Heavy Equipment Maintenance: Best Practices to Extend Machine Life
.png)
Keeping heavy equipment in top shape is no small task, but it’s one of the best ways to make sure your machines last longer and work better. Whether you’re in construction, farming, or manufacturing, taking care of your equipment is key to running an efficient and profitable operation. In this article, we’ll break down some practical tips and best practices to help you extend the life of your heavy machinery.
Key Takeaways
- Preventive maintenance is the backbone of extending equipment life. Regular checks and small fixes can save you from costly repairs later.
- Proper operator training ensures machines are used correctly, reducing wear and tear.
- Daily inspections help catch issues early, keeping your equipment running smoothly and safely.
- Using high-quality parts and consumables can make a big difference in how long your machinery lasts.
- Technology like maintenance software and IoT can streamline upkeep and predict problems before they happen.
The Role of Preventive Maintenance in Heavy Equipment Longevity
Understanding Preventive Maintenance
Preventive maintenance is all about staying ahead of potential problems. Instead of waiting for a machine to break down, you schedule regular check-ups and servicing. This might include inspecting parts, replacing worn components, and keeping everything clean and lubricated. The goal is simple: minimize downtime and extend the life of your equipment.
Think of it like going to the doctor for a yearly physical. You might not feel sick, but catching issues early saves you a world of trouble later. For heavy equipment, this approach means fewer costly repairs and less downtime on the job site.
Key Benefits of Proactive Care
Preventive maintenance isn’t just a checklist—it’s a game-changer for anyone managing heavy machinery. Here’s why:
- Reduced Downtime: Regular maintenance helps avoid unexpected breakdowns that can halt operations.
- Cost Savings: Fixing small issues early is way cheaper than dealing with a full-blown failure.
- Improved Safety: Well-maintained equipment is less likely to malfunction, keeping operators and job sites safer.
- Higher Resale Value: Machines with a documented maintenance history tend to fetch better prices when sold.
Common Preventive Maintenance Tasks
A solid preventive maintenance plan includes a variety of tasks, tailored to the specific equipment. Here are some of the most common ones:
- Fluid Checks and Changes: Regularly inspect and replace oil, hydraulic fluids, and coolants.
- Filter Replacements: Clean or swap out filters to keep systems running smoothly.
- Tire and Track Inspections: Check for wear and tear to avoid sudden failures.
- Lubrication: Keep moving parts well-oiled to reduce friction and wear.
- Battery Maintenance: Ensure batteries are charged and free of corrosion.
- System Diagnostics: Use tools to monitor engine health and other key systems.
Preventive maintenance is the backbone of a reliable fleet. It’s not just about keeping machines running today—it’s about ensuring they’re ready for tomorrow’s challenges.
Training and Skill Development for Equipment Operators
Importance of Operator Training
Well-trained operators are the backbone of efficient heavy equipment usage. Proper training doesn't just boost productivity—it extends the lifespan of your machinery. Operators who understand the ins and outs of their machines can spot potential issues early, reducing wear and tear. Training programs should emphasize safety, effective operation techniques, and routine maintenance awareness to ensure long-term benefits.
Best Practices for Skill Development
Building operator skills isn’t a one-and-done deal. Here’s how you can approach it:
- Start with Basics: Cover foundational skills like safe machine operation and understanding equipment controls.
- Hands-On Practice: Provide real-world scenarios where operators can practice under supervision.
- Ongoing Training: Keep up with advancements in equipment technology by offering regular refresher courses.
- Feedback Loops: Encourage operators to share their experiences and challenges for continuous improvement.
Leveraging Manufacturer Training Programs
Many equipment manufacturers offer specialized training programs. These programs are tailored to their machines and include:
- Detailed instructions on advanced features.
- Guidance on interpreting fault codes and alerts.
- Maintenance tips specific to their equipment models.
By participating in these programs, operators not only improve their skills but also gain insights into maximizing machine efficiency. This ensures your team is equipped to handle even the most complex equipment challenges.
Implementing a Comprehensive Inspection Routine
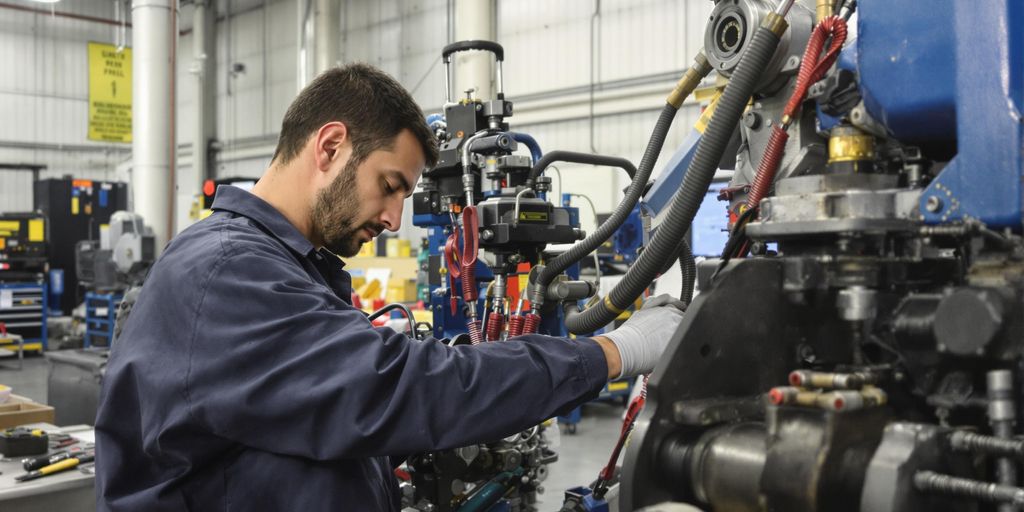
Daily Inspection Checklists
A daily inspection checklist is your first line of defense against unexpected equipment failures. Operators should walk around the machine, visually checking for obvious issues like leaks, loose parts, or worn-out components. Fluid levels—such as oil, coolant, and hydraulic fluid—must be checked daily to avoid operational hiccups. Here's a quick breakdown of what a daily checklist might include:
- Inspect tires for proper inflation and wear.
- Verify all lights, signals, and safety features are functional.
- Check for visible damage, leaks, or loose parts.
- Ensure safety equipment, like fire extinguishers, is in place and operational.
- Confirm that gauges and indicators are working as intended.
Regularly using a checklist not only keeps the equipment in top shape but also helps the operator become more familiar with the machine's condition. For more detailed tips on inspection, check out this guide to heavy equipment inspection.
Identifying Early Signs of Wear and Tear
Spotting problems early can save you from costly repairs down the road. Operators should pay attention to unusual noises, vibrations, or sluggish performance. Common signs to watch for include:
- Frayed wiring or loose electrical connections.
- Slack in chains, belts, or other tensioned components.
- Leaks around hydraulic systems or engine compartments.
- Cracks or dents in structural parts.
Documenting these issues immediately allows mechanics to address them before they escalate. Remember, minor fixes often prevent major breakdowns.
Using Technology for Efficient Inspections
Modern tools can make inspections quicker and more reliable. Maintenance management software allows operators to log inspection results digitally, providing an easily accessible record for future reference. Some systems even offer predictive analytics, flagging potential issues based on historical data.
Additionally, IoT-enabled sensors can monitor equipment in real-time, alerting you to problems like overheating or low fluid levels. These advancements reduce the guesswork and make your maintenance routine more efficient.
Optimizing Maintenance Schedules for Maximum Efficiency
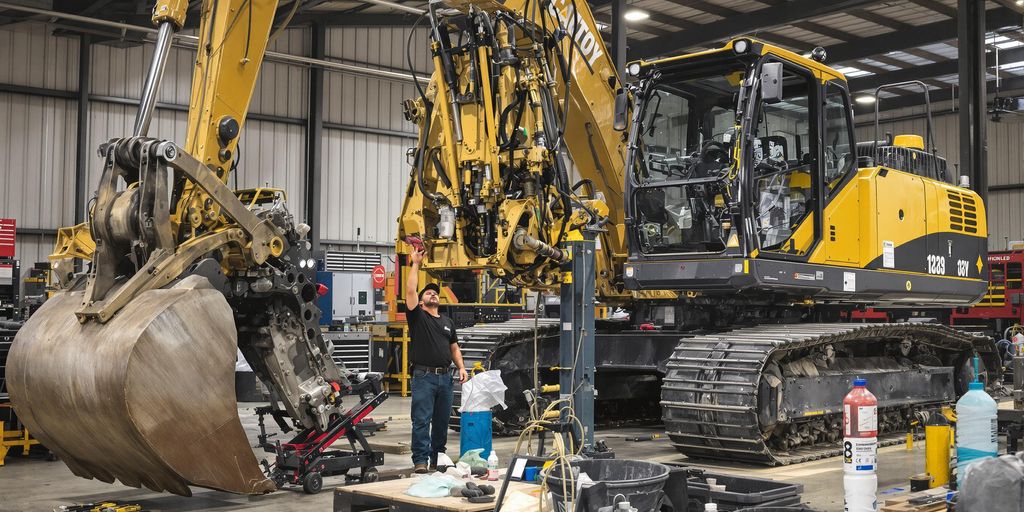
Balancing Maintenance and Operational Downtime
Finding the right balance between keeping your equipment running and scheduling maintenance is a challenge. Over-maintaining can waste time and resources, while neglecting it can lead to costly breakdowns. A great way to strike this balance is by using historical data and manufacturer guidelines to plan maintenance during off-peak times. This ensures minimal disruption to your operations while keeping machines in top shape.
Seasonal Maintenance Considerations
Different times of the year may demand specific maintenance tasks. For example, heavy equipment used in cold climates might need antifreeze checks or extra lubrication during winter. On the flip side, summer might call for additional cooling system checks. Creating a seasonal checklist tailored to your equipment's needs can help avoid surprises.
Customizing Schedules for Different Equipment Types
Not all machines have the same needs. A bulldozer will require different maintenance intervals compared to a crane or excavator. Grouping equipment by type and assigning tailored schedules ensures each gets the right care without overcomplicating the process. A simple chart like the one below can help:
Thoughtful planning and regular reviews of your maintenance schedule will save time, money, and extend your equipment's life.
The Impact of Quality Parts and Consumables on Equipment Life
Choosing High-Quality Replacement Parts
When it comes to heavy equipment, using quality replacement parts isn't just a luxury—it's a necessity. Inferior parts can lead to frequent breakdowns, costing you more in the long run. High-quality parts ensure that your machinery runs smoothly and reduces the risk of unexpected failures. Look for parts that meet or exceed the manufacturer's specifications. This guarantees compatibility and durability.
- Check for warranties on parts to ensure their reliability.
- Always source replacement parts from trusted suppliers.
- Avoid "universal" parts that claim to fit multiple machines; they rarely perform as well as machine-specific components.
Managing Consumable Inventory Effectively
Consumables like filters, belts, and tires might seem minor, but they play a huge role in keeping equipment operational. Keeping an organized inventory prevents downtime caused by missing or worn-out consumables. Here’s how to manage your stock effectively:
- Regularly audit your inventory to avoid overstocking or shortages.
- Use software to track usage patterns and predict when replacements are needed.
- Store consumables in a clean, dry area to prevent unnecessary wear or damage.
A well-maintained inventory ensures that you always have what you need when you need it.
Cost-Benefit Analysis of Bulk Purchases
Buying in bulk can save money, but it’s not always the best approach. Conduct a cost-benefit analysis before committing to large purchases. While bulk buying reduces the cost per unit, it can also lead to overstocking and storage issues. Here’s a simple breakdown:
Smart purchasing decisions not only save money but also ensure that your equipment gets the best care possible. Always balance immediate savings with long-term usability.
By focusing on quality parts and consumables, you’re not just maintaining your equipment—you’re investing in its future. This approach minimizes downtime, reduces repair costs, and ultimately extends the life of your machines.
Leveraging Technology for Advanced Maintenance Management
Benefits of Maintenance Management Software
Maintenance management software is no longer a luxury—it’s a necessity. These tools help organize and streamline maintenance tasks, saving time and cutting down on errors. With computerized maintenance management systems (CMMS), you can:
- Track equipment history: Know exactly when each machine was last serviced.
- Schedule tasks efficiently: Avoid overlapping maintenance and operational hours.
- Monitor warranties: Quickly pull up warranty data when needed.
Using Data Analytics for Predictive Maintenance
Forget about rigid maintenance schedules. Predictive maintenance uses analytics to tell you when a machine actually needs servicing. This kind of data-driven approach can:
- Reduce unnecessary downtime.
- Save money on labor and parts.
- Extend the life of your equipment.
For instance, analytics might show that a bulldozer in harsh conditions needs servicing more frequently than one in a controlled environment. Smart, right?
Integrating IoT in Heavy Equipment Maintenance
The Internet of Things (IoT) is making maintenance smarter. Sensors on machines can send real-time data to your CMMS, flagging problems before they escalate. Here’s how IoT is changing the game:
- Real-time monitoring for wear and tear.
- Instant alerts for unusual activity.
- Data collection for long-term performance trends.
Pro Tip: Pair IoT with advanced operator training to get the most out of your high-tech equipment. The more your team knows, the better they can use these tools.
Safety and Compliance Through Regular Maintenance
Ensuring Workplace Safety with Well-Maintained Equipment
Keeping heavy equipment in good shape isn’t just about saving money or avoiding downtime—it’s also about protecting your team. A well-maintained machine is far less likely to malfunction and cause accidents. Regular checks can catch issues like worn-out brakes, faulty hydraulic lines, or non-functional safety mechanisms before they become hazards.
Some key areas to inspect include:
- Hydraulic fluid levels and hose fittings.
- Frayed wiring or loose electrical connections.
- Proper functioning of controls and safety systems.
- Chain or belt tension and visible structural damage.
By addressing these issues daily, you reduce risks not only to workers but also to the equipment itself.
Meeting Industry Standards and Regulations
Staying compliant with industry rules isn’t optional—it’s mandatory. Regular maintenance ensures that your equipment meets the required safety and operational standards. Neglecting compliance can lead to fines, legal troubles, or worse, workplace accidents.
To stay on top of regulations:
- Follow manufacturer-recommended maintenance schedules.
- Keep detailed records of all inspections and repairs.
- Train operators and technicians on compliance requirements.
This approach not only keeps your fleet in line with legal standards but also boosts your company’s reputation for safety.
Reducing Risks of Equipment Failure
Equipment that breaks down unexpectedly can cause chaos on a job site. Worse, a major failure could lead to serious injuries or property damage. Regular maintenance minimizes these risks by catching problems early. For example, a simple daily inspection can reveal:
- Low brake fluid levels.
- Damaged tracks or tires.
- Non-functional alarms or lights.
Preventing failure is always easier—and cheaper—than dealing with the aftermath of a breakdown.
By making maintenance a priority, you’re not just extending equipment life; you’re creating a safer, more reliable workplace for everyone involved.
Conclusion
Taking care of heavy equipment isn’t just about keeping things running smoothly—it’s about making sure your investment lasts. By sticking to a solid maintenance plan, training your team, and staying on top of small issues before they grow, you can save time, money, and a lot of headaches. Remember, well-maintained machines not only perform better but also keep your workplace safer. So, whether it’s regular inspections or proper operator training, every little effort counts. Start today, and your equipment will thank you tomorrow.
Frequently Asked Questions
Why is preventive maintenance important for heavy equipment?
Preventive maintenance helps catch small issues before they become big problems. It can save money, reduce downtime, and make your equipment last longer.
What are the benefits of training equipment operators?
Training operators improves safety, reduces mistakes, and ensures the equipment is used correctly. This can extend the machine's life and boost productivity.
How often should heavy equipment be inspected?
Daily inspections are ideal. Regular checks help identify wear and tear early, keeping the equipment in good working condition.
What are some examples of common maintenance tasks?
Common tasks include checking fluid levels, inspecting tires, cleaning filters, and tightening loose bolts. These small steps can prevent bigger issues.
How does technology help with equipment maintenance?
Technology like maintenance software and IoT devices can track performance, predict issues, and schedule repairs, making maintenance more efficient.
What should I look for when buying replacement parts?
Always choose high-quality parts that match the manufacturer’s recommendations. Cheaper parts might save money upfront but can lead to costly repairs later.