Essential Heavy Equipment Safety Tips for Operators
.png)
When it comes to operating heavy machinery, safety should always come first. Heavy equipment can be dangerous if not handled properly, so it's crucial for operators to be well-informed about safety practices. This article outlines some essential heavy equipment safety tips for operators to help keep everyone safe on the job site. Whether you're new to the field or an experienced operator, these guidelines will ensure that you and your team are protected while working with heavy machinery.
Key Takeaways
- Always inspect equipment before starting work to catch any issues early.
- Make sure operators are trained on both general safety and specific equipment.
- Stay aware of your surroundings to avoid hazards and keep everyone safe.
- Wear the right personal protective equipment to minimize injury risks.
- Follow manufacturer guidelines to use equipment safely and effectively.
Conduct Thorough Equipment Inspections
It's easy to overlook the importance of a good inspection, but trust me, it's worth the time. I've seen firsthand how a quick check can prevent major headaches down the road. Regular inspections are the first line of defense against accidents and equipment failure.
Inspect Equipment Before Use
Before you even think about firing up that engine, take a walk around. Seriously, do it. Check for anything that looks out of place – loose parts, leaks, or damage. Fluid levels are a big one; make sure your oil, coolant, and hydraulic fluid are where they need to be. It's like giving your equipment a quick physical before a big game. Catching small issues early can save you from big problems later. I usually start with a ground-level walkaround, looking for anything obvious. Then, I climb up and check the controls, making sure everything moves smoothly and responds correctly. Don't skip this step – it's a lifesaver.
Check Safety Features
Alright, so you've done the basic inspection. Now, let's talk safety. Are your lights working? How about the horn and backup alarms? These aren't just there to annoy people; they're essential for preventing accidents. Make sure all guards and shields are in place and functioning properly. Test the brakes and steering to ensure they're responsive. If anything seems off, don't ignore it. Get it fixed before you start working. I remember one time, the backup alarm on a loader wasn't working, and someone almost got seriously hurt. It's not worth the risk.
Review Operational Manuals
Okay, I know what you're thinking: "Manuals? Who reads those?" But hear me out. Those manuals are packed with important information about your equipment, including safety procedures, maintenance schedules, and troubleshooting tips. Take some time to familiarize yourself with the manual for each piece of equipment you operate. Pay attention to the recommended operating procedures and any specific warnings or cautions. It might seem boring, but it could save your life. I keep a copy of the manual in the cab for quick reference. You can also request an electronic copy for easy access on a smartphone or tablet.
Ignoring the operational manual is like trying to assemble furniture without instructions. You might get it done eventually, but you're probably going to mess something up along the way. The manual is there to help you operate the equipment safely and efficiently. Don't be afraid to use it.
Prioritize Operator Training
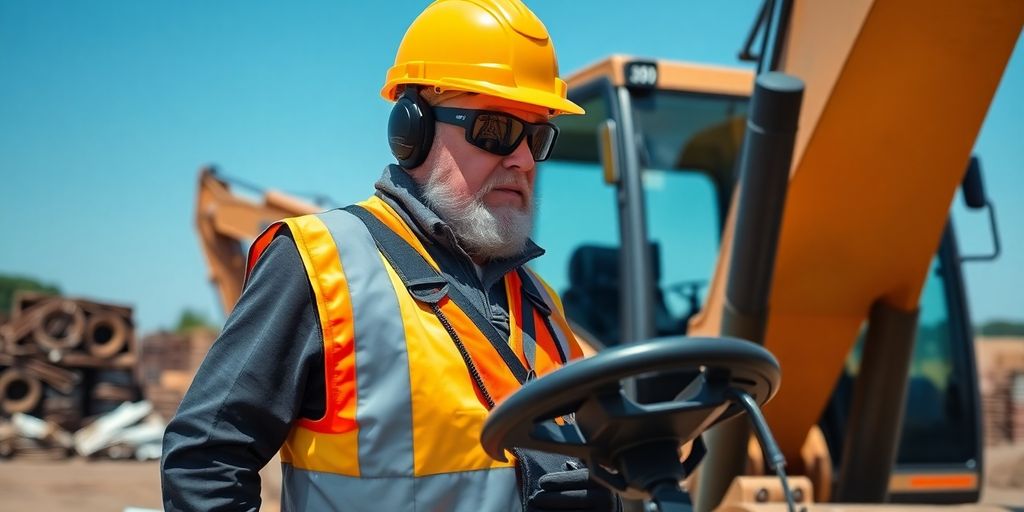
Operating heavy equipment isn't something you can just jump into. It demands a solid understanding of the machinery and safety protocols. Proper training is essential to prevent accidents and ensure everyone on the job site goes home safe. It's not just about knowing how to move the levers; it's about understanding the equipment's limitations, potential hazards, and emergency procedures.
Provide Comprehensive Training
Good training programs should cover everything from basic operation to advanced troubleshooting. This includes classroom instruction, hands-on practice, and simulations. Operators need to learn about equipment mechanics, safety features, load capacities, and emergency shutdown procedures. A well-rounded program will also address site-specific hazards and best practices.
Conduct Regular Refresher Courses
Even experienced operators benefit from refresher courses. Things change – new equipment, updated safety regulations, and evolving best practices. Regular training helps keep skills sharp and reinforces safe habits. It's easy to get complacent, so these courses are a good way to stay on top of things. Plus, it's a good opportunity to discuss any near misses or incidents and learn from them.
Ensure Equipment-Specific Training
Not all heavy equipment is created equal. A bulldozer is different from an excavator, which is different from a crane. Operators need training specific to the equipment they'll be using. This includes understanding the unique controls, capabilities, and limitations of each machine. Generic training is a start, but equipment-specific instruction is where the real learning happens.
Training isn't a one-time thing; it's an ongoing process. The more prepared your operators are, the safer and more productive your job site will be. Investing in training is investing in the well-being of your crew and the success of your projects.
Maintain Awareness of Surroundings
Operating heavy equipment isn't just about knowing the controls; it's about being completely aware of everything happening around you. This means constantly scanning your environment, anticipating potential hazards, and communicating effectively with everyone on the site. It's easy to get tunnel vision when you're focused on a task, but that's when accidents happen.
Identify Potential Hazards
Before you even start the engine, take a walk around the equipment. Look for anything that could pose a risk: overhead power lines, uneven terrain, underground utilities, other vehicles, and of course, people. Underground utilities are a big one – hitting a gas line or electrical cable can have catastrophic consequences. Make sure they're clearly marked. Also, be aware of the weather. Rain, snow, or fog can significantly reduce visibility and make surfaces slippery.
Establish Safe Zones
Ideally, you want to create a buffer zone around your equipment where no one is allowed to enter while it's in operation. Use barriers, cones, or tape to clearly mark these safe zones. If that's not possible, make sure everyone on the site knows the equipment's swing radius and keeps a safe distance. Communication is key here. Let people know what you're doing and where you're going.
Communicate with Ground Personnel
Communication is paramount. Hand signals, two-way radios, or even just a clear line of sight can prevent accidents. A spotter is invaluable, especially when backing up or operating in tight spaces. They can guide you around obstacles and alert you to the presence of workers or pedestrians you might not be able to see. Make sure your spotter is wearing high-visibility clothing and that you both understand the agreed-upon signals.
It's easy to become complacent on a familiar job site, but that's when accidents are most likely to occur. Stay vigilant, communicate clearly, and never assume that others are aware of your presence. Your awareness could save a life.
Here's a quick reminder of key communication methods:
- Hand Signals: Standardized signals for common movements.
- Two-Way Radios: Clear communication, especially over distances.
- Visual Contact: Maintain eye contact when possible.
- Audible Signals: Horn or backup alarms (but don't rely solely on these).
Utilize Personal Protective Equipment
Okay, so PPE. It's not just some suggestion, it's essential. You wouldn't believe how many injuries could be avoided if people just wore the right gear. Think of it as your personal force field against workplace hazards.
Wear Appropriate Gear
Hard hats, safety glasses, gloves, steel-toed boots, reflective vests – the list goes on. The right PPE depends on the job, obviously. Operating a jackhammer? You'll need hearing protection. Welding? You'll need a welding helmet and gloves. Make sure everything fits properly and is in good condition. Don't be that person wearing a hard hat that's three sizes too big.
Understand PPE Limitations
PPE isn't a magic shield. It reduces risk, but it doesn't eliminate it. A hard hat can protect you from falling objects, but it won't save you from everything. Know what your PPE can and can't do. For example, those gloves might protect you from minor cuts, but they won't stop a saw blade.
Regularly Inspect PPE
Don't just grab your gear and go. Take a minute to check it over. Look for cracks, tears, or any other damage. A damaged hard hat is about as useful as a paper bag in a rainstorm. Replace anything that's worn out or broken. It's a small investment that can save you a lot of pain (and money) down the road.
PPE is your last line of defense. It's there to protect you when other safety measures fail. Don't take it for granted. Treat it with respect, and it will do its job.
Practice Safe Entry and Exit Procedures
It's easy to overlook the simple act of getting in and out of heavy equipment, but it's a surprisingly common source of injuries. Rushing, not paying attention, or using improper techniques can lead to slips, falls, and strains. Let's break down how to do it right.
Maintain Three-Point Contact
Always maintain three points of contact when entering or exiting equipment. This means having two hands and one foot, or two feet and one hand, in contact with the machine at all times. This 3-point rule provides stability and reduces the risk of falling, especially on uneven or slippery surfaces.
Use Designated Steps and Handholds
Heavy equipment is designed with specific steps and handholds to facilitate safe entry and exit. Don't take shortcuts by climbing on tires, tracks, or other parts of the machine not intended for this purpose. These areas can be unstable or slippery, increasing the risk of an accident. Make sure to inspect the steps and handholds regularly for any damage or debris that could make them unsafe.
Avoid Climbing on Equipment
Never jump off equipment. It's a quick way to injure yourself. Always face the machine when entering or exiting, and use the steps and handholds provided. If you need to carry something with you, use a rope or have someone hand it to you once you're safely on the machine. Keep your hands free to maintain that crucial three-point contact.
Taking a few extra seconds to enter and exit equipment safely can prevent serious injuries. It's a small investment of time that can make a big difference in your overall safety and well-being on the job site.
Follow Manufacturer Guidelines
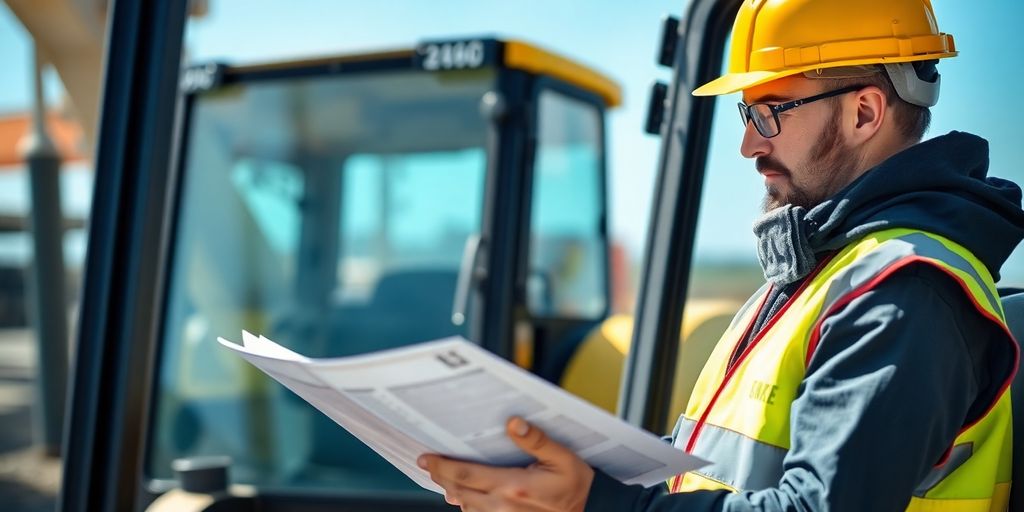
It's easy to think you know best, especially if you've been operating heavy equipment for years. But ignoring the manufacturer's guidelines is a recipe for disaster. These guidelines aren't just suggestions; they're based on extensive testing and engineering to ensure the equipment operates safely and efficiently. Let's break down why sticking to the manual is so important.
Use Equipment as Intended
Every piece of heavy equipment is designed for specific tasks. Using a machine for something it wasn't intended for can lead to equipment failure, accidents, and injuries. For example, trying to use an excavator as a makeshift crane is a terrible idea. It might seem like a quick fix, but the excavator's hydraulics and structural integrity aren't designed for that kind of stress. Always use the right tool for the job. If you're unsure, check the manufacturer's specifications or contact us for clarification.
Adhere to Load Capacities
Overloading equipment is a common cause of accidents. Each machine has a maximum load capacity that should never be exceeded. This limit is determined by the equipment's design and the materials it's made from. Exceeding the load capacity can cause the machine to become unstable, leading to tip-overs or structural failures. It can also damage the equipment's components, leading to costly repairs. Always know the load capacity of your equipment and ensure you never exceed it.
Avoid Modifications
Modifying heavy equipment might seem like a good way to customize it for your specific needs, but it can have serious consequences. Unauthorized modifications can void warranties, compromise the equipment's safety features, and even alter its performance in unpredictable ways. Manufacturers design their equipment to work as a system, and changing one part can affect the entire machine. If you need to make changes, consult with the manufacturer or a qualified engineer to ensure the modifications are safe and don't compromise the equipment's integrity.
Think of it like this: manufacturers spend countless hours designing and testing their equipment. They know what it can and can't do. Ignoring their guidelines is like ignoring the advice of an expert. It might seem like you're saving time or money in the short run, but you're likely to pay for it in the long run with accidents, injuries, or equipment damage.
Implement Safe Operating Practices
Operating heavy equipment isn't just about knowing how the machine works; it's about doing things the right way, every time. It's easy to get complacent, especially when you're doing the same tasks day in and day out, but that's when accidents happen. Let's talk about some key practices to keep in mind.
Stay Alert and Focused
This might sound obvious, but it's super important. Operating heavy equipment requires your full attention. Being tired or not fully engaged can lead to mistakes. Make sure you're well-rested and mentally prepared before you start your shift. If you're feeling unwell, it's better to take a break. It's not worth risking your safety or the safety of others.
Avoid Distractions
Distractions are a big no-no. That means no texting, no phone calls (unless it's work-related and hands-free), and no daydreaming. Keep your mind on the task at hand. If something is bothering you, deal with it during a break, not while you're operating machinery. Focus is key.
Use Spotters for Visibility
Heavy equipment often has blind spots, and that's where spotters come in. A spotter is someone who helps guide you, especially when you're backing up or maneuvering in tight spaces. They should be trained in hand signals and wear high-visibility clothing. Make sure you communicate clearly with your spotter before starting any operation. It's a simple step that can prevent serious accidents.
Having a spotter can make a huge difference, especially in busy or confined areas. They act as your eyes and ears, helping you avoid obstacles and keep everyone safe. It's a team effort, and clear communication is essential.
Here's a quick rundown of common hand signals:
- Stop: Arm raised with palm facing outward.
- Forward: Arm extended forward, palm up, making a pushing motion.
- Backward: Arm extended backward, palm down, making a pulling motion.
- Left/Right: Arm extended to the side, pointing in the direction of travel.
Wrapping It Up: Safety First
In the end, keeping safety at the forefront when operating heavy equipment is a must. It’s not just about following rules; it’s about protecting yourself and your coworkers. Remember to inspect your gear, stay aware of your surroundings, and always wear your personal protective equipment. Training is key, so make sure everyone knows what they’re doing before they jump in the cab. Heavy machinery can be dangerous, but with the right precautions, you can help create a safer work environment. So, take these tips to heart, and let’s keep those job sites accident-free!
Frequently Asked Questions
What should I check during an equipment inspection?
Before using heavy equipment, check for any leaks, loose parts, and fluid levels. Make sure all safety features are working.
Why is operator training important?
Training helps operators understand how to use equipment safely and avoid accidents. It's essential for everyone, from beginners to experienced operators.
What is personal protective equipment (PPE)?
PPE includes gear like hard hats, gloves, and safety glasses that protect workers from injuries while operating equipment.
How can I stay aware of my surroundings while operating?
Always look out for obstacles, other workers, and equipment around you. Use spotters to help with visibility.
What are safe entry and exit procedures for equipment?
Always maintain three points of contact when getting in or out of the machine, and use the designated steps and handholds.
Why should I follow manufacturer guidelines?
Manufacturer guidelines ensure that equipment is used safely and effectively, which helps prevent accidents and damage.