Heavy Machinery Lubrication: Why It’s Essential for Longevity
.png)
Heavy machinery plays a vital role in various industries, from construction to manufacturing. However, keeping these machines running smoothly isn't just about routine checks and repairs; it's about lubrication. Proper lubrication is key to ensuring that these machines operate efficiently and last longer. In this article, we'll explore why heavy machinery lubrication is essential for longevity, covering everything from types of lubricants to best practices and future trends.
Key Takeaways
- Regular lubrication minimizes wear and tear on machinery.
- Choosing the right lubricant enhances operational efficiency.
- Automatic lubrication systems can simplify maintenance tasks.
- Proper lubrication reduces the risk of overheating and equipment failure.
- Staying informed about lubrication trends can improve machinery longevity.
Importance of Heavy Machinery Lubrication
Proper lubrication is not just another checklist item. It keeps the machine moving without bumping into problems down the road. When you use the right lubricants and techniques, you can avoid a lot of unexpected hassles.
Minimizing Wear and Tear
Machines endure lots of friction when they run day in and day out. Using good lubricants cuts down on that metal-on-metal contact. Consider these points:
- It lessens direct contact between moving parts.
- It helps keep components from getting too worn out too quickly.
- It lowers the chance of sudden breakdowns.
Without proper lubrication, parts can wear out much faster, leading to more frequent and costly repairs.
For instance, you might find that using the right Lubrication tools really changes the game in slowing down wear.
Enhancing Operational Efficiency
Smooth movement means tasks get done more cleanly and with fewer hiccups. Sometimes, a simple lubricant can keep things running like clockwork. Look at the breakdown below:
These points add up, meaning machines spend more time working and less time sitting idle because of issues.
Preventing Overheating
When machines run, they generate heat. The right lubricants help keep temperatures in check. Here’s how it helps:
- It carries heat away from critical parts.
- It creates a thin protective layer that stops metal from frying under pressure.
- It works well even when using synthetic oil in high-stress environments.
A well-lubricated machine is like a well-oiled bike. It runs smoother, stays cooler, and surprises you by lasting longer.
Overall, paying attention to lubrication makes a big difference. You’ll notice fewer breakdowns and a machine that runs a lot more reliably over time. Regular maintenance, using proper Lubrication tools, and checking your levels go a long way to keeping heavy equipment on track.
Types of Lubricants for Heavy Machinery
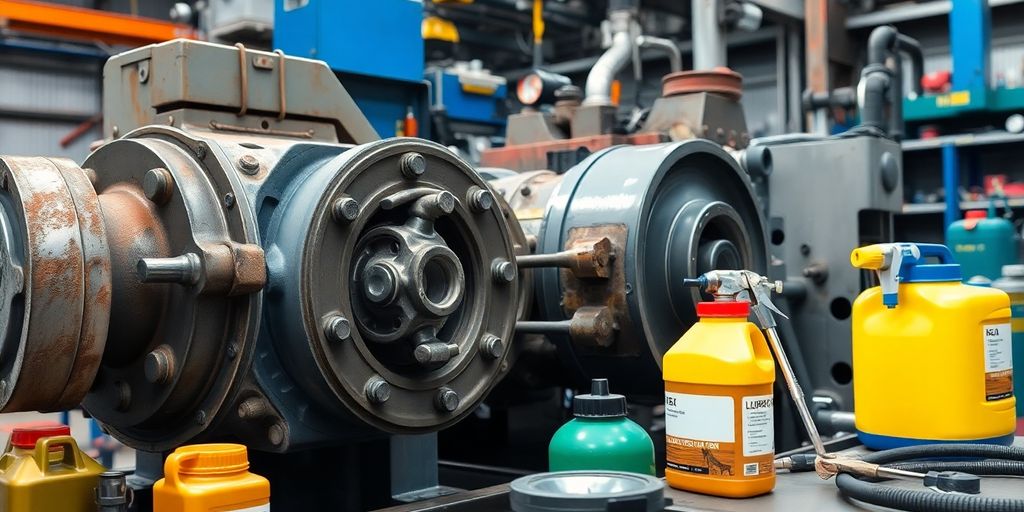
When it comes to heavy machinery, choosing the right lubricant is a bit like deciding between different tools for a tough job. There are many options out there, and sometimes it gets confusing. Let’s explore the three main comparisons to help you get a handle on it. Also, check out an industrial lubricant that fits the heavy duty needs perfectly.
Grease vs. Oil
You might wonder why some machines use grease while others use oil. A few points can clear things up:
- Grease tends to stick to parts, offering longer-lasting coverage in harsh spots.
- Oil flows easily, helping carry heat away from moving pieces.
- Grease is handy when you need a thick barrier to keep out dirt and moisture.
Grease often wins when staying on parts matters most. But don’t count oil out—it’s got its place in keeping parts moving smoothly.
Synthetic vs. Conventional
When comparing synthetic lubricants with conventional ones, the differences often come down to performance and cost. Here’s what you should know:
- Synthetic lubricants generally provide more stable behavior in temperature swings.
- Conventional ones are usually easier on the budget while still doing the job.
- The choice often depends on the work environment and load demands.
A simple list of benefits includes:
- Better longevity in extreme conditions (synthetic might cover this better).
- Lower cost for everyday use with conventional options.
- Consistency in performance across a variety of settings.
High-Temperature Lubricants
Machines operating in very warm or extreme conditions need lubricants that can stand up to the heat. High-temperature lubricants are specially formulated for this purpose. They help in lowering friction even when the engine parts heat up a lot.
Here’s a quick comparison table outlining some of the key differences:
Heavy machinery often faces conditions that push lubricants to their limits. Using a lubricant designed to handle high heat can be the difference between a well-running machine and unexpected breakdowns.
Every machine and operation is unique, so balancing these types of lubricants will help keep your equipment running longer without breaking the bank or stalling operations. Enjoy figuring out which one works best for your gear!
Automatic Lubrication Systems
Benefits of Automation
Automatic lubrication systems take the guesswork out of everyday machine care. Instead of scheduling manual checks all the time, these systems work on their own to keep parts running smoothly and evenly. Automatic lubrication systems save time and reduce the chance of mistakes that can lead to too much or too little lubricant. Here are some positive impacts these systems provide:
- Consistent application at all needed points
- Reduced labor and maintenance hours
- Fewer equipment breakdowns
Using an automatic setup means you can count on reliability while the system takes care of the routine tasks.
Components of a Lubrication System
Behind the scenes, automatic lubrication systems rely on several parts that work in harmony. The key components usually include a high-pressure pump, dispensing valves, and a central control unit. This table summarizes the main parts and what they do:
Each piece is important because, if one fails, the whole system might not deliver enough lubrication.
Maintenance of Lubrication Systems
Even though the system operates on its own, it still needs care. Regular checks help avoid small issues turning into big problems. A few good habits include:
- Scheduling regular inspections to catch wear and tear early
- Cleaning or replacing filters and valves periodically
- Monitoring lubricant levels and system performance
Remember, taking a few minutes for routine checks can save hours of downtime later.
Keeping up with maintenance ensures the system continues to run as intended over time.
Impact of Lubrication on Machinery Longevity
Extending Equipment Life
Regular lubricant application helps reduce friction and prevent heat buildup. Over time, this simple step protects components from wear and tear and extends the overall life of machinery. Here are a few ways consistent lubrication works its magic:
- Better friction management
- Lower operating temperatures
- Protection against rust and corrosion
Reducing Downtime
When machines are well-lubricated, they are less likely to suffer from unexpected issues that lead to interruptions. This approach cuts down the need for sudden repairs or part replacements. Think of it like giving your machine a quick tune-up every shift:
- Routine lubricant checks
- Timely part replacements
- Consistent monitoring of performance indicators
Regular maintenance can be the difference between a short pause and a full stop. It's a small step that saves a lot of time in the long run.
Improving Performance
Proper lubrication not only keeps machines running longer but also helps them run better. This routine makes a noticeable difference in efficiency. When lubrication is on point, there's less friction and smoother movement of parts. Consider the following breakdown of improvements:
Additional benefits include:
- Consistent performance output
- Lower energy consumption
- Quieter and smoother operations
Proper lubrication is more than just routine maintenance—it's a key step in keeping equipment in reliable condition for years.
Best Practices for Heavy Machinery Lubrication
Regular Maintenance Schedules
Keeping up with a regular maintenance schedule can mean the difference between smooth operations and unexpected breakdowns. It’s a good idea to have a routine that covers basic inspections and timely top-ups of lubricants. Below is a quick reference table for common inspection and lubrication intervals:
Stick to a schedule, and you could avoid unexpected repairs that disrupt work.
Choosing the Right Lubricant
When it comes to picking a lubricant, it’s not a one-size-fits-all deal. Machines vary, and so do operating conditions. Don’t underestimate the power of the right lubricant choice. Here are some factors to keep in mind:
- Consider the machine’s operating temperature range
- Think about the type of load the machine handles
- Verify compatibility with existing machine parts
Often, the best choice comes down to matching the lubricant with the specific demands of your machinery. Take your time, and if necessary, consult a guide or expert to get it right.
Monitoring Lubrication Levels
Keeping track of lubrication levels is as important as applying the right amount in the first place. A few straightforward steps can help here:
- Check lubricant gauges frequently – daily, if possible.
- Record levels in a maintenance log to detect patterns.
- Adjust schedules based on wear-and-tear reports.
Regular monitoring not only saves money but also prevents downtime from sudden failures. Setting a few reminders can save you a lot of hassle in the long run.
Challenges in Heavy Machinery Lubrication
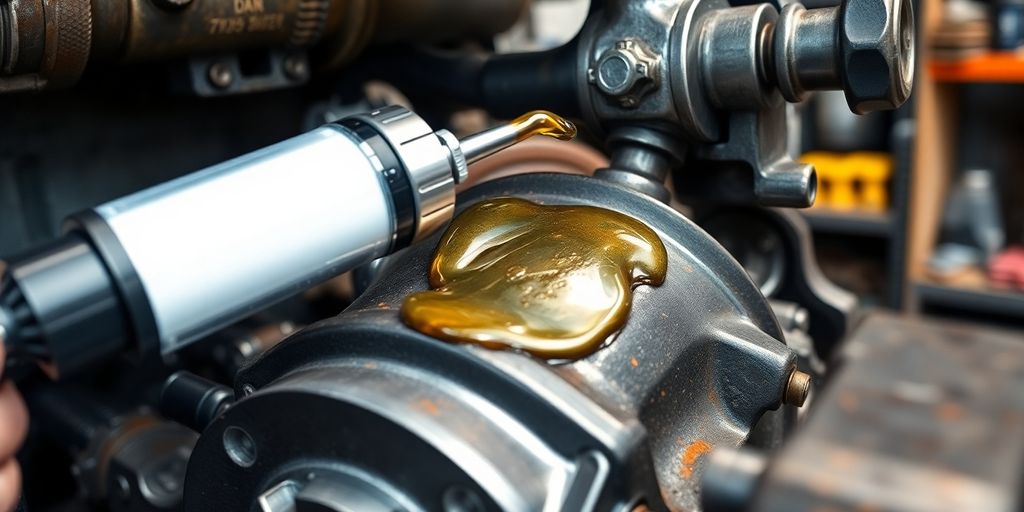
When it comes to heavy machinery, keeping everything running smoothly isn't as simple as it may seem. Lubrication challenges are a real headache and can lead to larger issues if not sorted out quickly.
Environmental Factors
Weather and surroundings often mess with your lubrication practices. Dust, rain, extreme temperatures, and even salt in coastal areas can break down your lubricants faster than you expect. Ignoring these factors can lead to costly repairs. Even the best lubricants can become ineffective under harsh conditions. For instance, a bit of unexpected moisture can start a chain reaction of wear that no one wants. Check out lubrication issues for common pitfalls.
Heavy machinery operates in unpredictable environments, and knowing the risks is half the battle. Adjust your practices and always be prepared for the unexpected.
Operational Conditions
Your machinery's day-to-day tasks also add plenty of strain to lubrication. Machines doing heavy-duty work day in and day out usually face a mix of conditions like high load, continuous operation, and sudden stops. Here’s a simple table showing some typical stress points:
This data shows that operational conditions directly affect how well your lubricant performs. Keeping an eye on these factors and adjusting your lubrication routine is key to preventing breakdowns. Look into lubrication issues for more insights on how operational wear can affect your machine's health.
Common Misconceptions
There are some myths floating around about heavy machinery lubrication that can actually hurt machine performance. Here are a few misconceptions you often hear:
- The belief that more lubricant means better protection, even though overgreasing can cause its own problems.
- Assuming that all lubricants are interchangeable regardless of the task or machine design.
- Thinking that once you fill up, there's no need for periodic checks or maintenance.
These mistaken ideas can lead to improper application of lubricants, and over time, this negligence builds up to major machinery issues. Getting the right information can make a huge difference, so be critical and always update your knowledge on lubrication challenges.
By keeping these points in mind, your approach to lubrication can change from reactive to proactive. Happy maintaining!
Future Trends in Machinery Lubrication
Smart Lubrication Technologies
The machinery world is watching how smart sensors and real-time data can change the way we care for heavy equipment. New gadgets and tiny devices are linking up with machinery to keep track of when things need a little extra attention. Sometimes, you might even see adjustments made automatically. One standout example is the integration of tech trends that helps respond to changes as they happen.
New smart lubrication tools are saving man-hours while slashing unexpected failures.
Here are a few benefits seen with smart lubrication:
- Faster response times to lubricant needs
- Reduced manual checks and errors
- Better integration with overall system monitoring
Sustainability in Lubricants
Environmental care has hit the lubrication sector. Manufacturers are now looking at ways to reduce waste and limit any harmful effects on nature while keeping machines running. Some solutions include biodegradable lubricants and methods that lower overall chemical use. I have seen that even small steps can add up, especially with machines that work around the clock. One interesting note: a shift toward green formulas is slowly taking shape, focusing on reducing heavy metal residues and choosing renewables over synthetics.
A quick look at how sustainability is making a mark:
- Development of renewable lubricant bases
- Improvement in recycling used lubricants
- Better waste management protocols on the shop floor
Innovations in Lubrication Practices
New ideas are being tested to reduce friction in ways that were not seen before. Research teams are exploring unique mixtures and altering viscosity to better meet extreme operating conditions. Though it sounds technical, it’s really just about making sure machines keep working longer and smoother. Practical work by maintenance crews is showing that even minor adjustments in lubricant composition can make a difference.
A summary table of key innovations includes:
This area is constantly evolving, diving into new mixtures and testing tiny add-ons. Each advancement is small on its own but, together, they shape the future of machinery upkeep.
Wrapping It Up: The Importance of Lubrication
In the end, keeping heavy machinery running well really comes down to one thing: lubrication. It’s not just a chore to check off; it’s a vital part of keeping everything in good shape. Skipping out on proper lubrication can lead to some serious problems, like costly repairs and downtime. So, whether you're running a big construction site or just maintaining a few machines, remember that good lubrication practices can save you a lot of headaches down the road. It’s all about making sure your equipment lasts longer and works better, which is something every operator should prioritize.
Frequently Asked Questions
What is heavy machinery lubrication and why is it important?
Heavy machinery lubrication is when you apply a special substance to the moving parts of machines to keep them running smoothly. This is important because it helps the machines last longer, work better, and need fewer repairs.
What are the different types of lubricants for heavy machinery?
There are various types of lubricants, including grease and oil. Grease is thicker and good for high-pressure situations, while oil flows easily and is better for cooling.
What is an automatic lubrication system?
An automatic lubrication system is a setup that automatically applies lubricant to machines. This helps save time and ensures that machines get the right amount of lubricant consistently.
How does lubrication help machinery last longer?
Lubrication reduces friction and wear on machine parts, which helps them work better and last longer. It also prevents overheating, which can damage the machinery.
What are some best practices for lubricating heavy machinery?
Best practices include keeping a regular maintenance schedule, choosing the right type of lubricant for your machine, and checking lubrication levels often.
What challenges can affect heavy machinery lubrication?
Some challenges include harsh environmental conditions, how the machine is used, and common misunderstandings about lubrication needs.