Common Heavy Equipment Repairs and How to Avoid Them
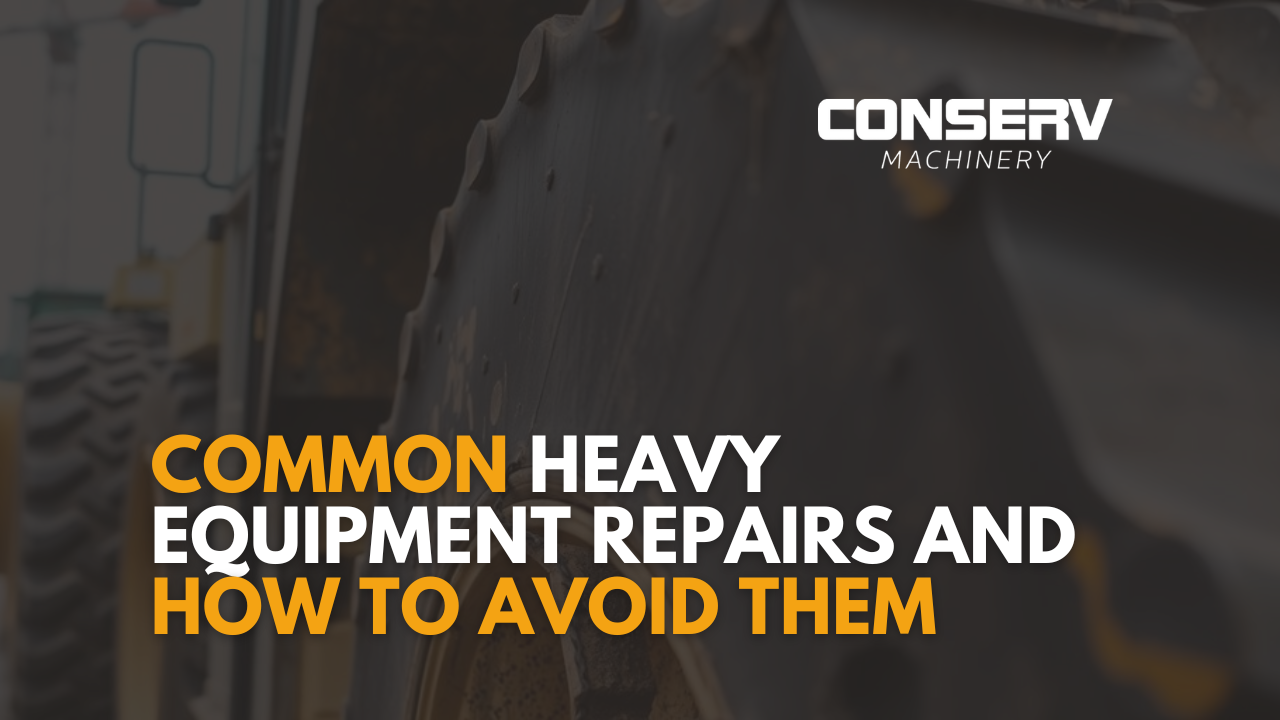
Heavy equipment is essential in many industries like construction and mining. However, these machines can face common issues that lead to costly repairs and downtime. Understanding these problems and how to prevent them can save you time and money. In this article, we will explore the frequent repairs needed for heavy equipment and share tips on how to avoid them.
Key Takeaways
- Regular maintenance is key to preventing equipment failures.
- Operator training can reduce the risk of accidents and damage.
- Scheduled inspections can catch small issues before they escalate.
- Pay attention to hydraulic and electrical system care to avoid major breakdowns.
- Utilizing technology can help monitor equipment health and predict maintenance needs.
Understanding Common Heavy Equipment Failures
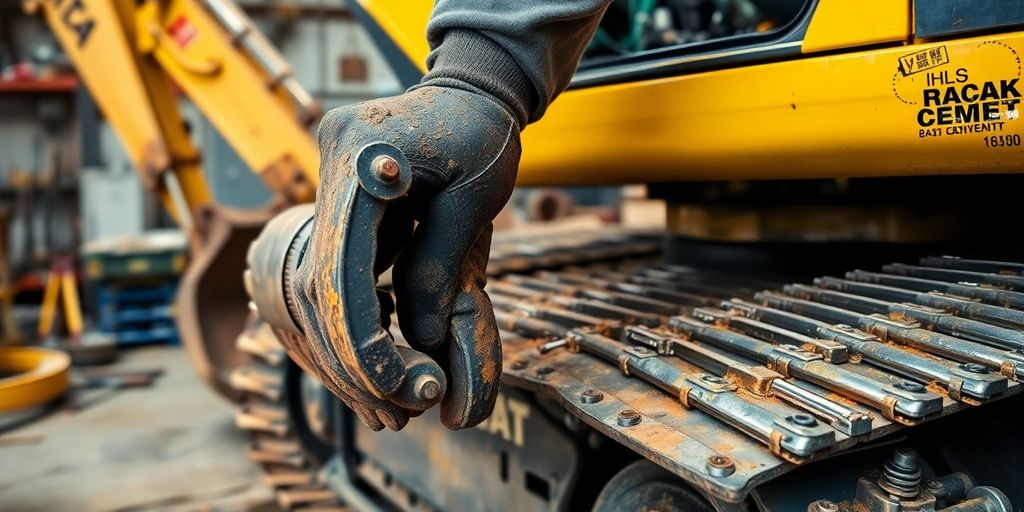
Heavy equipment is vital across many industries, but when it breaks down, it leads to expensive downtime and potential safety issues. Knowing why these machines fail is the first step in keeping them running smoothly. Understanding the root causes of equipment failures is essential for effective maintenance and prevention strategies.
Lack of Regular Maintenance
Skipping regular maintenance is a recipe for disaster. It's like ignoring your car's oil changes – eventually, something big will break. Neglecting fluid servicing, lubrication, and inspections can lead to engine problems, transmission issues, and hydraulic system failures. A good maintenance schedule can extend your equipment's life and improve safety. Regular maintenance is crucial for longevity.
Environmental Factors
Heavy equipment often operates in tough conditions: extreme temperatures, dust, moisture, and rough terrain. These environmental factors can accelerate wear and tear on components. For example, constant exposure to dust can clog filters and damage engines. Similarly, extreme cold can affect the viscosity of fluids, reducing their effectiveness. It's important to consider the operating environment when planning maintenance.
Operating conditions play a significant role in equipment health. Factors like temperature, humidity, and terrain can impact component wear and overall performance. Implementing protective measures and adjusting maintenance schedules based on environmental conditions can help mitigate these risks.
Operator Error
Even the best equipment can suffer from operator error. Improper operation, lack of training, and failure to follow safety protocols can all contribute to equipment failures. For instance, overloading a machine or using it for tasks it wasn't designed for can cause significant damage. Proper training and adherence to safety guidelines are essential for preventing operator-related failures. Here are some common errors:
- Ignoring warning signs
- Improper loading techniques
- Failure to perform pre-operation checks
Preventive Maintenance Strategies
Preventive maintenance is all about stopping problems before they even start. It's like going to the doctor for a check-up – you might feel fine, but they can catch things early. With heavy equipment, this means less downtime and bigger savings in the long run. A solid preventive maintenance program is the backbone of any successful operation.
Scheduled Inspections
Regular inspections are key. Think of it as giving your equipment a regular physical. Walk around, look for anything out of the ordinary – leaks, cracks, loose parts. Don't just glance; really inspect things. A good schedule might include daily checks by the operator, weekly inspections by a mechanic, and more thorough monthly or quarterly reviews. These regular inspections can catch small issues before they become major headaches.
Fluid Servicing
Fluids are the lifeblood of your equipment. Oil, coolant, hydraulic fluid – they all need to be at the right levels and in good condition. Dirty or low fluids can cause serious damage. Make sure to follow the manufacturer's recommendations for fluid changes and use the right type of fluid. Keep a log of when fluids were changed and what type was used. It's also a good idea to take fluid samples periodically to check for contamination or wear. This helps you keep all the parts you use are high quality.
Component Replacement
Everything wears out eventually. Hoses crack, belts fray, filters clog. The key is to replace these components before they fail and cause bigger problems. A good preventive maintenance program includes a schedule for replacing wear items based on hours of use or time. Don't wait until something breaks down; be proactive. Keep track of when components were replaced and what their expected lifespan is. This helps you plan for future replacements and avoid unexpected downtime. Consider using a rebuilt machine parts supplier to save money.
Preventive maintenance isn't just about fixing things; it's about planning and managing your equipment's health. It's about understanding its needs and taking care of it so it can take care of you. It's an investment that pays off in the long run with reduced downtime, lower repair costs, and increased productivity.
Training Operators for Success
It's easy to overlook operator training, but it's a huge deal when it comes to keeping your heavy equipment running smoothly and avoiding costly repairs. A well-trained operator is less likely to misuse equipment, which translates to fewer breakdowns and a longer lifespan for your machines. Plus, it's about safety too. Let's face it, these machines are powerful and dangerous if not handled correctly.
Importance of Proper Training
Proper training is the foundation of safe and efficient equipment operation. It's not just about knowing which levers to pull; it's about understanding the machine's capabilities, limitations, and potential hazards. Untrained operators are more likely to make mistakes that can lead to accidents, damage to equipment, and costly downtime. Think of it like this: would you let someone drive your car without a license? Probably not. The same principle applies to heavy equipment.
Identifying Warning Signs
Operators need to be able to spot potential problems before they turn into major breakdowns. This means training them to recognize unusual noises, vibrations, leaks, or other abnormalities that could indicate a problem. A good operator will know when to stop using a machine and report an issue before it causes serious damage. It's all about being proactive and paying attention to the details. Here's a quick list of things to watch out for:
- Unusual noises (grinding, squealing, knocking)
- Excessive vibrations
- Fluid leaks (oil, coolant, hydraulic fluid)
- Overheating
- Smoke or unusual smells
Safety Protocols
Safety is paramount when operating heavy equipment. Training should cover all relevant safety protocols, including:
- Proper use of personal protective equipment (PPE)
- Safe operating procedures
- Emergency shutdown procedures
- Communication protocols
- Awareness of surroundings and potential hazards
By investing in thorough operator training, you're not only protecting your equipment but also your employees. A safe work environment is a productive work environment, and that starts with making sure everyone knows how to operate the equipment safely and responsibly.
Common Hydraulic System Issues
Hydraulic systems are the lifeblood of much heavy equipment, powering everything from excavator arms to loader buckets. When these systems fail, it can bring your entire operation to a standstill. Understanding common issues and how to address them is key to preventing costly downtime. Let's get into it.
Leak Detection
Leaks are probably the most obvious sign of trouble in a hydraulic system. Even small leaks can indicate bigger problems, like worn seals or damaged hoses. Regular visual inspections are crucial. Look for:
- Puddles of fluid under the equipment
- Damp spots on hoses and fittings
- A sudden drop in hydraulic fluid levels
Early detection is key. Ignoring a small leak can lead to a major failure, potentially damaging other components and costing you more in the long run. Make sure you check the hydraulic systems regularly.
Hose Maintenance
Hoses are under constant pressure and subject to wear and tear from the environment. Regular inspection and timely replacement are essential. Here's what to look for:
- Cracks or abrasions on the hose surface
- Bulges or kinks in the hose
- Leaks at the fittings
It's also important to ensure that hoses are properly routed and supported to prevent rubbing and chafing. Using OEM parts is always a good idea when replacing hoses, as they're designed to withstand the specific pressures and conditions of your equipment.
Fluid Quality Control
Hydraulic fluid isn't just a lubricant; it's the power transmission medium. Contaminated or degraded fluid can cause serious damage to the entire system. Here are some things to keep in mind:
- Use the correct type of fluid as specified by the equipment manufacturer.
- Change the fluid at the recommended intervals.
- Use proper filtration to remove contaminants.
Regularly testing your hydraulic fluid can help you identify problems before they cause major damage. Look for signs of water contamination, excessive wear metals, or a change in viscosity. A simple fluid analysis can save you a lot of money in the long run.
Addressing Electrical System Failures
Electrical issues can really sideline heavy equipment, and they're often more complex than just a dead battery. It's easy to overlook electrical maintenance, but doing so can lead to bigger problems down the road. Let's look at some key areas.
Regular Electrical Inspections
Think of electrical inspections like a check-up for your equipment's nervous system. Catching problems early can prevent major breakdowns. Look for things like frayed wires, loose connections, and corrosion. A simple visual check can save you a lot of trouble. Make sure to check the terminals for corrosion, as this is a common issue.
Battery Maintenance
Batteries are the heart of the electrical system. Keep them clean, charged, and properly connected. Check the terminals for corrosion and make sure the connections are tight. Cold weather can be especially hard on batteries, so consider using a battery tender in the winter. A battery that's not properly maintained can cause all sorts of electrical problems.
Wiring Checks
Wiring is the backbone of the electrical system. Inspect wiring harnesses for damage, wear, and proper routing. Replace any damaged wires immediately. Use dielectric grease on connections to prevent corrosion.
Ignoring wiring issues can lead to shorts, fires, and equipment failure. It's a small thing that can cause big problems. Make sure to check the wiring regularly and address any issues promptly.
Managing External Component Wear
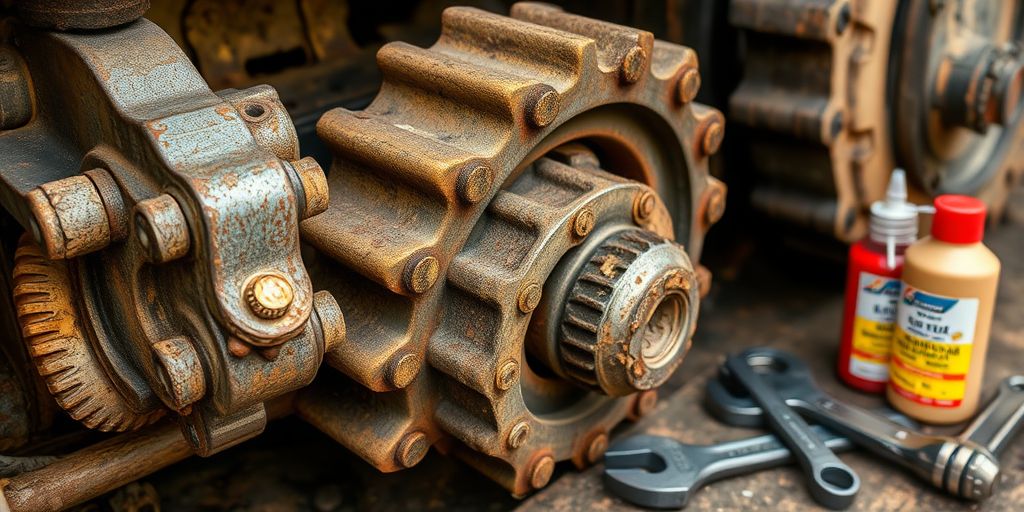
External components on heavy equipment really take a beating. Think about it: loader arms, dozer blades, excavator buckets – they're constantly in contact with abrasive materials. This means they need regular attention to last longer and avoid problems.
Attachment Maintenance
Attachment maintenance is super important. Regularly inspect attachments for signs of wear, like cracks, bends, or excessive thinning. Make sure cutting edges are sharp and properly aligned. If you're dealing with a bucket, check the teeth and replace them when needed. For blades, keep an eye on the wear bars.
Regular Cleaning
Cleaning might seem basic, but it makes a big difference. Dirt, mud, and debris can accelerate wear and tear on external components. Plus, cleaning lets you spot potential problems early. A good power wash can do wonders. Make sure to clean after every use, especially if you're working in harsh conditions. This helps prevent corrosion and keeps things running smoothly. Regular heavy equipment maintenance checklist is key.
Load Management
How you use your equipment matters a lot. Overloading can put excessive stress on external components, leading to premature failure. Always stick to the manufacturer's recommended load limits. Distribute the load evenly to avoid uneven wear. Also, be mindful of how you're operating the equipment. Avoid sudden stops, starts, and jerky movements. Smooth operation reduces stress and extends the life of your components.
Think of your equipment like you would a car. You wouldn't drive it recklessly if you wanted it to last, right? Same goes for heavy equipment. Treat it with respect, and it'll treat you well in return.
The Role of Technology in Equipment Maintenance
Technology is changing how we keep our heavy equipment running. It's not just about fixing things when they break anymore; it's about predicting when they might break and stopping it before it happens. I remember when everything was done with paper and clipboards – what a mess! Now, it's all about data and systems.
Monitoring Systems
These systems track everything from engine temperature to fuel consumption in real-time. It's like having a doctor constantly checking the vital signs of your equipment. You can see potential problems before they become major headaches. For example, a sudden spike in engine temperature could indicate a cooling system issue, allowing you to address it before the engine overheats and causes serious damage. This proactive approach saves time and money in the long run. It also helps in maximizing fleet utilization.
Predictive Maintenance Tools
Predictive maintenance uses data analysis to forecast when equipment might fail. Instead of just reacting to breakdowns, you can schedule maintenance based on actual need. Think of it like this: instead of changing the oil every 3,000 miles no matter what, the system tells you, "Hey, based on how this engine is running, you've got another 500 miles before you really need an oil change." This approach reduces downtime and extends the life of your equipment. To get started, choose one piece of equipment at a time.
Data Analysis for Performance
Data analysis helps you understand how your equipment is performing overall. Are certain machines consistently underperforming? Are some operators harder on the equipment than others? By looking at the data, you can identify areas for improvement and make better decisions about maintenance, training, and resource allocation. It's about regular electrical inspections and understanding the story the data tells.
It's not just about fixing things; it's about understanding the equipment's behavior and making informed decisions. This leads to better performance, reduced downtime, and lower costs. It's a smarter way to manage your fleet.
Here's a simple example of how data analysis can help:
- Identify underperforming equipment.
- Optimize maintenance schedules.
- Improve operator training.
- Reduce fuel consumption.
Wrapping It Up
In the end, keeping your heavy equipment in good shape is all about being proactive. Regular maintenance checks, training your operators, and staying on top of potential issues can save you a lot of headaches down the road. Sure, it might seem like a hassle to schedule those inspections or take the time to train your crew, but trust me, it’s worth it. You’ll avoid those surprise breakdowns that can cost you time and money. So, take a moment to think about your equipment and what you can do to keep it running smoothly. A little effort now can go a long way in preventing those costly repairs later.
Frequently Asked Questions
What are the main reasons heavy equipment fails?
Heavy equipment can fail mainly due to lack of regular maintenance, harsh environmental conditions, and mistakes made by the operators.
How can I prevent my heavy equipment from breaking down?
You can prevent breakdowns by scheduling regular maintenance, training your operators, and keeping an eye on warning signs of wear and tear.
What should I check during a maintenance inspection?
During inspections, check the brakes, hydraulic systems, electrical connections, and any signs of wear on hoses and belts.
How often should I perform maintenance on my heavy equipment?
It’s best to perform maintenance based on the equipment's usage, but generally, regular inspections should be done at least every few months.
What are some common issues with hydraulic systems?
Common hydraulic system problems include leaks, worn hoses, and dirty hydraulic fluid. Regular checks can help catch these issues early.
Why is operator training important for heavy equipment?
Training helps operators understand how to use the equipment properly, recognize warning signs of problems, and follow safety protocols to avoid accidents.