Exploring Innovative Technology Trends in Industrial Equipment for 2024
.png)
In 2024, the world of industrial equipment is buzzing with fresh tech trends. From robots that can do more than ever before to AI that's changing how we maintain and optimize machinery, the industry is on a roll. The Industrial Internet of Things (IIoT) is making it easier to keep tabs on equipment in real-time, while 3D printing is speeding up production like never before. And let's not forget the push towards using cleaner energy in machines, making them friendlier to our planet. As these innovations unfold, they're not just reshaping factories but also the very nature of industrial work itself.
Key Takeaways
- Robotics and automation are transforming industrial processes, making them faster and more efficient.
- AI is revolutionizing maintenance and quality control, leading to smarter and more reliable equipment.
- IIoT is enabling real-time monitoring, improving decision-making and operational efficiency.
- 3D printing is reducing costs and time in manufacturing, offering new possibilities for design and production.
- Clean energy solutions are becoming more prevalent, reducing the environmental impact of industrial equipment.
Embracing Robotics and Automation
Robots are no longer just a futuristic concept; they're here and changing how industries work. In manufacturing, robots are addressing age-old problems like inefficiency and human error. Their precision and ability to adapt to different tasks have made them indispensable. Robots can work around the clock, ensuring consistent quality and reducing defects. With sensors and cameras, they enhance safety by detecting potential hazards, allowing them to swiftly respond and avoid accidents. This ability to function continuously is a game-changer, especially for meeting tight deadlines and handling large workloads with minimal human interaction.
Automation in Smart Factories
Smart factories are leading the way in automation. These factories use cutting-edge technology to operate with minimal human intervention. Imagine a factory that can run in the dark because it doesn't need people to be present. That's what automation is achieving. It's not just about replacing human labor; it's about creating a seamless environment where machines and humans work together to boost productivity. Automation reduces labor costs and improves workplace safety, making it a win-win for both manufacturers and workers.
Impact on Labor and Efficiency
The rise of automation and robotics is reshaping the workforce. While some fear that robots will take over jobs, the reality is different. Automation is creating new opportunities for workers to engage in more meaningful and less repetitive tasks. It allows employees to focus on areas that require creativity and problem-solving skills. A recent survey of manufacturers in Europe and North America highlights the growing embrace of these technologies, showing that companies are optimistic about the future. By improving efficiency, robots and automation are helping industries stay competitive in a rapidly changing market.
The integration of robotics and automation is not about replacing humans but enhancing their capabilities. Workers can now focus on tasks that truly require human insight, making industries more innovative and forward-thinking.
Harnessing the Power of Artificial Intelligence
AI-Driven Predictive Maintenance
Artificial Intelligence (AI) is changing how industrial equipment is maintained. Machines can now predict when they'll need service before something breaks down. This means fewer unexpected stops and a smoother operation. Companies like Sarox are leading the way with tools that keep machines running by spotting problems early. Using AI, they can analyze machine data in real-time, helping businesses avoid costly downtime.
- Predictive maintenance reduces unexpected breakdowns.
- Early fault detection saves money and time.
- Real-time data analysis ensures continuous operation.
Enhancing Quality Control with AI
Quality control is another area where AI is making a big impact. AI systems can inspect products faster and more accurately than humans. This ensures that only the best products make it to the market. By using AI, companies can maintain high standards and reduce waste. For instance, Siemens has integrated AI-powered machine vision solutions to enhance quality checks in their production lines.
AI in Supply Chain Optimization
AI is also helping to streamline supply chains. It can predict demand, manage inventory, and even optimize delivery routes. This means products get to where they need to be more efficiently. AI can analyze vast amounts of data to make supply chains more responsive and resilient. As a result, companies can reduce costs and improve customer satisfaction.
AI is not just a tool; it's becoming a partner in industrial operations. By predicting maintenance needs, ensuring product quality, and optimizing supply chains, AI is proving to be a game-changer in the industry. As we move into 2024, the role of AI in manufacturing will only continue to grow, offering exciting possibilities for companies ready to embrace this technology.
The Rise of IIoT-Enabled Equipment
Industrial Internet of Things (IIoT) is transforming how we monitor machinery and processes. By embedding sensors into equipment, IIoT enables real-time data collection and analysis, giving businesses immediate feedback on operations. This connectivity allows for optimized operations, reduced energy consumption, and improved overall equipment effectiveness (OEE). The ability to monitor and control equipment remotely is especially valuable for industries with widespread operations.
Benefits of IIoT in Industrial Equipment
- Enhanced Transparency: IIoT provides greater visibility into operations, allowing for remote monitoring and control.
- Regulatory Compliance: Automates data collection and reporting, helping industries adhere to standards.
- Operational Efficiency: Real-time insights improve the agility and responsiveness of machines.
Challenges in IIoT Implementation
While IIoT offers numerous benefits, integrating it into existing systems can be challenging. Compatibility with current infrastructure, data security concerns, and the need for skilled personnel to manage and interpret data are significant hurdles. Additionally, ensuring reliable connectivity in remote or harsh environments can pose a challenge. However, advancements in key industrial IoT trends, such as edge computing and AI, are helping to address these issues, paving the way for broader adoption of IIoT.
3D Printing Revolutionizing Manufacturing
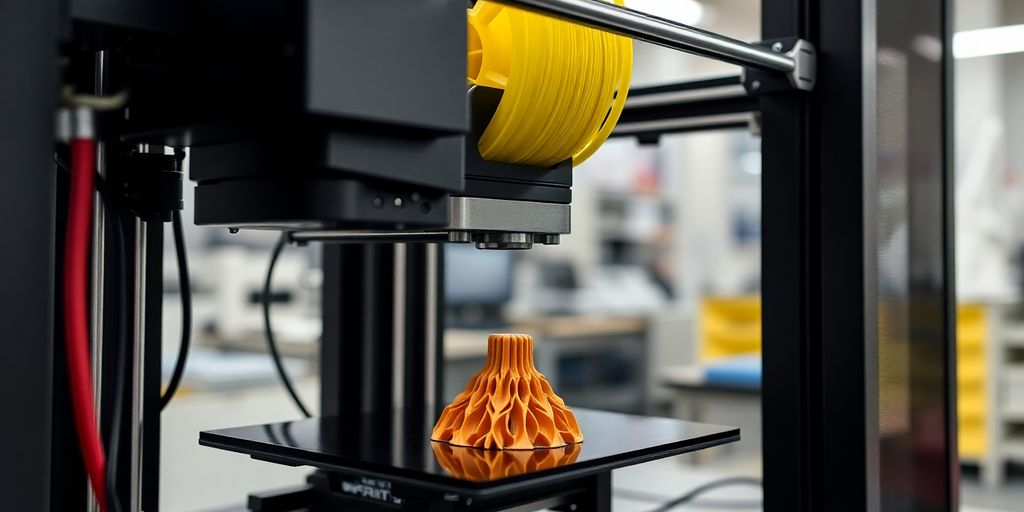
Applications of 3D Printing in Industrial Equipment
3D printing is changing how industrial equipment is made. It allows for the creation of complex parts directly from digital files, without the need for traditional molds or machining. This means custom parts can be made quickly and at a lower cost. Industries like aerospace and automotive are using 3D printing to make lightweight parts that improve fuel efficiency. Plus, the flexibility of 3D printing means that designs can be easily modified to fit specific needs.
Cost and Time Efficiency with 3D Printing
3D printing can be a game-changer for reducing costs and saving time. Traditional manufacturing often involves several steps and a lot of material waste. But with 3D printing, materials are used more efficiently, and parts are made layer by layer, which cuts down on waste. This process not only speeds up production but also lowers the overall cost. Companies can produce parts on demand, avoiding the need for large inventories and reducing storage costs.
Future Prospects of 3D Printing
The future of 3D printing looks promising, with ongoing advancements in materials and technology. Innovations in 3D printing technology are focusing on sustainable materials and improved techniques, which could further enhance efficiency and creativity in manufacturing. As technology evolves, 3D printing might become even more integrated into the production process, allowing for greater customization and faster prototyping. The potential for using recyclable and bio-based materials also supports a more sustainable manufacturing approach.
The shift towards 3D printing in manufacturing signifies a move towards more efficient, customizable, and sustainable production methods. This technology not only addresses current manufacturing challenges but also opens up new possibilities for the future.
Sustainable Solutions with Clean Energy Machines
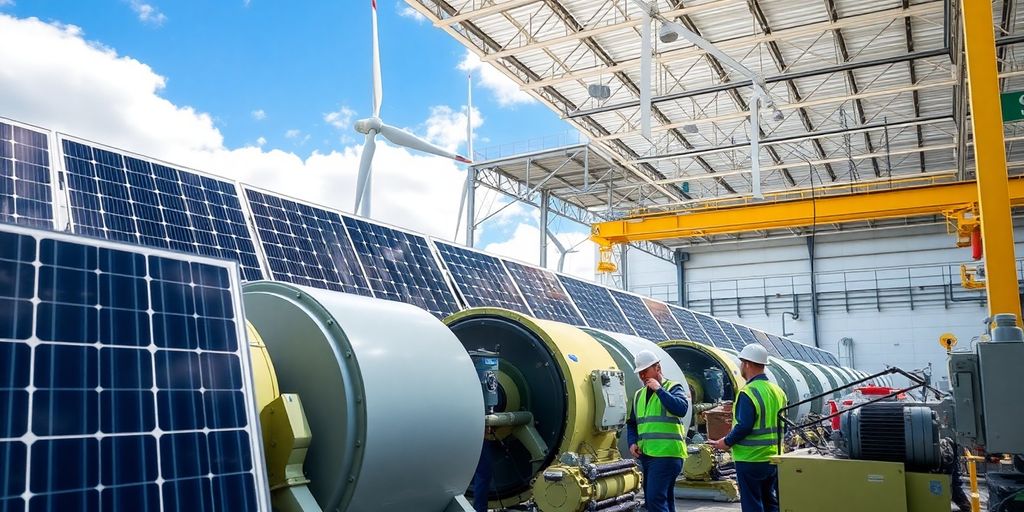
Adoption of Renewable Energy in Industrial Equipment
Switching to clean energy machines is becoming a big deal in the industrial world. Wind and solar photovoltaic (PV) energy are at the forefront, producing more electricity than traditional sources like hydropower. By 2025, renewables are set to outshine coal, marking a major shift. These machines help cut down the carbon footprint of factories, making them not just greener but also cheaper to run. They’re quieter too, which means less noise pollution, and they offer precise control and quick response times, making manufacturing more accurate and efficient.
Reducing Carbon Footprint with Clean Energy
Going green in industrial settings isn't just about looking good; it's about doing good. Clean energy machines, powered by renewables like wind and solar, are a big step in slashing emissions. They’re more energy-efficient, which means factories save on costs while using fewer resources. Plus, these machines are adaptable, easily fitting in with new tech, which makes them a smart choice for future-proofing industrial operations.
Innovations in Energy-Efficient Machinery
The future of industrial equipment is all about innovation. Electric machines offer a sustainable alternative to the traditional, noisy, and resource-heavy counterparts. They not only cut down on energy use but also integrate seamlessly with other smart technologies. This means better efficiency and lower costs in the long run. As we move forward, these machines will play a crucial role in reshaping the industrial landscape, making it cleaner and more efficient.
Augmented and Virtual Reality in Industrial Settings
Training and Simulation with AR/VR
In the industrial world, training can be a risky endeavor. But with Virtual Reality making waves in 2024, it's getting a whole lot safer. Imagine being able to train on complex machinery without the fear of breaking something or getting hurt. That's what VR brings to the table. Workers can dive into a virtual environment where they can practice operating and maintaining equipment without any real-world consequences. It's like a video game, but for serious business.
On the flip side, Augmented Reality (AR) adds a layer of digital information to the real world. Picture a technician looking at a machine through AR glasses and seeing step-by-step instructions hovering over the parts they need to fix. This real-time guidance can drastically cut down on errors and speed up the learning process.
AR/VR for Equipment Maintenance
When it comes to keeping machines running smoothly, AR and VR are game-changers. AR can provide on-the-spot troubleshooting by overlaying diagnostic data directly onto the equipment. This makes it easier for workers to identify issues and perform repairs, even if they're not experts. Meanwhile, VR can simulate maintenance scenarios, allowing technicians to practice and perfect their skills in a controlled setting before they tackle the real thing.
AR and VR also enable remote assistance, which is a big deal in today's globalized world. Experts can guide technicians through repairs from miles away, seeing exactly what they see and providing real-time advice. This not only saves time and travel costs but also ensures that machines are fixed correctly the first time around.
Future Trends in AR/VR Technology
Looking ahead, the potential for AR and VR in industrial settings is huge. As technology continues to evolve, we can expect even more immersive and intuitive experiences. Imagine AR glasses that are as comfortable as regular eyewear, or VR simulations that are indistinguishable from reality. These advancements will make AR and VR even more accessible and effective tools for training, maintenance, and beyond.
Moreover, the integration of AI with AR and VR could open up new possibilities. AI could analyze data from VR training sessions to provide personalized feedback, or enhance AR overlays with predictive insights. As these technologies continue to converge, the line between the physical and digital worlds will blur even further, creating exciting opportunities for innovation in the industrial sector.
The rise of AR and VR in industry isn't just about flashy new gadgets. It's about creating safer, more efficient, and more connected workplaces. As these technologies become more widespread, they'll transform the way we train, maintain, and interact with industrial equipment, paving the way for a smarter future.
Enhancing Cybersecurity in Industrial Equipment
Addressing Cyber Threats in Industrial Systems
In today's interconnected world, industrial systems are more vulnerable to cyber threats than ever. With the rise of the Industrial Internet of Things (IIoT) and smart manufacturing, the attack surface has expanded significantly. Effective cybersecurity measures are crucial to protect sensitive data and maintain operational integrity. Companies need to focus on both hardware and software solutions to shield against potential cyber attacks. This includes deploying advanced encryption, multi-factor authentication, and regular system patching.
Implementing Robust Security Protocols
Implementing robust security protocols is not just about defense; it's about creating a resilient industrial environment. Here’s a basic checklist:
- Conduct regular security audits to identify vulnerabilities.
- Integrate cybersecurity into engineering and procurement processes to reduce risks associated with supply chain vulnerabilities.
- Establish backup and disaster recovery plans to ensure quick recovery in case of an attack.
These steps help maintain trust with stakeholders and ensure compliance with regulatory standards.
The Role of AI in Cybersecurity
AI is playing an increasingly important role in cybersecurity. By leveraging machine learning algorithms, AI can detect anomalies and potential threats much faster than traditional methods. This proactive approach allows for real-time monitoring and response, significantly reducing the risk of breaches. AI-driven systems can also adapt to new threats, providing a dynamic defense mechanism that evolves with the threat landscape.
As industrial systems become more integrated and complex, the need for a comprehensive cybersecurity strategy becomes even more critical. Organizations must prioritize cybersecurity to protect their assets and ensure the safe and efficient operation of their equipment.
Leveraging Industrial Cloud Computing
Cloud Solutions for Data Management
In today's fast-paced industrial world, managing massive amounts of data is a real challenge. Industrial cloud computing steps up as a game-changer, offering a centralized platform to gather, store, and analyze data in real-time. This means no more data silos and a huge leap toward insightful analytics and predictive maintenance. Companies can customize cloud resources to fit their needs without breaking the bank on traditional IT infrastructure. Plus, with robust security measures, sensitive data is kept safe, shielding it from potential cyber threats.
Improving Collaboration with Cloud Technology
Cloud computing isn't just about data storage; it's also about connecting people and systems. With cloud platforms, teams across different locations can collaborate seamlessly, sharing data and insights instantly. This connectivity fosters innovation and speeds up decision-making processes. Imagine engineers in different parts of the world working together on the same project, accessing the same data, and making real-time updates. It's like having a virtual office that never closes.
Scalability and Flexibility of Cloud Services
One of the biggest perks of cloud services is their scalability. As businesses grow, their data needs change, and cloud platforms can easily adjust to these demands. There's no need to invest in new hardware or worry about outdated systems. Cloud services offer the flexibility to scale up or down, depending on the current needs. This adaptability ensures that companies can focus on their core operations without worrying about IT constraints.
"Industrial cloud computing is not just about technology; it's about transforming how businesses operate. By centralizing data and enabling collaboration, it paves the way for a more efficient and connected industrial landscape."
Wrapping Up: The Future of Industrial Equipment
So, there you have it. The industrial equipment scene is buzzing with fresh ideas and tech upgrades. From robots to clean energy, the changes are coming fast and furious. It's not just about keeping up anymore; it's about staying ahead. Companies diving into these trends are setting themselves up for a future that's not just about survival but thriving. As we look to 2024 and beyond, it's clear that innovation isn't slowing down. Whether you're in the game or just watching from the sidelines, it's an exciting time to be part of this industry. Keep an eye out, because the next big thing might just be around the corner.
Frequently Asked Questions
What are the main trends in industrial equipment for 2024?
In 2024, industrial equipment trends include robotics and automation, AI-driven processes, IIoT-enabled equipment, 3D printing, sustainable energy solutions, augmented and virtual reality, enhanced cybersecurity, and industrial cloud computing.
How is AI used in industrial equipment?
AI is used in industrial equipment for predictive maintenance, improving quality control, and optimizing supply chains. It helps machines learn from data to make better decisions and increase efficiency.
What is the impact of robotics on factories?
Robotics in factories speeds up production, reduces errors, and helps in handling repetitive tasks. This makes factories more efficient and frees up workers for more complex jobs.
How does 3D printing benefit manufacturing?
3D printing allows for quick prototyping and production, saving time and costs. It enables manufacturers to create complex parts on-demand and reduces waste.
What is IIoT and how does it help industries?
IIoT stands for Industrial Internet of Things. It connects machines and devices to the internet, allowing real-time monitoring and data analysis. This helps industries improve efficiency and predict equipment failures.
Why is cybersecurity important in industrial equipment?
Cybersecurity is crucial to protect industrial systems from cyber threats. With more equipment connected to the internet, robust security measures are needed to prevent data breaches and ensure safe operations.