Projections
The market for smart heavy machinery is heading into an exciting phase. Companies are predicting numbers that show a healthy rise over the years. See the table below for a quick snapshot of what experts expect in upcoming market years:
These projections come with a mix of cautious optimism and the need for gradual adaptation. The numbers indicate a significant shift in investment priorities for many manufacturers.
Impact on Workforce Dynamics
Changes in technology are also affecting work practices. As machines get smarter, workers see their roles shift. A few common ways the workforce is evolving include:
- More need for hands-on tech maintenance
- New training programs aimed at digital skills
- Adjustments in job responsibilities to support modern systems
Even as some jobs might seem to fade out, others are growing, especially in technical and support roles. The dynamic is a mixed bag, but there is a clear push for more skills that match today’s demands. One can see that the integration of new systems is creating new opportunities, and soon enough, efficiency will be at the heart of daily operations.
With ongoing developments, it's clear that adapting to these changes will be key for everyone involved. The evolution might be challenging at first, but it is set to shape a smarter and more responsive future in heavy machinery.
Conclusion
In summary, AI and automation are shaking things up in the heavy machinery sector. These technologies are not just fancy tools; they’re changing how companies operate. With smarter machines, businesses can work faster and safer. Sure, there are bumps in the road, like the need for training and the costs involved, but the upsides are hard to ignore. Companies that jump on this bandwagon will likely find themselves ahead of the game. The future looks promising for those ready to adapt and innovate.
Frequently Asked Questions
How does AI improve maintenance for heavy machinery?
AI helps in predicting when machines need repairs, which means they can last longer and work better.
What are autonomous construction vehicles?
These are machines that can drive themselves without a human in control, making construction safer and more efficient.
How does AI work with other technologies?
AI can combine with the Internet of Things (IoT) to create smart machines that monitor themselves and report issues.
What challenges do companies face when using AI?
Some challenges include high costs to start using AI, keeping data safe, and needing workers who know how to use the new technology.
Can automation help the environment?
Yes, automation can make machines use less energy and produce less waste, which is better for the planet.
What does the future look like for heavy machinery?
The future will likely see more advanced machines that are safer, more efficient, and can do more tasks with less human help.