Boosting Factory Efficiency with Advanced Machinery: Strategies for Success in 2024
.png)
In 2024, factories are stepping up their game with new tech. It's not just about getting the latest machines but making them work for you. Think robots, AI, and smart systems that talk to each other. This isn't just about looking cool; it's about getting things done faster and better. This article dives into how factories can boost efficiency with advanced machinery.
Key Takeaways
- Integrating advanced machinery can significantly increase productivity in factories.
- Aligning new machinery with business goals is essential for successful implementation.
- Predictive maintenance helps in reducing downtime and improving machine availability.
- Data-driven decisions enhance operational efficiency and support continuous improvement.
- Upskilling the workforce is crucial for adapting to new technologies and maintaining engagement.
Integrating Advanced Machinery for Enhanced Productivity
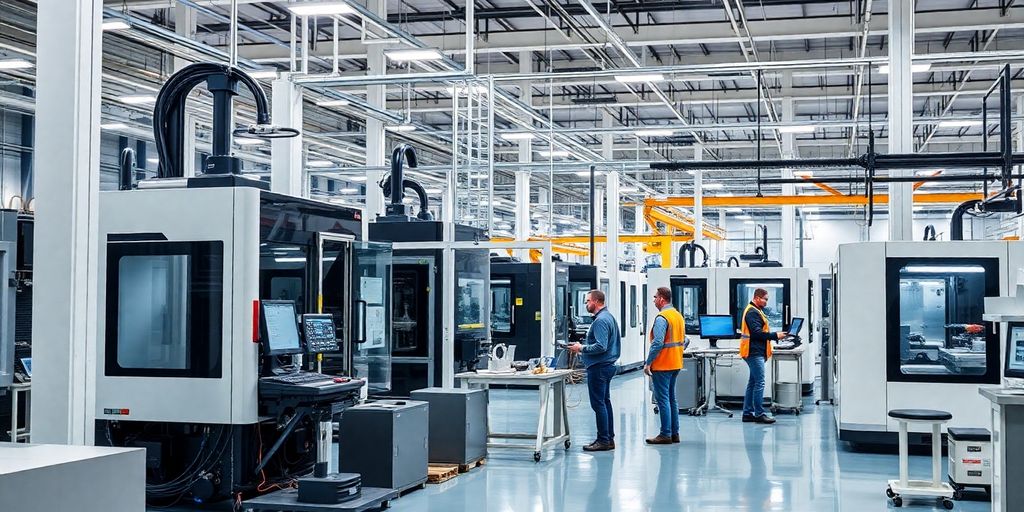
Leveraging Industry 4.0 Technologies
Industry 4.0 is not just a buzzword; it's a game-changer for factories. Imagine a production line where machines communicate seamlessly, adjusting to real-time data and optimizing processes on the fly. This is the power of Industry 4.0 technologies. By integrating these systems, manufacturers can achieve unprecedented levels of efficiency and flexibility.
- Smart Factories: These incorporate technologies like augmented reality (AR) and artificial intelligence (AI), transforming global production and fostering innovation.
- Real-Time Monitoring: Sensors and IoT devices provide continuous feedback, allowing for immediate adjustments and minimizing downtime.
- Data-Driven Decision Making: With access to vast amounts of data, manufacturers can make informed decisions that enhance productivity and reduce waste.
Implementing Robotics and Automation
Robots are no longer confined to science fiction; they're a vital part of modern manufacturing. Automated assembly lines, ranging from simple conveyor belts to sophisticated robotic arms, are taking over repetitive and hazardous tasks.
- Increased Speed and Efficiency: Automation significantly boosts production speed, ensuring consistent product quality and reducing labor costs.
- Safety Improvements: By handling dangerous tasks, robots reduce the risk of workplace injuries, creating a safer environment.
- Cost Savings: Automation reduces the need for manual labor, cutting costs and increasing profit margins.
Utilizing Artificial Intelligence for Process Optimization
Artificial intelligence is revolutionizing how factories operate. AI systems can analyze complex datasets to optimize production processes, predict maintenance needs, and enhance overall efficiency.
- Predictive Maintenance: AI algorithms can foresee equipment failures before they happen, reducing downtime and maintenance costs.
- Quality Control: AI-driven systems ensure products meet high standards by detecting defects early in the manufacturing process.
- Supply Chain Efficiency: AI helps in managing inventory levels, ensuring materials are available when needed, and reducing excess stock.
Embracing advanced machinery isn't just about keeping up with technology; it's about paving the way for a more efficient, productive, and safe manufacturing environment. As we move into 2024, the factories that harness these innovations will lead the industry, setting new standards for success.
Strategies for Successful Machinery Integration
Aligning with Business Objectives
When it comes to integrating new machinery, the first thing you need to do is make sure everything aligns with your business goals. It's not just about getting the latest tech; it's about finding the right fit for your operations. Think of it like getting a tailored suit instead of buying off the rack. You want machinery that complements your existing processes and helps you reach your targets faster.
- Assess Your Needs: Start by evaluating your current production processes and pinpointing any gaps or inefficiencies. Determine what your business goals are and how new machinery can help achieve them.
- Set Clear Objectives: Clearly define what you want to achieve with the new machinery. This could be anything from reducing production time to improving product quality.
- Align Investments: Make sure your machinery investments align with your specific production requirements and long-term objectives.
Ensuring Cross-Functional Collaboration
Getting everyone on the same page is crucial when bringing in new machinery. It's not just the tech team that needs to know what's going on. Everyone from operations to finance should be involved.
- Open Communication: Foster open communication between departments to ensure everyone understands the benefits and challenges of the new machinery.
- Collaborative Planning: Involve different departments in the planning and implementation phases to leverage diverse expertise and insights.
- Regular Updates: Keep the team updated on progress and any changes to the integration plan.
Overcoming Implementation Challenges
Let's face it, bringing in new machinery isn't always smooth sailing. There are hurdles, but with the right approach, they can be overcome.
"The road to successful machinery integration is paved with challenges, but each obstacle is an opportunity for growth."
- Identify Potential Roadblocks: Anticipate potential challenges such as technical issues or resistance to change.
- Develop Contingency Plans: Have backup plans ready to address any unforeseen problems.
- Continuous Training: Provide ongoing training to ensure employees are comfortable and proficient with the new technology.
By focusing on these strategies, companies can not only integrate new machinery more effectively but also optimize procurement processes, ensuring that their investments truly add value to their operations.
Maximizing Efficiency with Predictive Maintenance
Transitioning from Reactive to Predictive Models
Moving from a reactive to a predictive maintenance approach can significantly cut down on unexpected downtimes. Instead of waiting for a machine to break down, predictive maintenance uses data and smart technology to foresee issues before they happen. This shift not only saves time but also reduces costs associated with emergency repairs and production halts.
Utilizing IoT and AI for Maintenance
The predictive maintenance strategy heavily relies on IoT sensors and AI algorithms. These technologies gather real-time data from machinery, analyzing it to predict possible failures. By doing so, they allow for timely maintenance actions, ensuring that machines are always in top working condition. This proactive approach can lead to a smoother operation and less disruption in production lines.
Benefits of Reduced Downtime and Increased Availability
Predictive maintenance offers numerous advantages, with reduced downtime being one of the most significant. By anticipating equipment failures, companies can schedule maintenance during off-peak hours, minimizing the impact on production. This not only keeps the production line running smoothly but also extends the lifespan of the machinery. Increased equipment availability means more consistent production schedules and improved overall efficiency.
Embracing predictive maintenance is like having a crystal ball for your machinery. It tells you when something's about to go wrong, so you can fix it before it breaks. This foresight is invaluable in maintaining a steady workflow and avoiding costly interruptions.
Enhancing Quality Control Through Technology
Implementing Automated Inspection Systems
In today's fast-paced manufacturing world, relying on manual inspection just doesn't cut it anymore. Automated inspection systems are stepping up, offering a way to catch defects quicker and more accurately than ever. These systems use cutting-edge technology like computer vision and AI to scrutinize products at a speed and precision that humans simply can't match. This means fewer errors slip through the cracks, resulting in higher quality products hitting the market.
- Automated inspections lead to consistent quality checks.
- They reduce the need for human oversight, freeing up staff for other tasks.
- Advanced systems can even predict potential defects before they occur.
Utilizing Quality Management Software
Quality management software is another game-changer, providing a centralized hub for all things quality-related. This software allows manufacturers to track quality metrics in real time, offering insights that were previously hard to come by. By integrating with existing systems, it streamlines processes and ensures that quality standards are met consistently across the board.
Ensuring Consistent Product Standards
Maintaining consistent product standards is crucial for building customer trust and brand reputation. With technology, this becomes a more achievable goal. Automated systems and quality management software work hand-in-hand to ensure that each product meets the set standards every single time. This consistency not only boosts customer satisfaction but also reduces waste and rework, saving time and resources.
Embracing digital transformation in quality control isn't just a trend; it's a necessity for manufacturers aiming to enhance efficiency and product quality. By adopting these technologies, companies can stay ahead in the competitive market and ensure their products meet the highest standards possible.
The Role of Data-Driven Decision Making in Modern Manufacturing
In today's manufacturing world, data is king. Having access to real-time data from machines, sensors, and other sources means you can make decisions faster and with more accuracy. This isn't just about collecting data; it's about using it to see what's happening on the factory floor right now. With this information, you can spot problems before they get worse and adjust your operations to keep everything running smoothly.
Improving Operational Efficiency
When you use data to guide your decisions, you're not just guessing what might work best. Instead, you're relying on hard facts to make your factory more efficient. This can lead to shorter production times and less waste, which ultimately saves money. Here are some ways data helps:
- Identifying Bottlenecks: Find out where production slows down and fix it.
- Optimizing Inventory: Keep just the right amount of materials on hand, so you're never overstocked or running out.
- Streamlining Processes: Use data to refine how tasks are done, making operations smoother and quicker.
Facilitating Continuous Improvement
Data doesn't just help you in the moment; it sets the stage for future improvements. By analyzing trends and patterns, manufacturers can predict what changes will benefit them in the long run. This continuous improvement cycle means you're always getting better and staying ahead of the competition.
In the world of manufacturing, staying stagnant is not an option. Embracing data-driven strategies means you're always moving forward, ready to tackle new challenges with confidence.
Empowering Workforce with Advanced Machinery
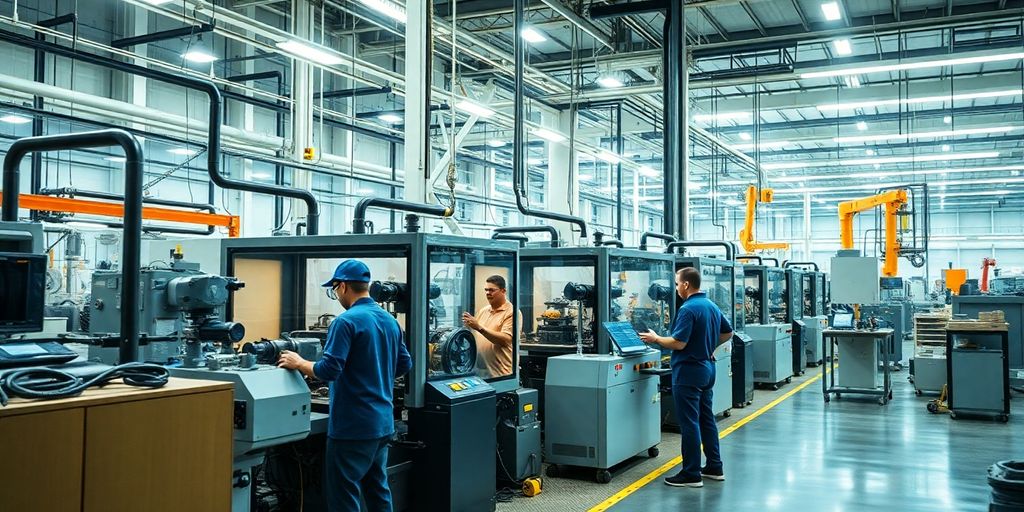
Upskilling Employees for New Technologies
Introducing advanced machinery into the workplace isn't just about upgrading equipment—it's about upgrading skills, too. Employees need to be trained to work alongside these new technologies, which means investing in comprehensive training programs. This isn't just a one-time thing; it's ongoing. You want your team to be comfortable and confident, not just in using the machinery but in troubleshooting and maintaining it. Consider creating a structured training plan that covers everything from basic operation to advanced troubleshooting. This ensures everyone is on the same page and can handle the machinery effectively.
Creating a Culture of Continuous Improvement
To keep up with the fast pace of technological change, fostering a culture of continuous improvement is key. Encourage your team to constantly look for ways to optimize processes and improve efficiency. This might mean regular team meetings to discuss new ideas or implementing a suggestion box for process improvements. By involving your workforce in decision-making, you not only boost morale but also tap into their unique insights and experiences. Remember, the people who work with the machinery every day often have the best ideas for how to improve its use.
Ensuring Employee Engagement and Adaptability
As automation transforms workplaces, it's crucial to create a positive, safe, and engaging culture to attract and retain talent. Employees need to feel valued and part of the bigger picture. This means clear communication about how new machinery fits into the company’s goals and how it benefits them personally. Flexibility in roles and responsibilities can also help, allowing employees to explore different aspects of the technology and find where they excel. Regular feedback sessions and open communication channels can help address any concerns and keep everyone engaged and adaptable to change.
Empowering your workforce with advanced machinery isn't just about the technology—it's about the people who use it. By focusing on training, culture, and engagement, you can ensure that your team not only adapts to change but thrives in it.
Conclusion
So, there you have it. As we look towards 2024, it's clear that boosting factory efficiency isn't just about getting the latest machines. It's about weaving together technology, sustainability, and smart strategies. Companies that jump on this train now, mixing digital tools with traditional know-how, are setting themselves up for big wins. Sure, it's a bit of a puzzle, but the pieces are there. And when they fit together, the payoff is huge—more productivity, less waste, and a factory that's ready for whatever the future throws its way. So, why wait? The future's knocking, and it's time to answer.
Frequently Asked Questions
What is the factory of the future?
The factory of the future is a modernized manufacturing facility that uses advanced technology like AI, robotics, and digital tools to boost productivity and efficiency.
How does predictive maintenance help factories?
Predictive maintenance uses sensors and smart tools to predict when machines might break down, so repairs can be made before problems happen, reducing downtime.
Why is it important to align machinery with business goals?
Aligning machinery with business goals ensures that investments in new equipment support the company's overall strategy, leading to better outcomes and efficiency.
What role does AI play in modern factories?
AI helps factories by analyzing data to optimize processes, improve quality, and make operations more efficient, leading to better productivity.
How can employees adapt to new machinery?
Employees can adapt to new machinery by receiving training and upskilling opportunities, which helps them learn how to use and work alongside advanced technologies.
What is Industry 4.0?
Industry 4.0 is the current trend of automation and data exchange in manufacturing, involving technologies like the Internet of Things (IoT), AI, and robotics.